We may receive a commission when you use our affiliate links. However, this does not impact our recommendations.
Just as with building any woodworking project, eliminate one step from the manufacturing process
and the results can be fatal.
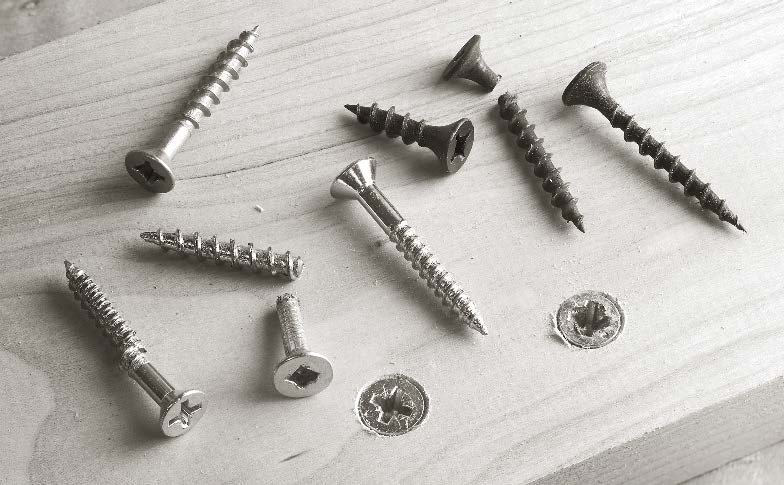
Twisting, bending and breaking are just three of many results you sometimes experience when working with screws. Choose better – not necessarily more expensive – screws to reduce those occurrences.
It usually happens as you hang a door or install a shelf. You’ve got a balancing act going as you hold one piece, steady a second piece and attempt to drive a screw all at the same time. Then, as you snug the screw those final few threads, the connection pulls tight and the screw snaps.
I was curious to find out why some screws break and others don’t. I know what I discovered will amaze you as much as it did me.
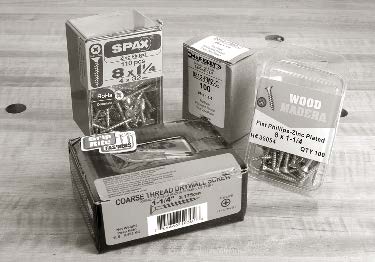
Drywall screws are included in the test due to the ease of acquisition, however I would not consider using these screws when building fine furniture.
I bought four different boxes of screws to test – a common drywall screw (because most woodworkers use this screw as they start woodworking), a zinc-plated screw off the shelf from a home center, as well as a premium square-drive screw from McFeely’s (mcfeelys.com) and a box of Spax screws (also considered premium) purchased online (highlandwoodworking.com).
My first surprise – rest assured there are more to come – was that premium screws were actually cheaper by the piece ($.041) than screws purchased from the home center ($.0447).
Screw Fabrication
How a screw is created is interesting and influences a screw’s strength. Some manufacturers bring in steel stock that is ready to be made into screws while others bring in stock that needs to be pulled and thinned to the appropriate size; bulky material is passed through a series of shaping stations that stretch the stock to arrive at a needed diameter.
Once the material is sized it’s fed into a machine that pounds the stock one time to form the head and a second time (or possibly a third time) to form the recess – the area in the head of a screw for the screwdriver. I’ve been told this process shakes the entire facility floor with each pound.
Head Designs
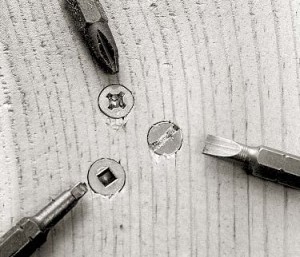
The invention of Phillips and square-drive recesses improved the ease of driving screws. Each reduced the amount of foot-pounds needed to keep the bit engaged with the screw head.
There are many screwhead designs of which the most common used for woodworking is a flat head, where the top of the head is flush with the surface when the screw is properly seated. Other head styles include:
■ Trim head: These are like the flat head but with a smaller diameter flat surface.
■ Oval head: These screws also have a countersink design, but the surface is slightly elliptical in shape.
■ Pan head: A dome-shaped head that stays above the wood’s surface while the flat surface under the head is the bearing surface.
■ Truss head: Similar to a pan head screw, but with a lower head profile and a slightly larger bearing surface.
■ Washer head: This screw has an even larger
bearing surface, used in cabinetry for mounting wall cabinets.
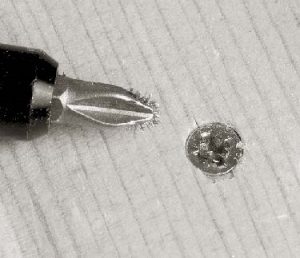
Counterbores and pilot holes help to reduce the tiny amount of shredded steel collected on the tip of the driver, which is a clear indication of “cam-out.”
