We may receive a commission when you use our affiliate links. However, this does not impact our recommendations.
Pocket screws are a wonderful thing. They’ve been used to build furniture by everyone from Shakers to Makers. However, using the proper pocket screws in your project is the difference between having a project that’s locked together tightly or one that will strip out, loosen up over time or poke through the side of your project. Here, I want to give you a little bit of guidance on how to select the proper screws for your project.
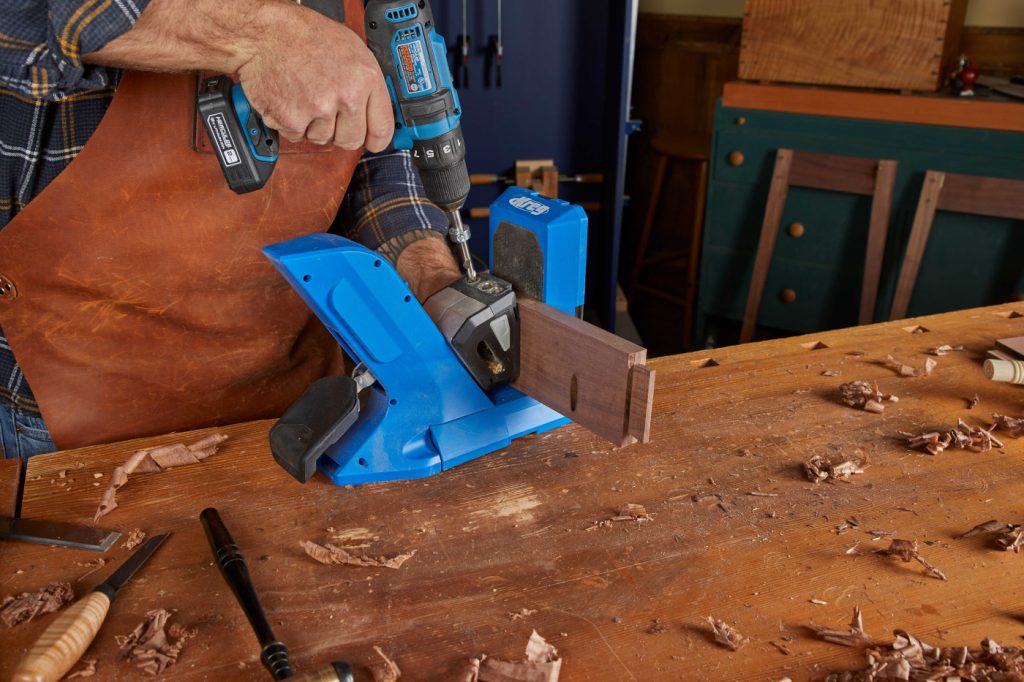
Pocket holes and pocket screws have been used in furniture for hundreds of years.
Pocket Hole Anatomy
When it boils down to it, there are three different things to consider when choosing pocket screws: Length/size, Screw Type (coating), and thread size.
Now, I’m really only talking about screws designed for pocket holes. If you take a look at the photos of the Kreg brand pocket screws below, you’ll notice that every screw is a washer-head type screw (called Maxi-Lock by Kreg) .
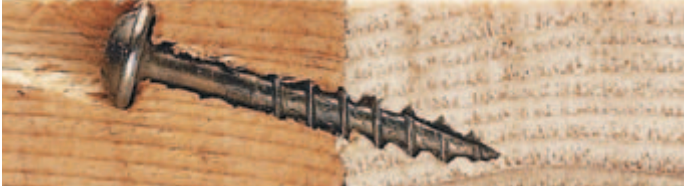
This cut-away shows the inner workings of a pocket hole joint.
As you can see from the cut-away above, drilling a hole with a pocket jig, such as the Kreg 720, you’ll end up with a flat-bottomed, countersunk hole. The flat bottom hole is where the pressure of the joint will be centralized. If you use a standard woodscrew, with a conical head, you will be tightening a wedge into the wood. This can lead to the joint breaking apart as the screw is tightened down, which is obviously a problem. The flat-bottom/Washer head style of pocket hole screws allows for direct pressure to be applied across the joint without fear of splitting. Kreg also offers a pan-head screw that features a smaller shank size, for use in dense hardwood.
In addition, most pocket hole screws will have a self-tapping notch located at the tip of the screw to help “cut” the threads as they’re driven home.
Screw Length and Diameter
As you can see in the cut-away above, a properly sized pocket hole screw is just below the surface of the part. If you choose a screw that’s too long for your project, it’s going to zip through the face of one of your parts. Likewise, a screw that’s too short will not offer sufficient holding power. So, like baby bear’s porridge, it needs to be just right. You can see the different length screws below.

Pocket screw lengths range from 3/4″ (for 1/2″ stock) to 2-1/2″ screws for 1-1/2″ thick material.
