We may receive a commission when you use our affiliate links. However, this does not impact our recommendations.
Design without compromise: An exercise in high-end handwork.
Sometimes a cup of tea is more than a cup of tea. Its surface may be still, its color translucent and its container unadorned. But in a single sip of hot water, you can taste the time of year the leaves were harvested, the sun that touched them from above and the earth drawn into them from below.
This is not so different from woodworking. As woodworkers, we’re concerned with transforming natural materials into creations of our own, hoping all the while that they retain some of the unimaginable complexity of their former lives. This project, a sideboard for preparing tea, is an opportunity to unite two arts, both of which celebrate simplicity and reflection and, in the modern spirit, are capable of presenting both calm, unassuming surfaces and the living forces roiling in their depths.
To achieve this in the form of a standing cabinet, my guiding principle has been to take away all that is extraneous and leave only what is necessary. The cabinet is made from pale, straight-grained Spessart oak – aesthetically calming and unobtrusive. Symbolically, too, it seems in keeping that a piece meant for quiet, contemplative moments be made from ancient, slow-growing timbers. In addition to the careful selection of lumber, the components are as thin as practicable; the outer box is 5⁄8” thick, while most of the interior dividers are a relatively wispy 3⁄8“.
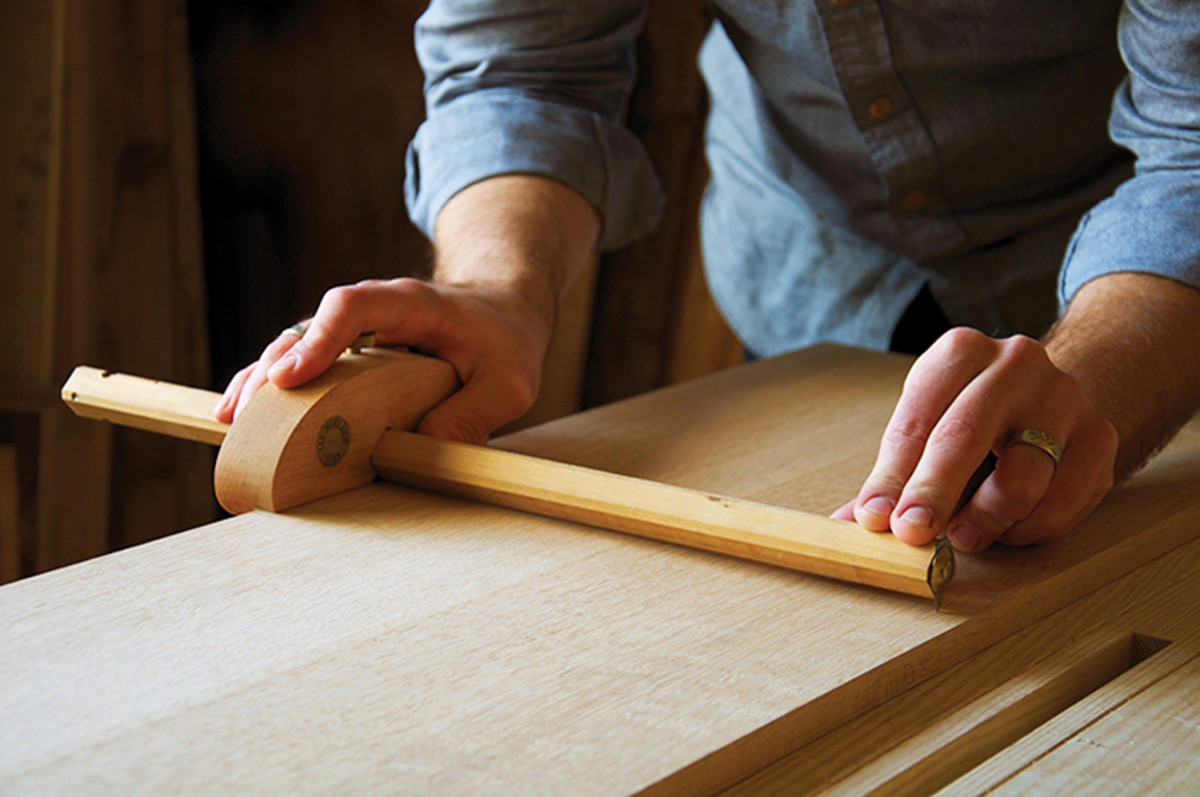
Properly gauged. A panel gauge keeps the cabinet’s outer parts a consistent width, making it easier to align the grain at the corners.
The soul of the piece is the left-most cubby, intended to hold a cherished teapot or bowl. In contrast to the austerity of the cubby, the right section of the cabinet is filled with dividers and drawers that intersect to form muted patterns. In other words, the fullness of the right section enhances the emptiness of the left.
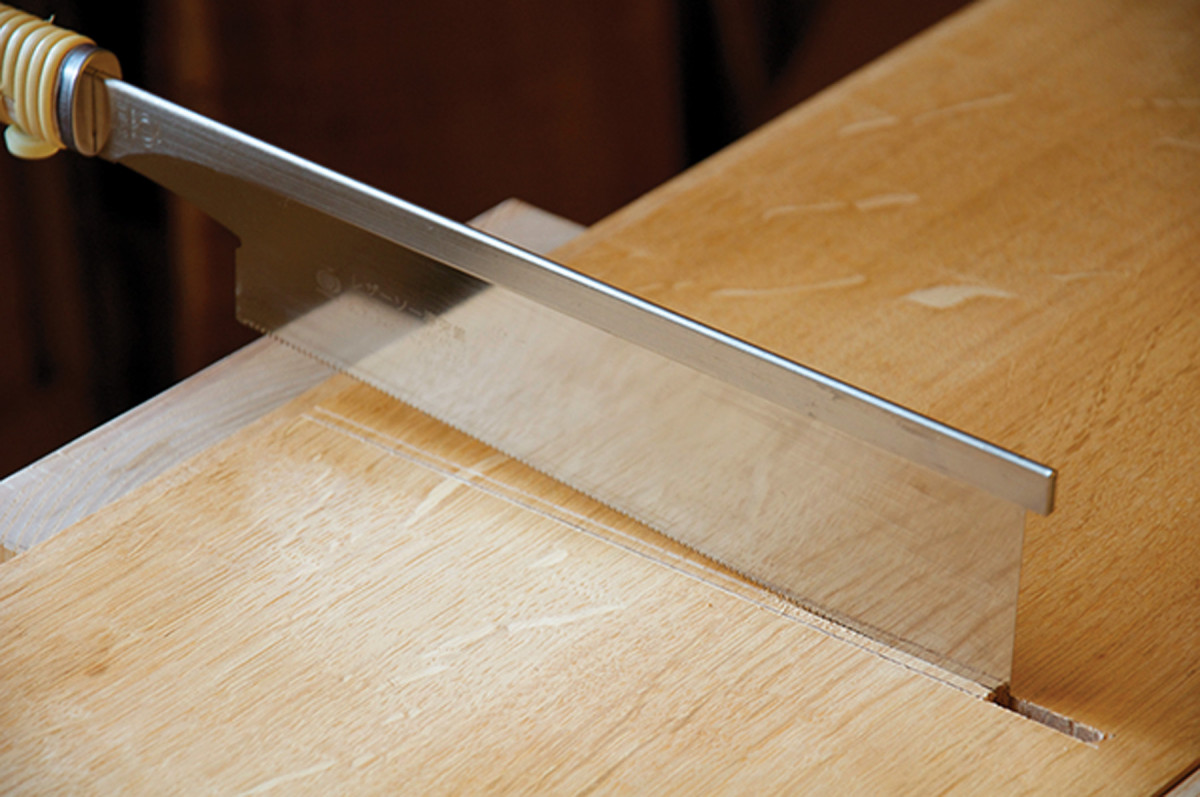
Saw the dados. Make the case’s deep, narrow dados by sawing their full length and depth just inside the layout lines.
In addition, the dividers and drawers are progressively set back from the cabinet’s front edge. The varying shadows they cast hint at the richness and mystery of an organizing principle expressed through otherwise simple shapes. They point, too, at function: a stately teapot resides in the deepest space, cups on a slightly narrower shelf, and spoons and whisks in even smaller drawers.
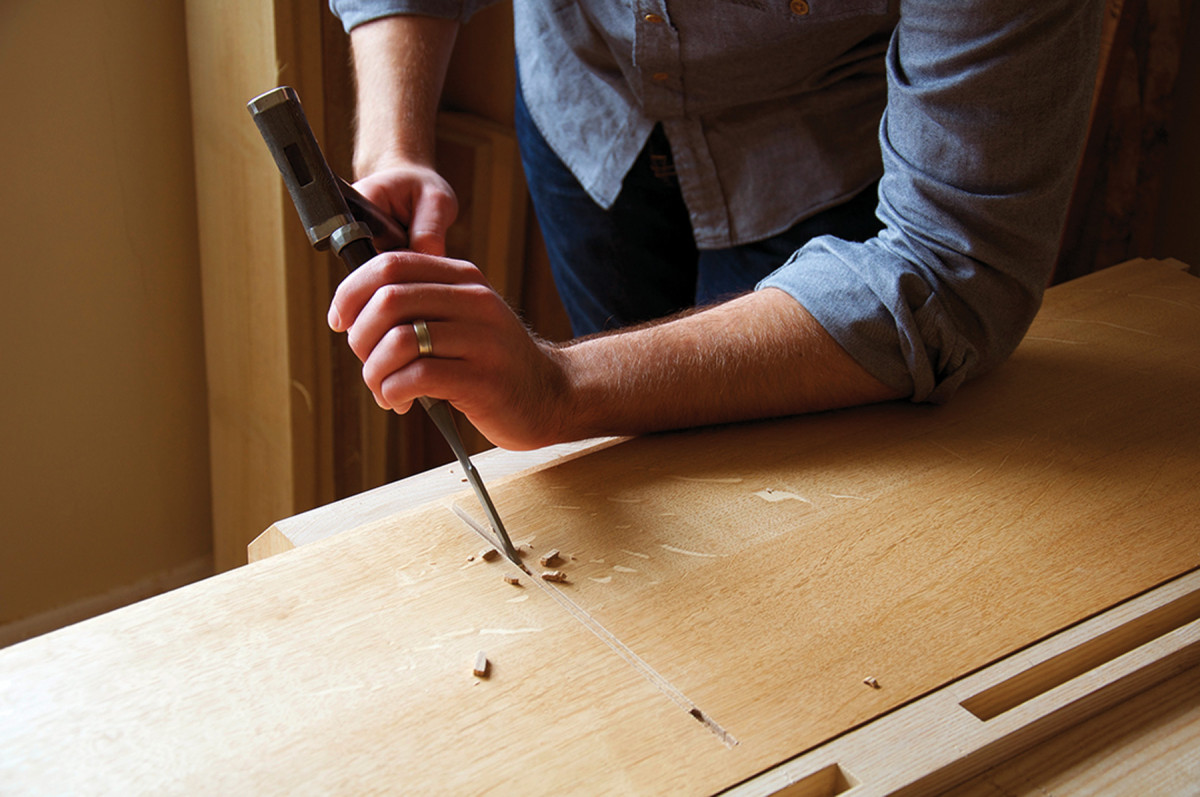
Entrenched. Clear the waste with a chisel driven by a mallet.
