This workbench has a top ready for hard use. But it’s the base that catches your eye. The interlocking joinery, with its dovetails and wedges, is rock solid, yet it knocks down quickly for moving.
Although it looks complicated, the base is surprisingly easy to build. It’s made from multiples of only five parts that fit
together like the pieces of a puzzle. The
fancy joinery that locks the pieces in
place is nothing more than strategically
located rabbets and dadoes, and they’re
all made on the tablesaw.
Unlock the Joinery
The key to successfully building this base is knowing the
sequence of the saw cuts, shown here as lettered steps. If you
approach building it one cut at a time, following the steps,
you’ll have it assembled before you know it.
First, fit the brackets to the tops of the legs with slots and
dadoes (Steps A and B). Set the brackets aside.
Next, fit the end rails to the legs with half-lap, dado and
bevel cuts (Steps C – F). Before gluing them together, make
dadoes in the end rails to house the side rails (Step G).
After the end assemblies are glued, cut the tenons on the
side rails so they fit between the end rails (Step H). Then cut
dadoes in the end assemblies (Step J) for the wedges.
Make the wedges (Step K) and then lay out and cut the
angled dadoes on the side rails that hold them (Steps L and
M). Assemble the base, lock it together by tapping the
wedge home (Step N) and slide the top brackets in place.
You’ll need 25
board feet of 8/4 and 15 board feet of 6/4 stock. Additional
6/4 and 8/4 scrap stock in any wood is helpful for test cuts.
Your shop needs to be equipped with a well-adjusted jointer,
planer and tablesaw. You’ll also need an accurate, adjustable
try square. For layout work you’ll need a stack dado set that
cuts flat bottoms, a tapering jig for the wedges and brackets,
a sharp chisel and a router and chamfering bit.
Make or Buy the Top
When it comes to the top, you have two choices. You can
buy one ready-made (see Sources, below), or make your own. Manufactured workbench tops are hard to find, come in
limited sizes and are expensive to ship. Butcherblock countertops
are widely available, but are always only 1-1⁄2-in.
thick and often include short butt-joined pieces.
Making your own top is a lot of work and you won’t save
yourself much money. Satisfaction, quality control and
choosing specific dimensions, especially the thickness, are
good reasons to do it.
I made this one from plainsawn 8/4 boards, all 8-ft. long
and about 6-in. wide (72 board ft.) I milled them to 1-3⁄4-
in. thickness and ripped them in half. After jointing the edges,
I ripped the boards to a consistent width, as wide as the narrowest
piece. Then I glued them together face to face, quartersawn
edges up, in three sections, each about 10-1⁄2-in.
wide. I ran these sections through the planer to make them
smooth and of uniform thickness. Then I jointed the edges and carefully glued these sections together to make the
top. I cut the ends square with a straightedge-guided saw.
Other Possibilities
Upon seeing it, one of my friends said, “That’s not a
workbench, it’s a table.” He’s right—half right, anyway.
The bench could also be used as a kitchen or gardening
work table. And with minor modification it would make
a great dining or coffee table. Just imagine the base under
a glass top. But be prepared to keep the glass clean of nose
prints from guests seeking a closer look at your exquisite
joinery!
Sources
(Note: This information may have changed since this story's original publication date.)
Woodcraft Supply, woodcraft.com, 800-225-1153, 1-3/4" Thick Laminated Maple Bench Tops, 30" x 60", #145686, $270, 1-3/4" x 24" x 60", #145685, $250, 24" x 84", #145687, $300.
Your local home center or lumberyard, Butcherblock Countertops.
Bench Dimensions and Cutting List

This story originally appeared in American Woodworker October 1999, Issue #75.

|
|
Click on any image to view a larger version.
Make the Top Bracket


1. Cut slots centered in the top of each leg for the brackets
that hold the top (Step A).To keep the leg steady, attach a tall
auxiliary fence to your saw’s rip fence and clamp the leg to a
good-sized rectangular block. Use a featherboard and make the
cut in several shallow passes until you reach the maximum
depth your dado set allows (21⁄8-in., in this case).

2. Cut dadoes on both sides of each top bracket so they
can slip into the dadoes in the leg tops (Step B). Stop blocks at
each end of the miter fence control the width of the cut.
Make the End Assemblies


3. Bevel the edges of each end rail at a 9-degree angle
(Step E).These cuts turn the tongues into big dovetail pins.
Leave a 1⁄4-in. wide flat on the back edge of the rail to ride
against the fence.

4. Make angled cuts at the
reference points, turning the leg
dadoes into tails (Step F).Then nibble
away the remaining waste. After cutting
the angle on one side of each dado, flip
the leg over and stand the end rail on the
leg. Align the pin with the unfinished tail, and
mark the leg for the remaining angled cut.
(Inset) Set the height of the blade for cutting the
dovetail corners by raising it so that its teeth barely nick the
top of the dado.

5. Pare the waste from the angled saw cuts with a sharp,
wide chisel to finish the corner.
House the Side Rail


6. Cut a dado (Step G) in each end rail, starting from the
shoulder of the half-lap. Make it wide enough to house the
side rail.
Final Assembly


7. Mark the location of the angled dado in the side rail
that will hold the wedge. Slide the side rail into position and
use the end assembly dado for reference.

8. Lay out the side rail wedge dado from the L-shaped mark
you’ve just made (Photo 7). Its leg gives you the depth and its
stem marks the back of the wedge. Extend the dado a bit behind
this line for clearance. Draw the angled front using one of your
wedges held tight against a try square.You can remove most of
the waste from this dado with straight, 90-degree cuts (Step L).

9. Make the final angled cuts in the side rail (Step M). Use
one of the wedges clamped between the rail and the miter
gauge to guarantee that the angle of the dado and the wedge
match perfectly.
The Wedge


10. Slide the wedge home (Step N). Once it has engaged
the dado in the lower end rail, tap it securely into place.
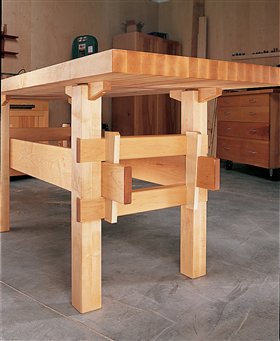
|