For most of my projects, I’m using 3/4″ material. As long as the two pieces being joined are at least 3/4″ thick, I use 1-1/4″ -long screws (Left in photo). As soon as you start jumping up into thicker material, the screws need to become longer. The larger the timbers used for a project, the bigger the strain on the joint. As a rule of thumb, with extra length on pocket hole screws the diameter of the screw increases as well. The XL Pocket hole screws shown on the far right are a prime example. These are designed for use with the Kreg Pocket-Hole XL Jig, and won’t work with standard pocket hole jigs (the diameter of the pilot holes are too small). The 2-1/2″ screws in the center, however, will work with standard pocket hole jigs.
Thread Size
Now that we’ve decided length of the screw you need, now you have to decide whether you want coarse or fine threads on the screw. And you might think “Of course I want coarse threads … They’ll hold better.” Well, yes and no. Coarse threads are indeed larger and hold better in softer woods. Think of woods like pine, cedar (or treated lumber), aspen, poplar, birch, and even plywood and MDF. However, once you get into denser hardwoods, finer threads are better. For Oak, walnut, hickory, cherry, and maple (along with other denser hardwoods), use fine thread. Now, have I been guilty of using coarse threads in hardwoods … I’d deny it, but I’d be lying. However, when I have the correct thread, I do use it. You can see the size difference between the coarse and fine threads in the photos below.
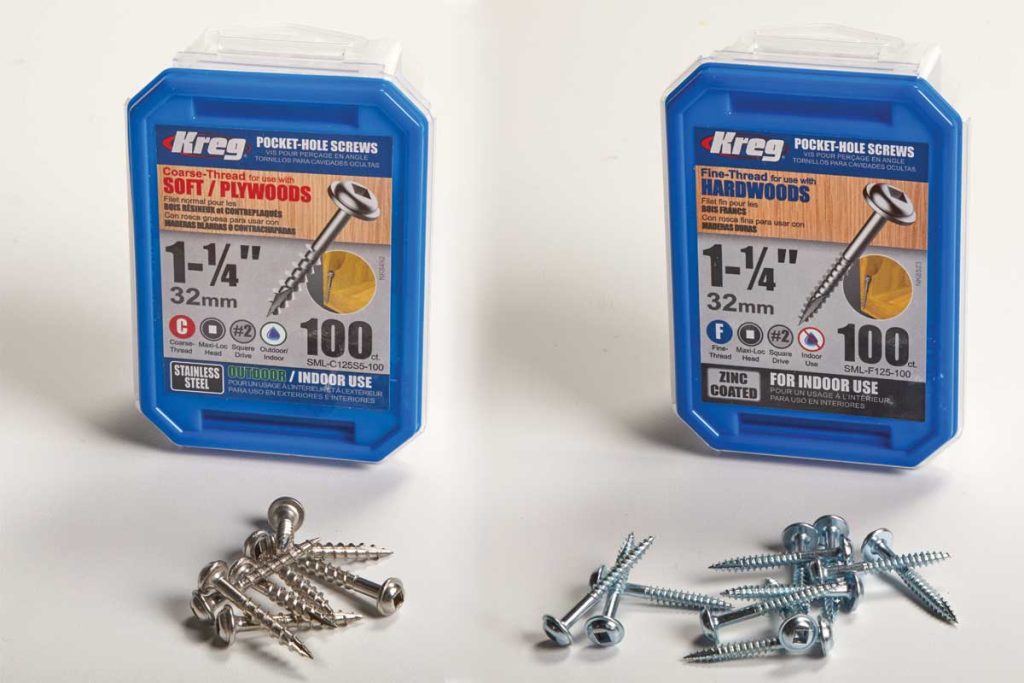
Coarse threads (left) are designed for softwood and plywood. Fine threads (right) are designed for dense hardwood.
Screw Coating type
The final consideration to give to your pocket screw is what type of project are you building? What I mean by that, is the project going to be exposed to weather? If it will, then you’ll want to make sure that your pocket hole screws have some form of protective coating on them. In the above photos, you’ll notice the containers shows what type of coating the screws have in the lower left corner. Some common types are zinc coated, stainless steel, protec-kote and blue-kote.

Stainless Steel (Left), Protec-Kote (Center), and Blue-Kote (right) are three outdoor screw styles offered by Kreg.
For indoor projects, zinc is pretty much all I use. In my opinion, there’s not really any reason to go to anything else. When working on something for outside (a deck, planters, etc.), I want a little more protection. Stainless steel is the ultimate in strength and corrosion resistance. Kreg also offers two different coatings in their Protec-Kote (brown) and Blue-Kote. Both of these offer three layers of anti-corrosion resistance coating.
By picking the correct pocket hole screws for your woodworking project, you’re going to start your project off on the right foot. Still having a bit of problem deciding what screws you should use in your project? Kreg Tool has made a Screw Selection Tool to help easily find which screws you should use.
Happy Building.
Here are some supplies and tools we find essential in our everyday work around the shop. We may receive a commission from sales referred by our links; however, we have carefully selected these products for their usefulness and quality.