Because the rectangular case is the focus of the piece, the legs are designed to visually intrude as little as possible, while at the same time providing a subtle feeling of lift and sturdiness. While there’s nothing new under the sun, they’re attached by means of a somewhat unusual joint that allows for a minimal base, and they’re tapered, curved and rounded to soften their form.
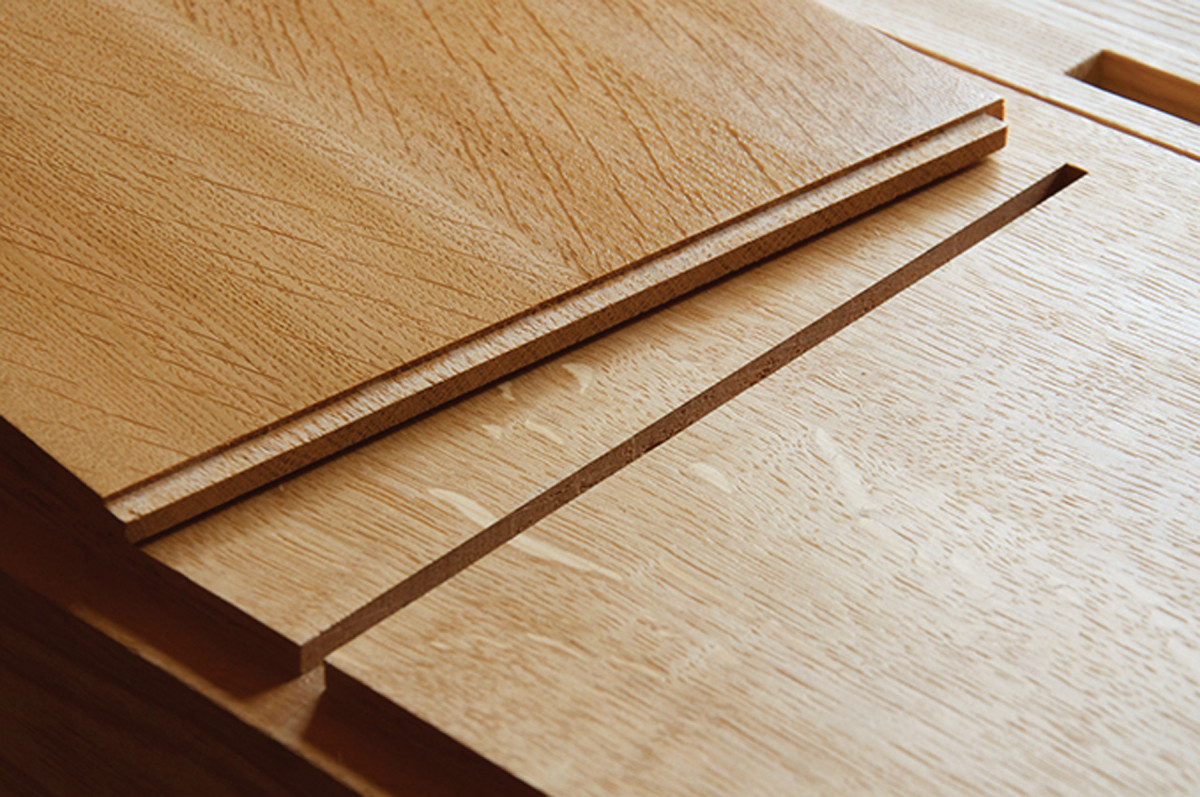
Division by dados. The vertical divider separating the left and right sides of the cabinet has 1⁄4″ tenons that slip into dados in the cabinet top and bottom.
In this article, I’ll briefly touch on constructing the main case, provide a step-by-step explanation of cutting the leg joint, and walk you through making the back’s mitered joints. I use hand tools exclusively to perform these tasks, a method that seems to suit the quiet, intentional spirit of tea.
Make the Case
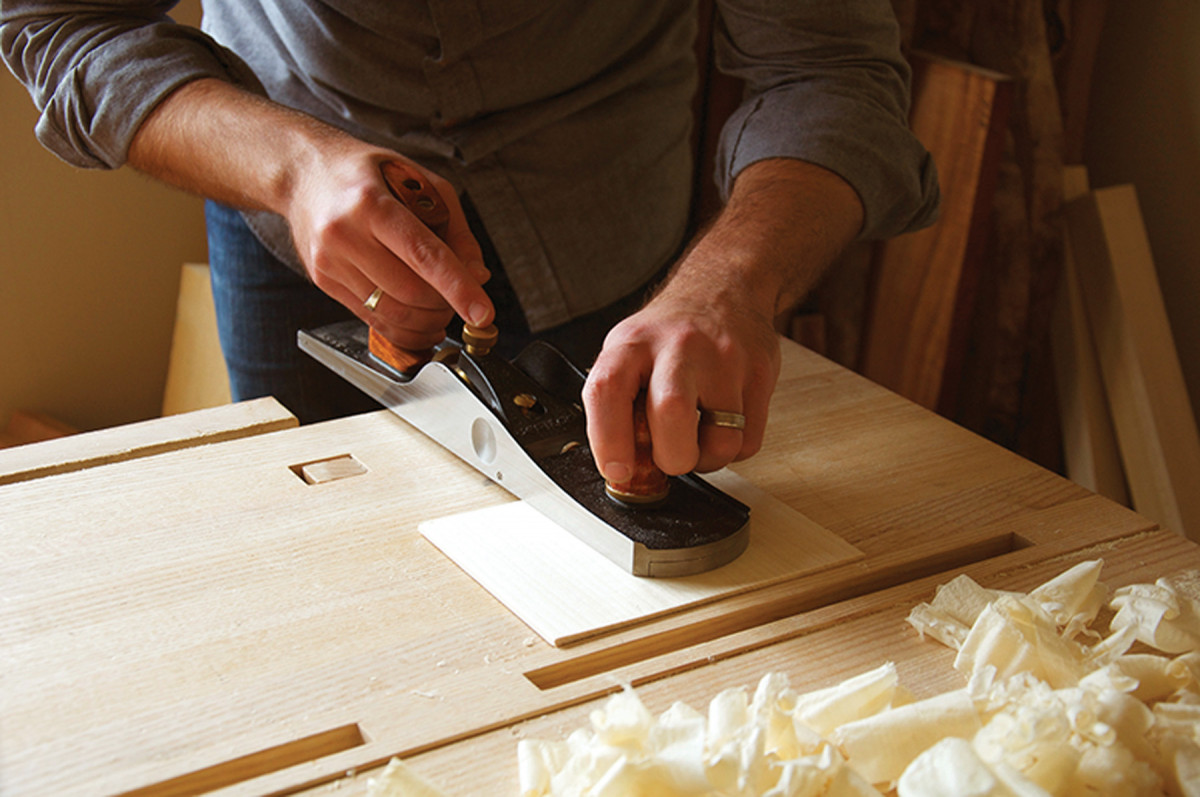
Thin shavings. Holding thin pieces such as the 1⁄8″ dust panels can be challenging. I plane them using a stop in my bench.
The four sides of the outer case are joined together with mitered, full-blind dovetails, which allow the grain of a single piece of oak to flow seamlessly around its corners with minimal distraction. The case is built with traditional joinery techniques, but two details are of note.
The second layer of drawers rides on a frame that includes dust panels between the runners. While this might seem extravagant, it simplifies construction in addition to adding a bit of flair. Grooves in the frame not only house the panels, but also make sufficient mortises for short, 1⁄8“-thick tenons cut into the ends of the runners. This means you can make two joints in one operation.