There are also a few other designs that are found from time to time.
The beveled area just below the head is the countersink. The countersink on wood screws is generally an 80º to 82º angle on American screws. That angle matches most commerically available countersink bits. Again, you occasionally find screws being fabricated with other angles.
Recess Design
The number of recess types available in screws is vast, but I’ve found that woodworkers primarily use three different designs.
The slot head was the first recess used in screws. I choose slot-head screws for most, if not all, of my projects. That’s a decision I make in an attempt to keep true to building reproduction furniture. This oldest of recesses has declined in use over the years because it’s difficult to keep
the screwdriver engaged with the screw recess as significant torque is applied to drive the screws.
It wasn’t until 1936 that Henry Phillips patented the Phillips recess. This recess, sometimes referred to as “cross-drive,” is still popular in the U.S. woodworking industry. The ability to maintain contact between the screwdriver and the Phillips screw recess is greatly enhanced versus the slot screw. People exert approximately 12 foot-pounds of pressure to keep the driver engaged into a Phillips recess. This is the recess design most woodworkers use if they are not concerned with achieving an authentic, antique look.
While the slot head allowed the driver to slip causing damage to the screw’s head, the Phillips recess created a new problem – “cam-out.” Cam-out occurs when the recess is damaged by the screwdriver due to an excessive amount of torque applied while driving a screw.
The third screw recess used in many woodworking shops is the square drive. This design helps to eliminate or substantially reduce cam-out. A square-drive screw requires only about 4 foot-pounds of pressure to keep the driver in contact with the recess as you drive the screw. Therefore, you’re less apt to have the driver slip.
I use square-drive screws for assembling jigs and shop fixtures. Why? I was having trouble with screws breaking and decided to try a deck screw to see if there was a difference. The screws I selected were a square-drive design. There was a difference, but I later found out it wasn’t due to the recess. It was a difference in screws. Read on.
Thread Styles
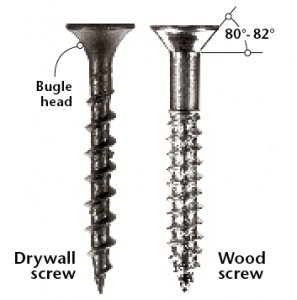
A countersink on a wood screw (right) is tapered at 80º-82º in the U.S. (90° in the U.K.), while the countersink on a typical drywall screw (left) is slightly concave or of a “bugle” design.
After the head and recess is formed, screws are cut to length, then threads are added. Historically, threads were cut into the shank of the screws – this left the outer diameter of the threads equal to the diameter of the shank (a great method for dating screws pulled from older furniture). Today, threads are pressed into the shanks. As a result, the thread profile extends beyond the diameter of the shank.
To illustrate how threads are added to screws, place your hands in a prayer position then slide your right hand back so the tips of your fingers are at the palm of your left hand. In this example your right hand is the thread-cutting tool while the left hand is the screw. Now, apply pressure with your right hand and slide it forward across your left hand.
Thread patterns for woodscrews have traditionally been a “single lead,” or one parallel thread, wrapped around the length of the screw. This design is still the most-used thread style in woodworking screws.
Due to the use of particleboard in the furniture industry (isn’t that a lovely thought), deep-thread screws were introduced. This thread design has a thinner shank and deeper threads set at a sharper angle. Deep-thread screws are said to hold better in composite woods and drive with less splitting, bursting or displacement of material.
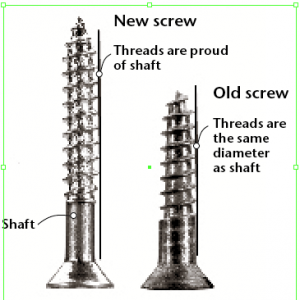
As the process of creating threads on screws evolved, the relationship of thread size to screw shaft changed. The threads on the right screw were cut into the shaft leaving, the thread diameter equal with the shaft. Threads on new screws (the screw on the left) are pressed into the shaft causing the thread diameter to be larger that that of the shaft.
Another thread design is “double lead” where two parallel threads circle the shank, originating at the point of the screw. The double-lead thread design produces more threads per inch. As a result, screws drive faster. However, double-lead threads are primarily used on screws longer than 3-1⁄2″ in length. The double lead provides stability to the screw in the heat-treating process, reducing the screw’s tendency to bend.
Heat Treatment: The Next Step
With the threads created, screws travel through a heat-treating process. Heat-treating is the most important step in making screws that are strong or weak. (Another element that increases strength is the ingredients of the raw materials from which the screws are made.)