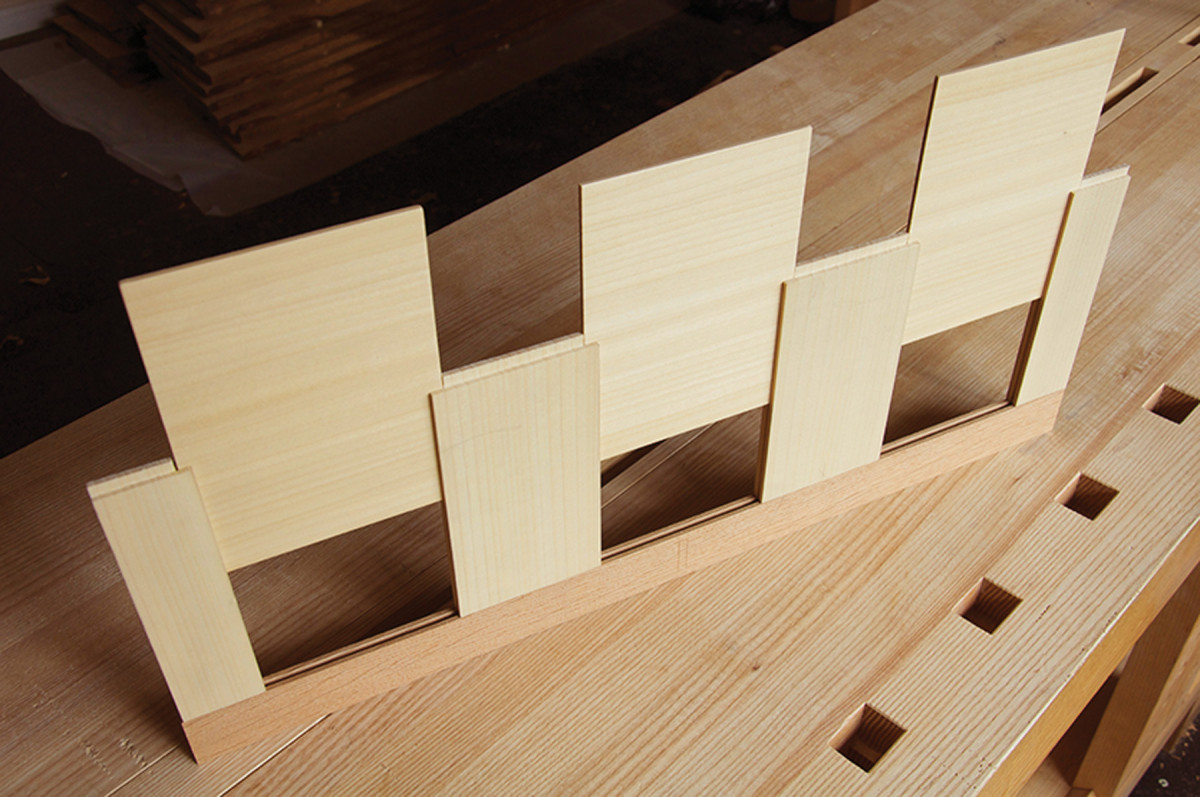
Two-for-one joinery. Both the dust panels and runners of the upper drawer frame slip into the same 1⁄8″ grooves cut into the front and rear dividers.
Installation of the vertical drawer dividers is also slightly unorthodox. First, slide the drawer frame and the cup shelf into place. Then carefully but confidently bend the drawer frame upward to accommodate the lower vertical divider’s 3⁄32” tenons. Do the same for the next layer. This is as terrifying in practice as it is in print, but if you fight through the inevitable shortness of breath, the dividers will lock into place and create a very rigid framework.
Sideboard Fit for Tea Cut List
No. Item Dimensions (inches) Material Comments
t w l
Case & legs
❏ 1 Top 5⁄8 x 10 7⁄8 x 36 1⁄4 Oak
❏ 1 Bottom 5⁄8 x 10 7⁄8 x 36 1⁄4 Oak
❏ 2 Sides 5⁄8 x 10 7⁄8 x 10 3⁄8 Oak
❏ 1 Vertical divider 3⁄8 x 9 3⁄4 x 9 3⁄4 Oak 5⁄16” TBE*
❏ 1 Cup shelf 3⁄8 x 9 1⁄2 x 22 7⁄8 Oak
❏ 1 Drawer frame, front 3⁄8 x 1 1⁄2 x 22 7⁄8 Oak
❏ 1 Drawer frame, back 3⁄8 x 1 1⁄2 x 22 7⁄8 Poplar
❏ 2 Frame runners, outside 3⁄8 x 11 1⁄16 x 6 7⁄8 Poplar 1⁄4” TBE*
❏ 2 Frame runners, center 3⁄8 x 3 3⁄8 x 6 7⁄8 Poplar 1⁄4” TBE*
❏ 3 Dust panels 1⁄8 x 6 5⁄8 x 4 13⁄16 Poplar
❏ 1 Drawer rail, front 3⁄8 x 1 1⁄2 x 22 1⁄2 Oak
❏ 1 Drawer rail, back 3⁄8 x 1 1⁄2 x 22 1⁄2 Poplar
❏ 2 Drawer runners, outside 3⁄8 x 6 3⁄8 x 1 1⁄2 Poplar **
❏ 1 Drawer runner, center 3⁄8 x 6 3⁄8 x 3 3⁄8 Poplar **
❏ 1 Vertical drawer divider 3⁄8 x 1 3⁄8 x 2 5⁄8 Oak 1⁄8” TBE*
❏ 2 Vertical drawer dividers 3⁄8 x 1 3⁄8 x 2 1⁄4 Oak 1⁄8” TBE*
❏ 4 Cup dividers 3⁄16 x 8 7⁄8 x 3 7⁄8 Oak
❏ 10 Drawer stops 1⁄4 x 1 x 1⁄4 Oak
❏ 4 Legs 1 1⁄8 x 2 1⁄4 x 34 Oak
Back
❏ 2 Rails 1⁄2 x 1 5⁄16 35 5⁄8 Oak
❏ 2 Stiles, outside 1⁄2 x 1 5⁄16 x 9 3⁄4 Oak
❏ 1 Stiles, center 1⁄2 x 2 5⁄8 x 9 3⁄4 Oak
❏ 1 Panel 1⁄4 x 20 11⁄16 x 7 5⁄8 Oak
❏ 6 Wide slats 5⁄16 x 7⁄8 x 7 3⁄8 Oak 1⁄8” TBE*
❏ 3 Narrow slats 5⁄16 x 3⁄8 x 7 3⁄8 Oak 1⁄8” TBE*
Drawers
❏ 2 Fronts 3⁄8 x 2 3⁄8 x 11 1⁄16 Oak
❏ 2 Backs 3⁄8 x 2 3⁄8 x 11 1⁄16 Poplar
❏ 4 Sides 5⁄16 x 2 3⁄8 x 9 Poplar
❏ 2 Slips 5⁄8 x 1⁄2 x 10 7⁄16 Oak Miter, glue to fronts
❏ 4 Slips 5⁄8 x 1⁄2 x 8 3⁄4 Poplar Miter, glue to sides
❏ 2 Bottoms 1⁄4 x 8 3⁄4 x 9 15⁄16 Poplar
❏ 3 Fronts 3⁄8 x 2 x 7 1⁄4 Oak
❏ 3 Backs 3⁄8 x 2 x 7 1⁄4Poplar
❏ 6 Sides 5⁄16 x 2 x 9Poplar
❏ 3 Slips 5⁄8 x 3⁄8 x 6 5⁄8 Oak Miter, glue to fronts
❏ 6 Slips 5⁄8 x 3⁄8 x 8 3⁄4 Poplar Miter, glue to sides
❏ 3 Bottoms 1⁄4 x 8 13⁄16 x 6 1⁄4 Poplar
❏ 2 Pulls 3⁄16 x 3⁄8 x 6 3⁄8 Ebony †
❏ 3 Pulls 3⁄16 x 3⁄8 x 2 9⁄16 Ebony †
*TBE = Tenon both ends; **Cut from wide stock – grain runs side to side in final orientation so there are no cross-grain gluing concerns when attaching runners to case bottom; †3⁄16” tenon into drawer fronts
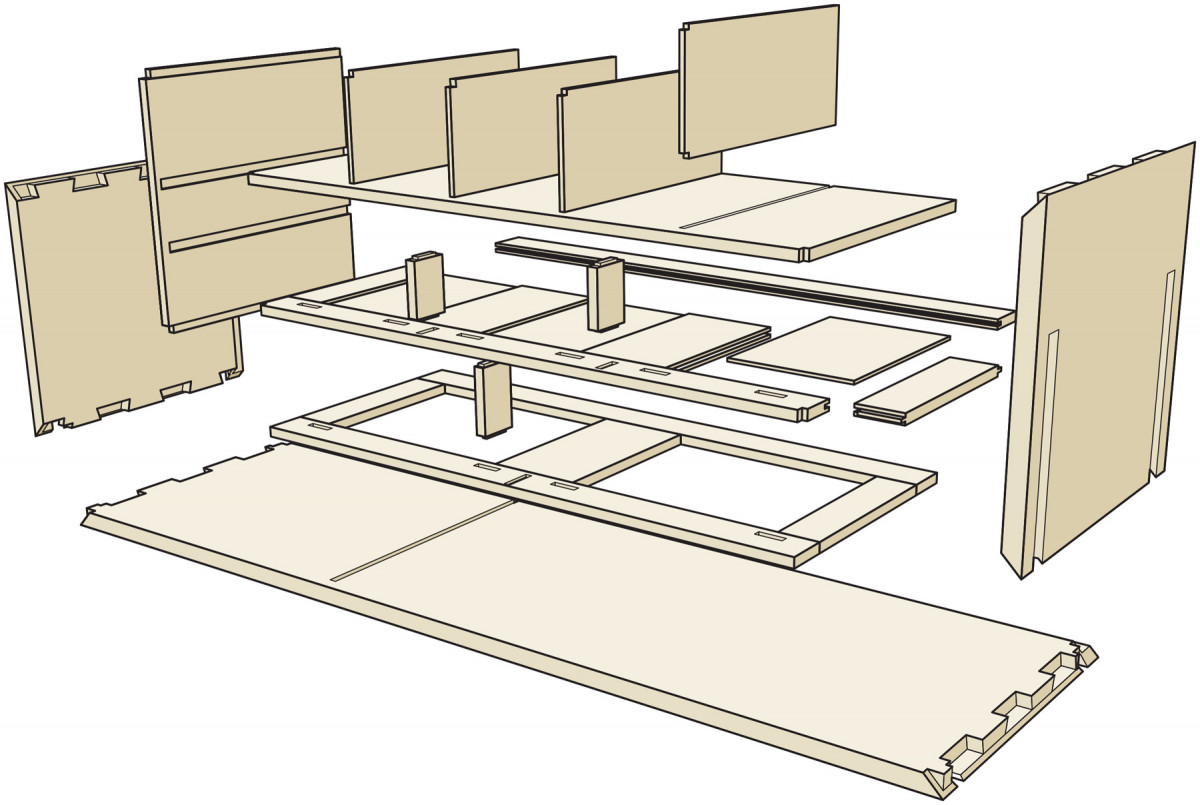
Carcase Exploded View
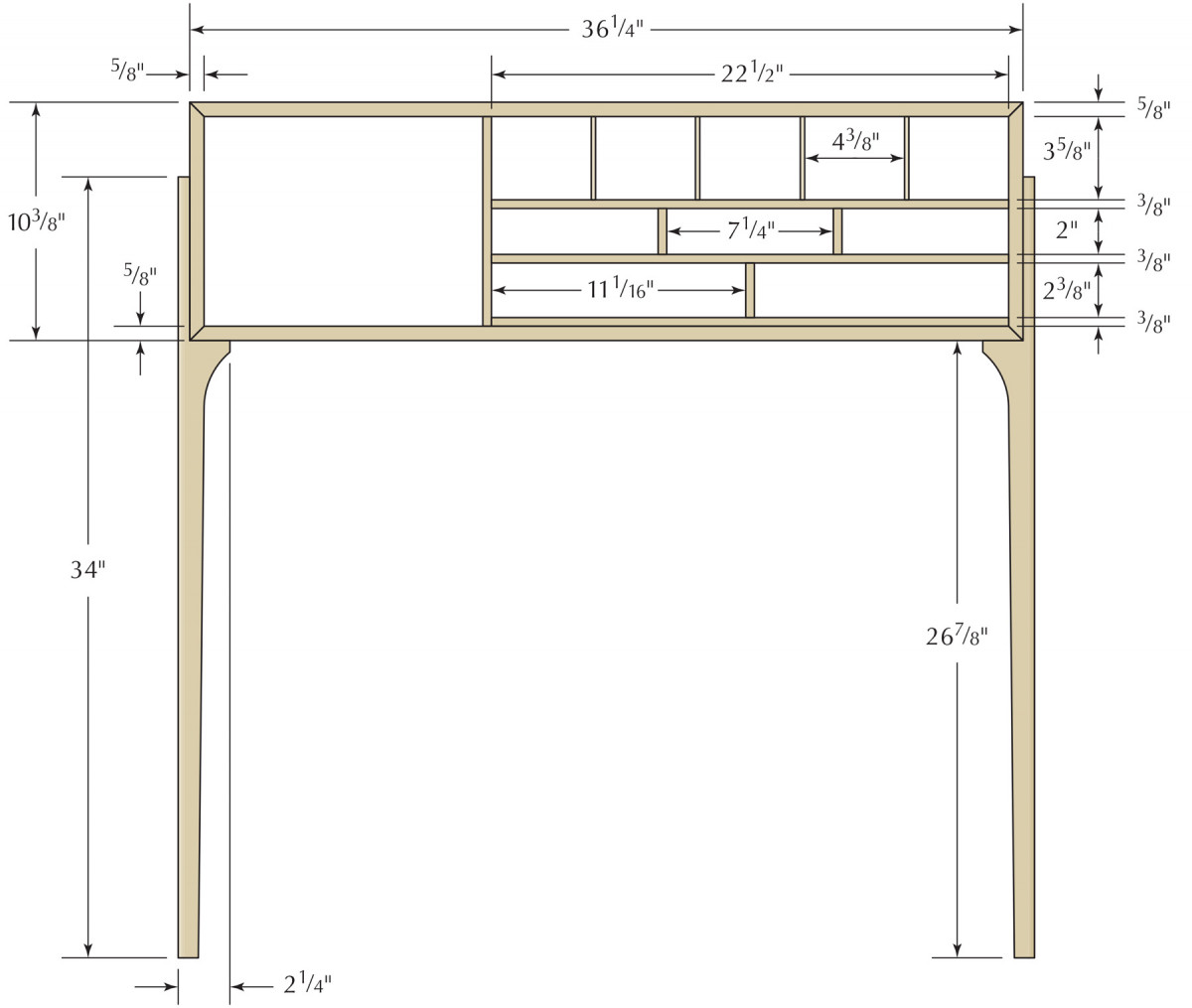
Elevation (back & drawers removed)
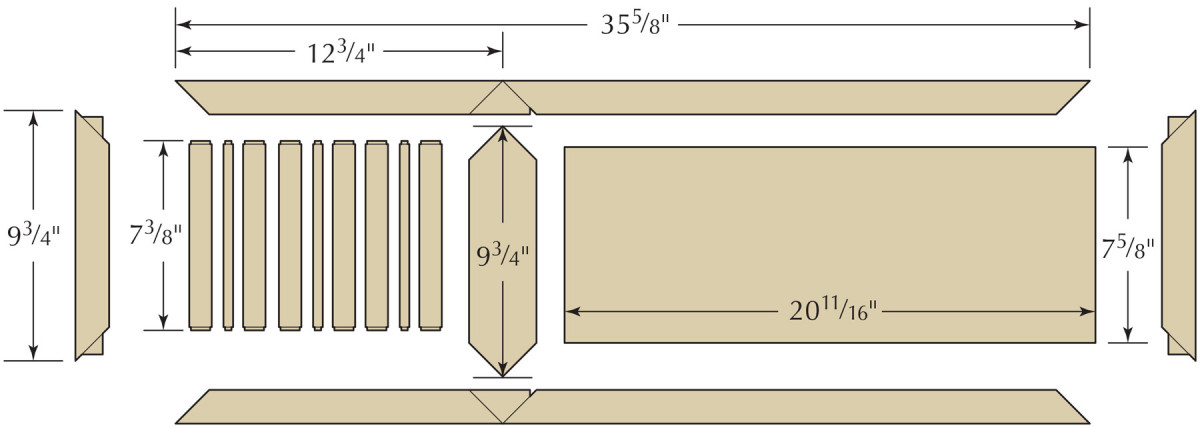
Back – exploded view
Unusual Legs
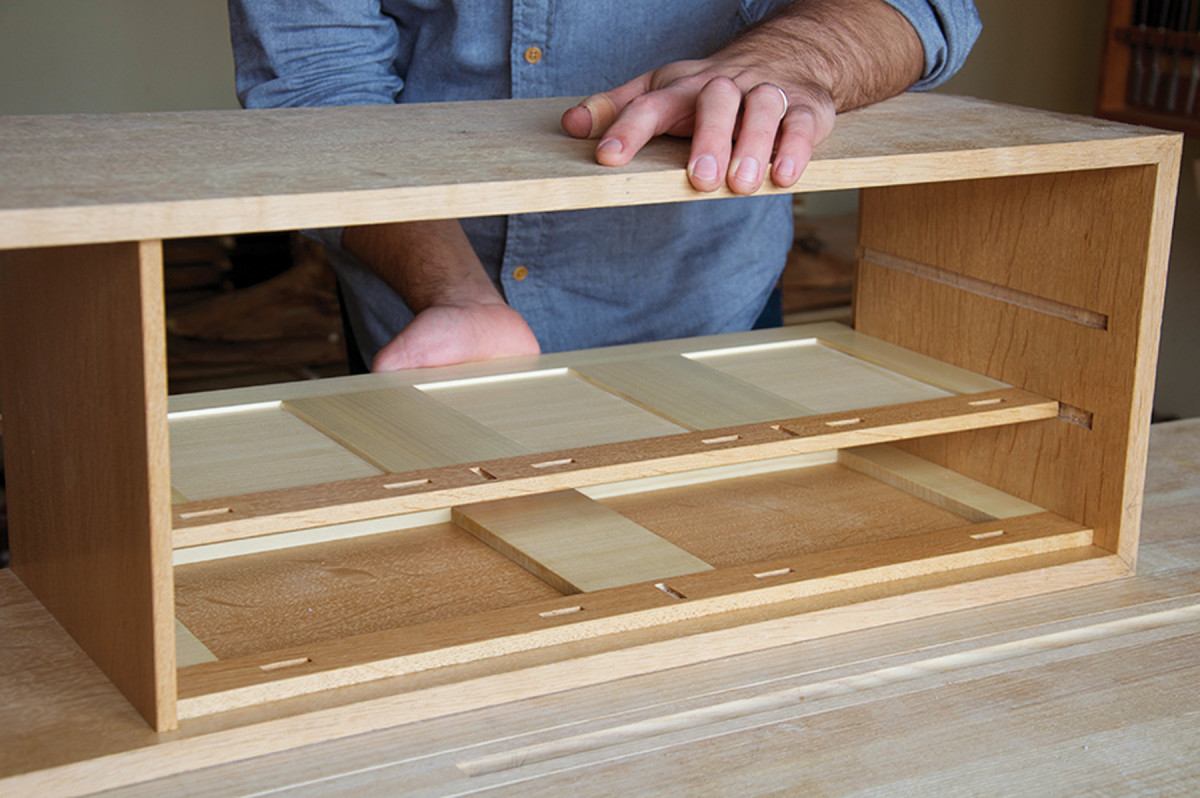
Push to assemble. The drawer frame and cup shelf slide in from the back. A dab of glue at the front of the dados will keep them in place.
Rather than a complex network of legs, rails and stretchers, the sideboard stands on four independently joined legs. They’re made sturdy by means of an unusual two-part joint that is surprisingly easy to cut.