Heat-treating is accomplished using a variety of methods. The best method is to separate the screws into smaller portions, as in hoppers, and run the screws through the process. This method allows the screws to travel more evenly, ensuring each screw is heat-treated properly. To increase that efficiency even more, some manufacturers shake the conveyor belt as the screws ride along. Shaking allows the screws to mix and heat more evenly.
The temperature in heat-treating varies somewhat by the length of screw being made, but as a general rule the furnace temperature is near 1,600º Fahrenheit. A temperature far in excess of 1,600ºF causes the screws to be more brittle. If they’re too brittle, they tend to snap when driven.
Here’s the Shocker!
Heat-treating is not done on all screws. One of the single-most important steps used to build strength in screws is left out of the process by some manufacturers. This is the main reason some screws break and others do not.
Drywall Screws
The properties we’ve discussed so far relate to wood screws. Contrary to what you read or hear, drywall screws are not wood screws and should not be used in woodworking projects for a number of reasons.
Besides being heat-treated at a higher temperature and being brittle, drywall screws have a smooth “bugle head” – a curved transition between the shank and head. This design is to keep the screw head from breaking the paper of drywall wallboard (the only true use for drywall screws.) In addition, the countersink of the drywall screw does not match the recess made when using a typical countersink bit.
Also, drywall screws generally have thin shanks equal to the size of a #6 wood screw and oversized heads that are the size of a #8 wood screw. The oversized head helps to minimize tearing through the drywall’s paper face as well.
It’s easy to understand that if you tighten a screw with those characteristics, it’s more likely to break when driven into wood. The bugle-head design doesn’t fit the countersink and the thin shank reaches a point of stress prior to the larger head being properly seated.
About Our Testing
The test was to drive a number of each screw, keeping track of the screws that break or cam-out when being driven. When you install screws in your work, you should always drill a countersink. For the test however, I simply drove the screws into maple. No countersink. No starter hole of any kind. This keeps the test on a level playing field.
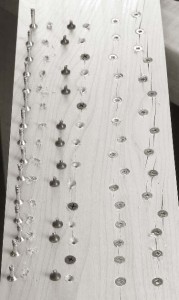
Proper heat-treating is extremely important in wood screws. The results of the test clearly demonstrate the effect of this manufacturing step. Premium screws, the right-most two rows, not only seated fully into the maple, they seated with enough force to start splits in the wood.
Surprise, Surprise
Because I have years of experience working with screws and because I’m a bit of a skeptic, I had a notion as to what to expect. Let me say, I wasn’t surprised with the results of the test. But I was aghast at the severity of difference.
I began the test by driving five home-center screws. All five screws broke. They didn’t just break as the countersink made contact with the maple; the screws broke near the mid-point in length. Not one screw seated properly. Wow.
Not wanting to reach a quick conclusion (albeit difficult given the results), I continued to drive home-center screw after home-center screw. In the end, all 20 screws fell victim to the same type of destruction.
The next contenders were the drywall screws. I expected the same results. Again, I was surprised. Drywall screws held up better than the home-center wood screws, but not by much. I drove 20 drywall screws to find that only four screws were equal to the challenge. Interestingly, most of the drywall screws reached the countersink portion of the screw, then broke. Clearly, this reinforces earlier statements.
Better Screws Beget Better Results
Down to the final two contenders. I wondered if these screws could withstand the test. After all, maple is a hard wood. Maybe I would experience all screws failing and need to start at the beginning and rethink the test.
Upon driving the first Spax screw, I knew the test would not need to be repeated. This premium screw drove easily. As the countersink portion of the screw reached the maple, the screw properly seated – as a screw should. The head was flush with the hardwood. Of the 20 screws tested, all 20 screws seated without any evidence of breakage or recess damage.
Did the less-costly McFeely’s premium screws, the most inexpensive screws in the test, compare well to the Spax? You bet they did. Again, I drove 20 screws; all seated perfectly and held firm. The McFeely’s screws, like the Spax, showed no signs of breakage or recess damage.
I expected the premium screws to test better than the others, but I expected at least a few to break during the test. Neither screw, the Spax nor the McFeely’s, flinched at the job. That surprised me.
From now on I’ll make sure to have so-called premium screws from Spax or McFeely’s on hand. Not only can you save money with the purchase, you save time and headaches in the shop while building your project. And that’s a savings of which I’m happy to take advantage.
— by Glen D. Huey
• From Woodworking Magazine, Summer 2008, which also includes “A Better Design for a Blanket Chests,” “Better Finger Joints,” “Trim End Grain Proud,” “A Simple Sea Chest,” “The Best Crackle Finish” plus Letters, Shortcuts and more.
Here are some supplies and tools we find essential in our everyday work around the shop. We may receive a commission from sales referred by our links; however, we have carefully selected these products for their usefulness and quality.