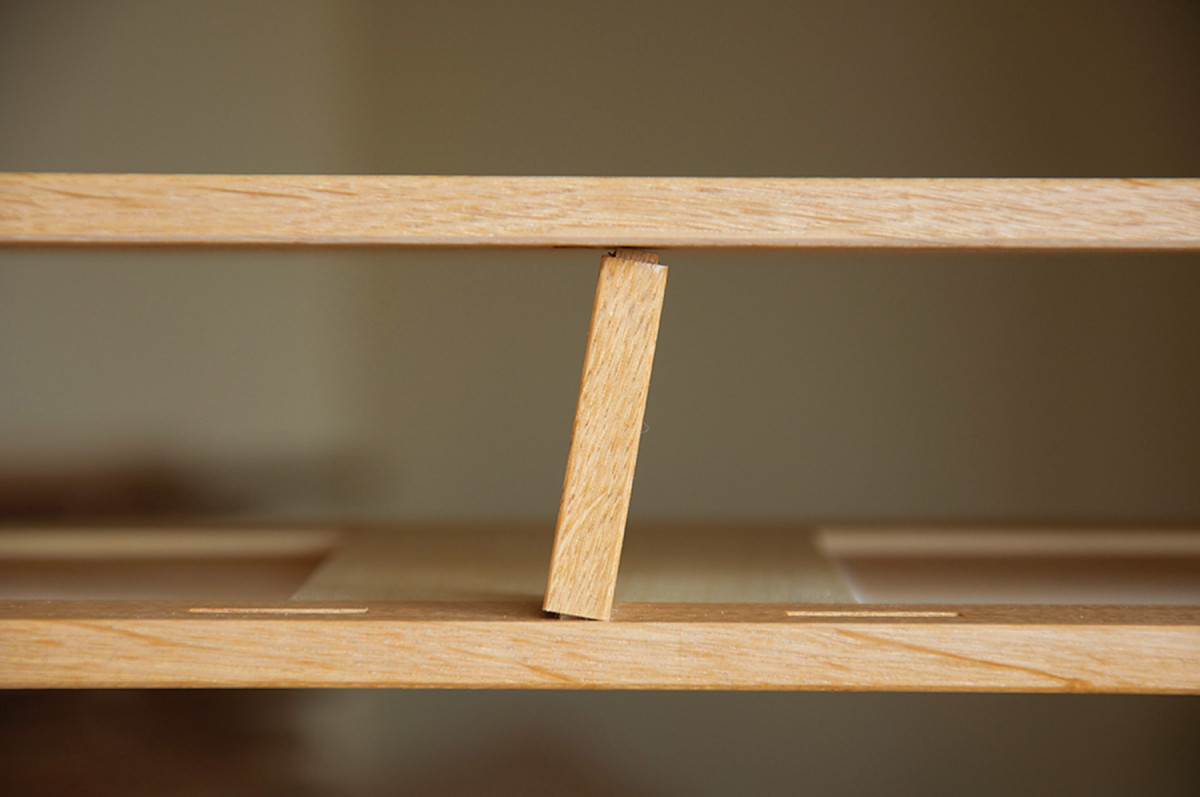
Wood is flexible. Gently bend the thin frame and shelf to install the vertical drawer dividers.
Start by milling four pieces of rift-sawn oak 11⁄8” thick x 21⁄4” wide x 34″ long. At the top of each leg, measure 13⁄4” from the inside edge to locate the long tenon’s shoulder and 17⁄16” to mark its depth. From the bottom of the leg, measure up 267⁄8“. This line will be the joint’s visible shoulder underneath the cabinet. Measure up 5⁄16” from the previous mark; this is the top of the dovetail.
Cut the resulting 17⁄16” x 71⁄8” notch with a saw, then pare the sawn faces back to the scribed lines, making sure they’re square to your reference face.
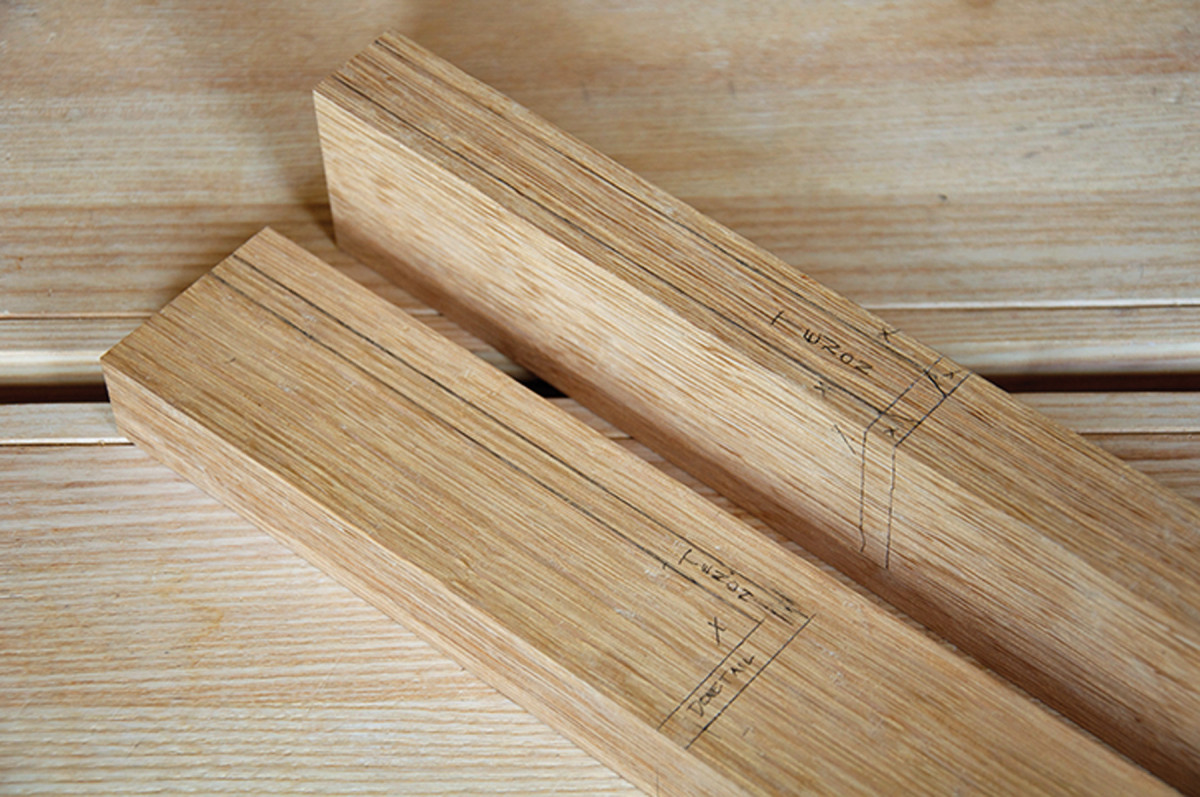
Leg layout. The aim is to create an L-shaped notch in which the cabinet will rest. A long tenon and sliding dovetail will keep it in place.
Next, create an L-shaped tenon by removing wood from each wide face. Set a marking gauge to 1⁄4” and scribe around the inside edge of the notch. Remove waste along the base of the joint by placing a chisel just inside the scribed shoulder line, chopping then paring toward the line at an angle. Continue until you’re just barely above the gauged line. Cut the vertical half of the joint by chopping along its length and paring from the side. Again, work to just above the gauge line, and finish off the tenon cheeks with a router plane.
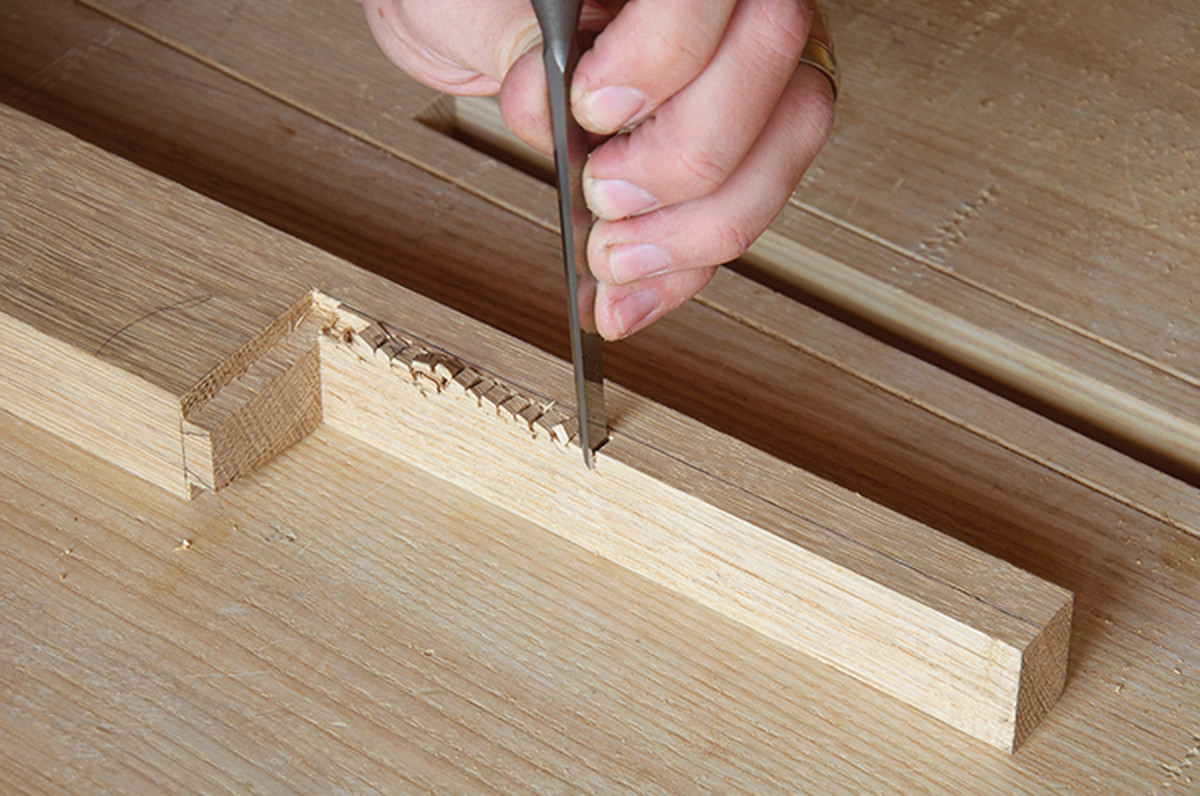
One-walled mortise. To form the long tenon in each leg, chop inside the shoulder line and pare from the side to remove the waste.
Mark the dovetail in pencil by measuring in 1⁄8” at the shoulder line of the joint and connecting these points to the upper corners of the tenon. Alternately chop and pare with a chisel until you approach the pencil line and shoulders. Square the shoulders to the base of the dovetails. Using a paring block that has been planed to the angle of the dovetail and to the appropriate height above your bench, guide the chisel in making gentle paring slices until it bottoms out. Finally, saw 1⁄4” off both the face of the dovetail and the top of the tenon to create clean shoulders.
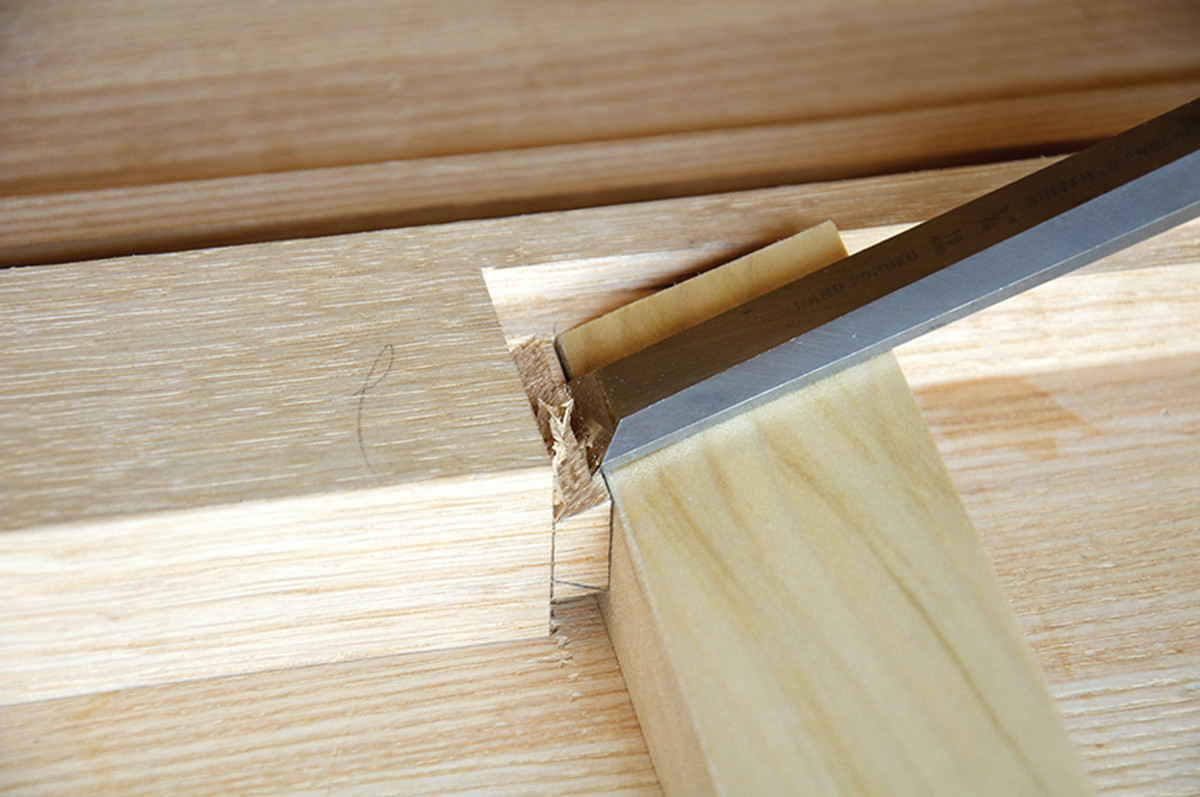
Pared with poplar. Guide your chisel with a paring block to perfectly form each leg’s dovetail.
Cut the other half of the joint directly into the bottom and sides of the main case. Because the leg slides into the case horizontally, the dovetail must enter its socket before the tenon engages its mortise. For this reason, I mark and cut the dovetail half of the joint first, and then, with the leg seated against the case side, scribe the final position of the long mortise.
To begin, hold the leg in position 1⁄2” back from the front edge of the case with the face of the dovetail pressing against the side of the cabinet. Trace around the dovetail, then transfer the location of its base to the bottom of the cabinet using a knife and square. Extend the marks 11⁄2” before squaring between them.
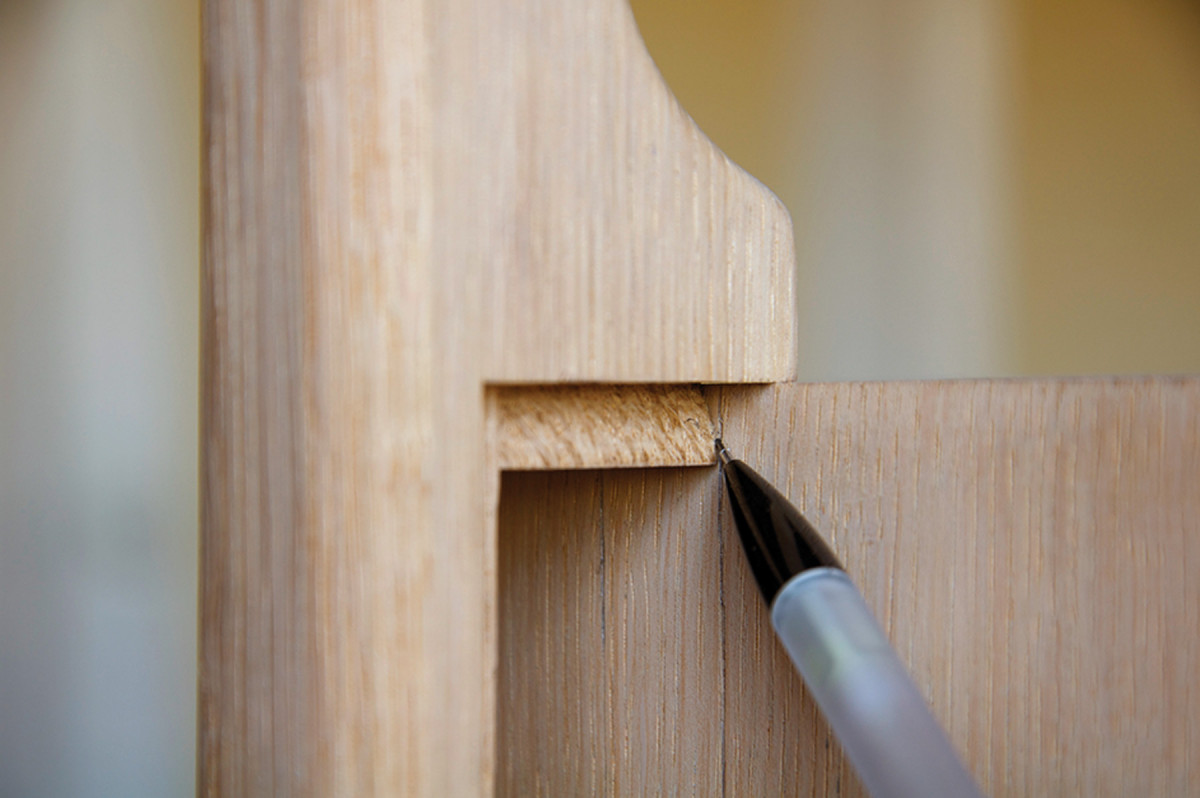
Trace the tails. Locate the position of the leg joinery by holding each one against the side of the cabinet and penciling in its silhouette.
If you cut the dovetail socket before the long mortise, you risk breaking off its cantilevered edges when enlarging the opening at the corner of the joint. Instead, first cut a 5⁄16” x 5⁄16” notch at the corner of the cabinet. Pencil in dovetail lines from the bottom corners of the notch to the knife lines on the bottom of the cabinet. Saw close to the pencil lines, then chop out most of the waste with a narrow chisel. To finish the sidewalls of the socket, carefully line up the same paring block used earlier with the scribed lines in the cabinet and clamp it in place. With a slicing motion, make successive passes until the wall is flat and straight. Clean up the bottom of the socket with a paring chisel.
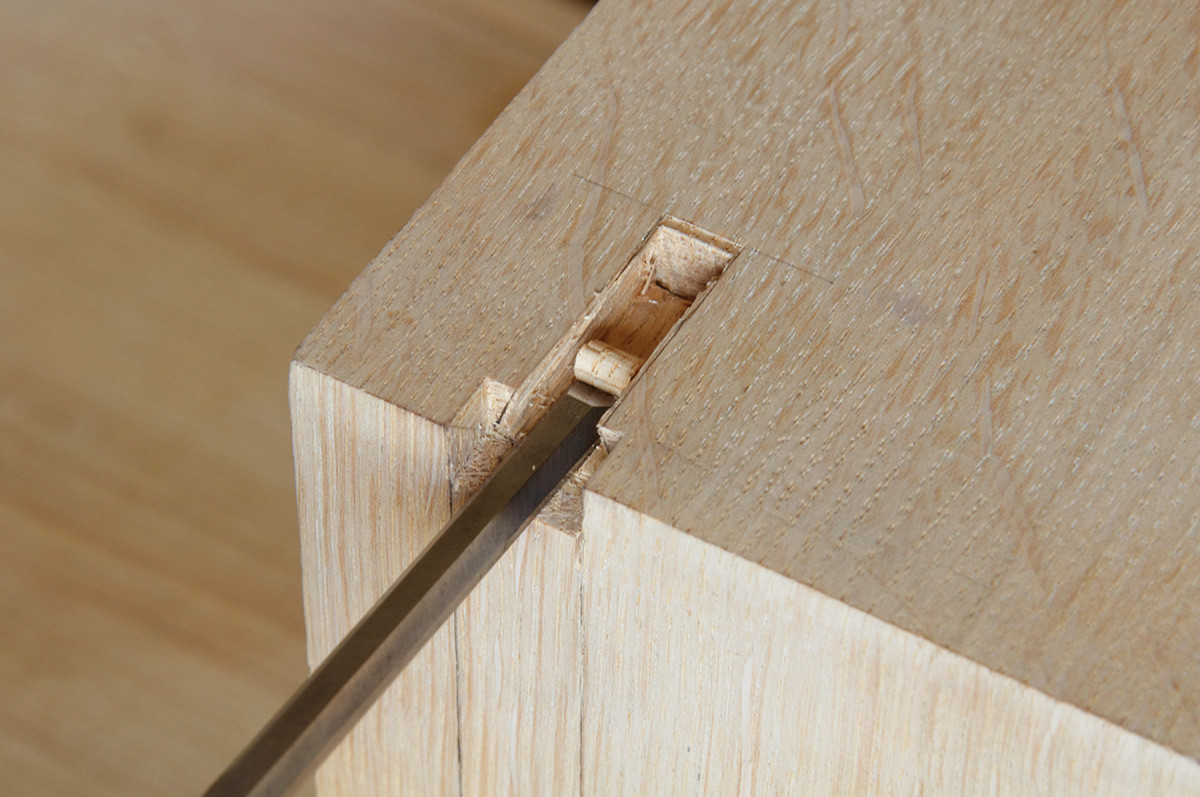
Chiseled sockets. Dovetail sockets in the cabinet are cut with chops from above followed by paring from the ends.
Dry-fit the dovetail and scribe around the tenon to determine the exact position of the mortise. Chop from one end to the other and clear out the waste. Having one end of the joint open makes this much easier; you can both lever out chips and pare from the open end.
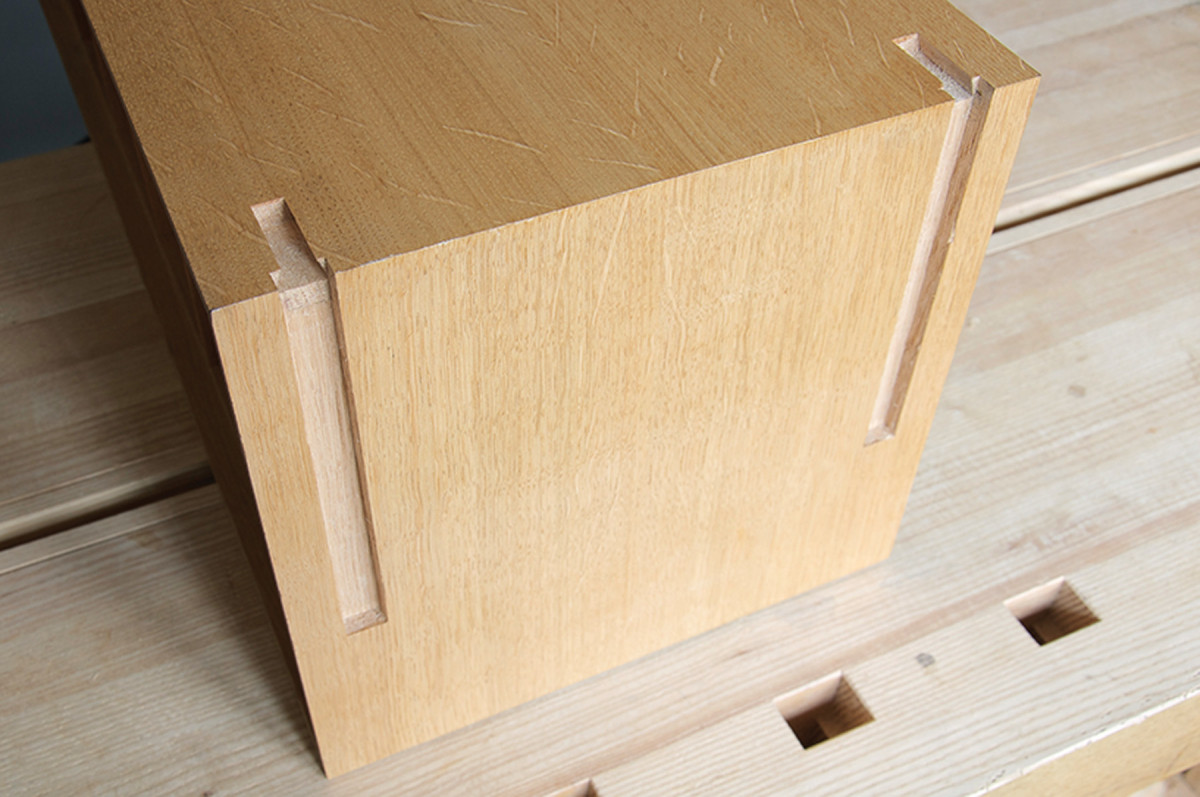
A receptive cabinet. Long mortises in the cabinet side receive the legs’ tenons, while sockets admit the dovetails.
Make one final pass with a router plane to provide an even gluing surface for the tenon.
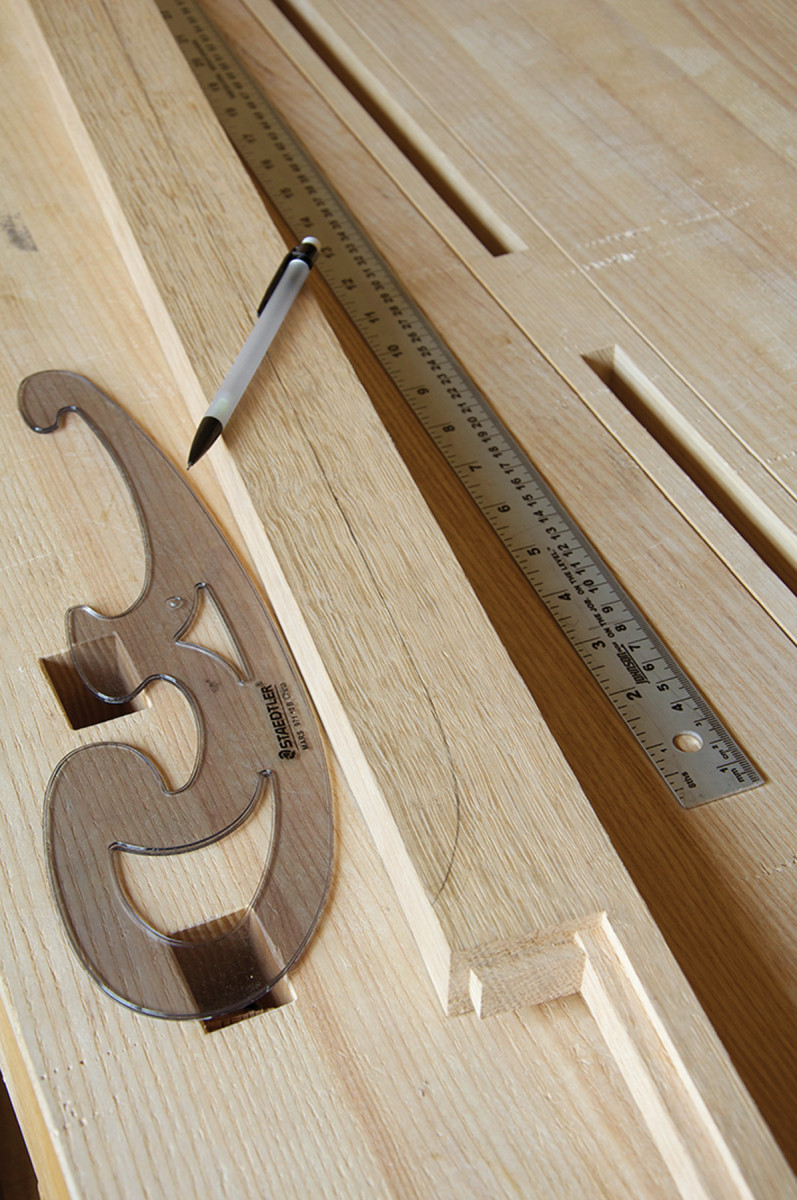
Trust your eye. Use a long straightedge and a French curve to draw a pleasing outline on each leg.
With the joints cut and fit, shape the legs. As seen from the front and measured from the outside edge, each leg tapers from 1 1⁄8” at a height of 24″ to 7⁄8” at the floor. Mark this taper in pencil, then use a French curve to connect the top of the tapered portion with a point on the inside edge 1⁄2” down from the dovetail’s shoulder.

Downhill slide. After most of the waste is sawn away, smooth the inside face of each leg with a small, curved-bottom spokeshave.
Saw out the waste and smooth the resulting inside face with a spokeshave and block plane. The front and back of each leg are also tapered from 1 1⁄8” thick at their tops to 7⁄8” at the floor. Mark these tapers in pencil and work carefully down to the lines with a long plane.
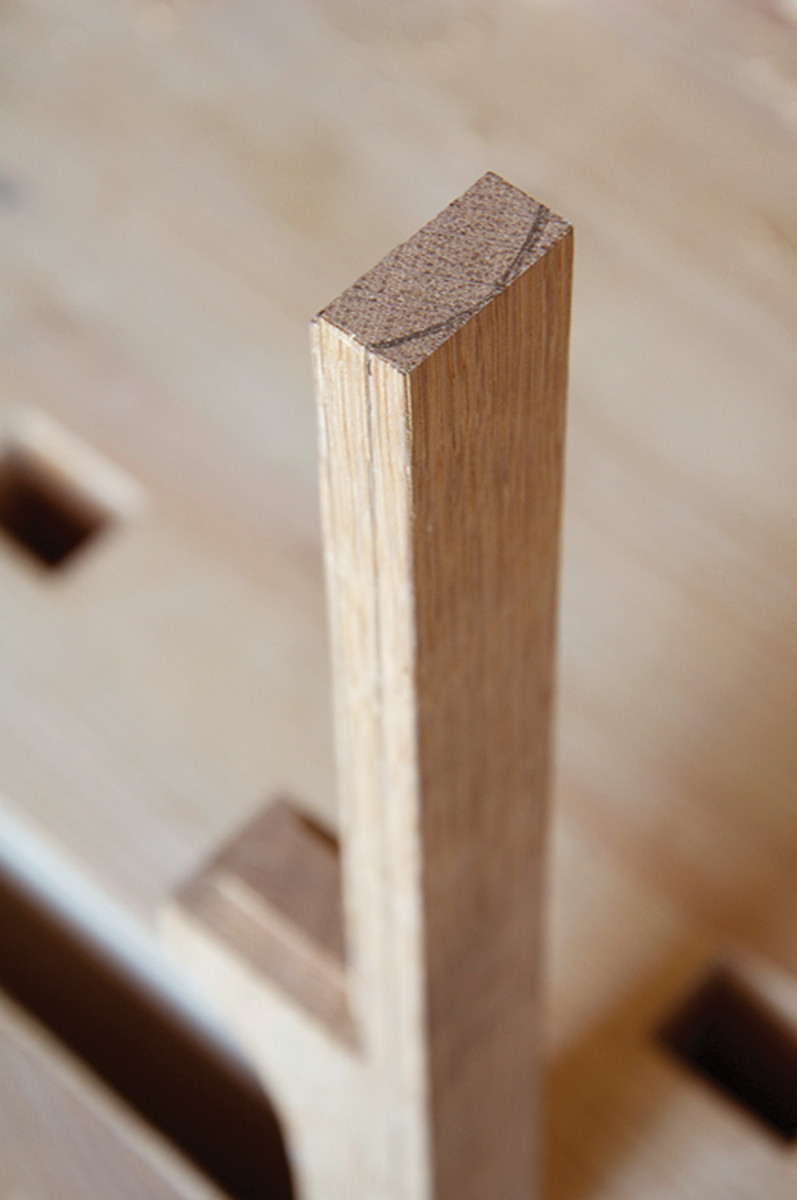
Outer bulge. Sketch a soft curve on the end of each leg, then work down to the lines with a jack plane.
Finally, use a plane to round over the outside corners, leaving a bulge in the center of the leg’s length. Soften the edges of the inside corners as well, but leave the inside face flat.
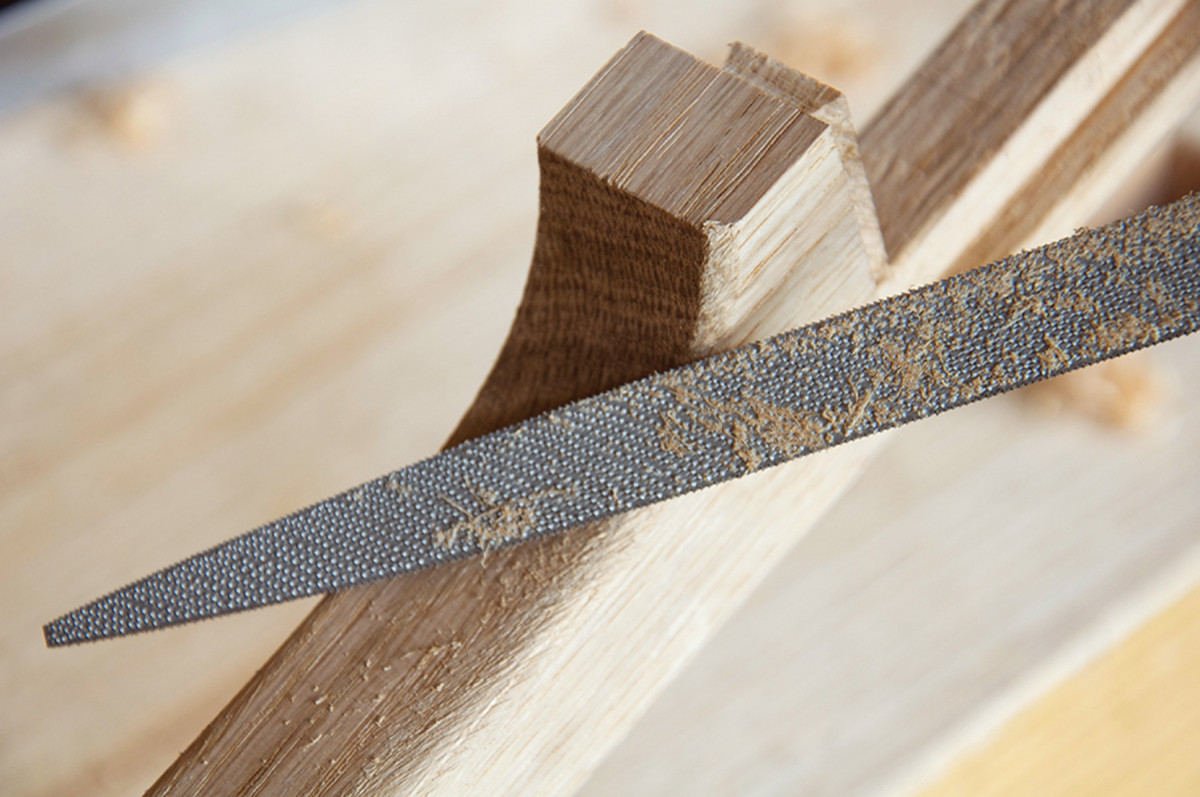
Rasp to round. Starting at the top of the curve, round over the inner, curved edges of each leg with a fine rasp.
To simplify assembly, glue and clamp one leg at a time. When the glue in the leg joints has cured, flip the whole thing over and test for level on a flat surface. Make any necessary adjustments, then chamfer the bottom edges.
Many-mitered Back
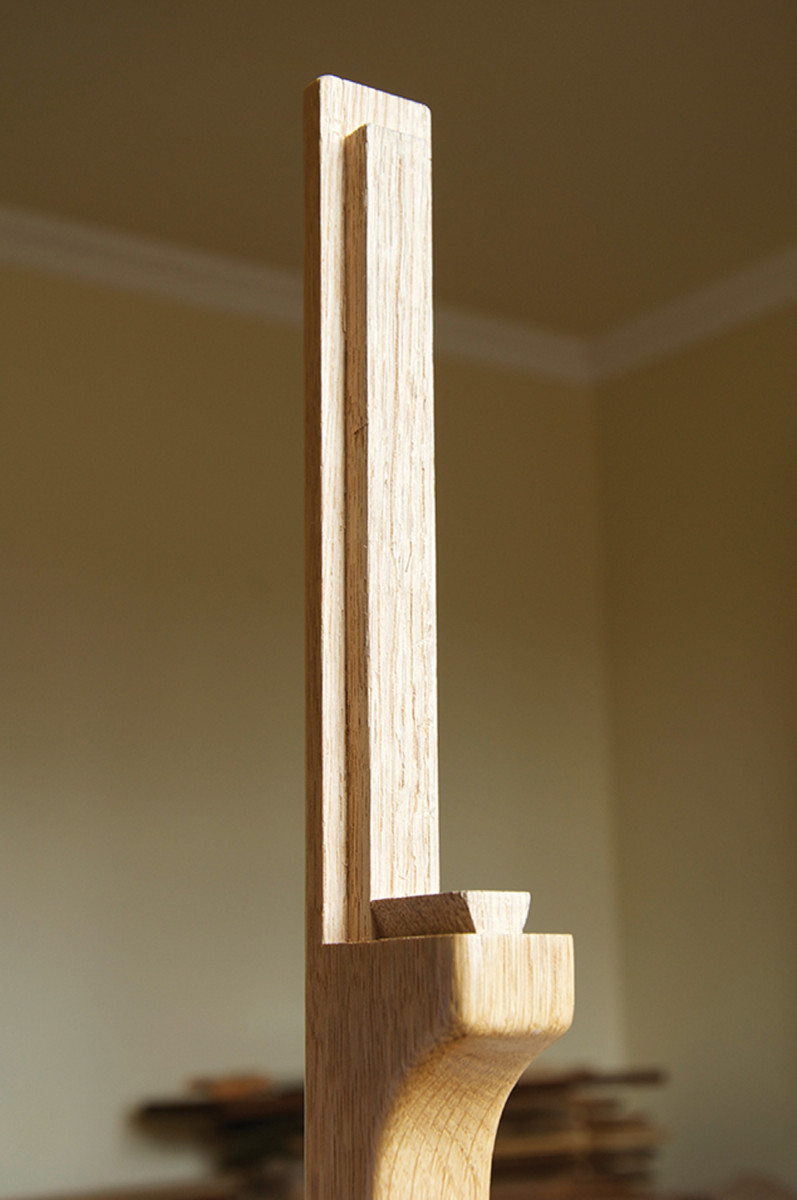
Tenon & tail. Each finished leg joint is composed of a long vertical tenon and a short sliding dovetail.
The back mirrors the interior of the cabinet; an outer frame is divided into two sections by a central stile, with slats behind the teapot cubby and a solid panel behind the drawers. The rails and stiles are mitered both inside and out, continuing the theme of clean, hidden joinery and making the back the most complex part of the project.
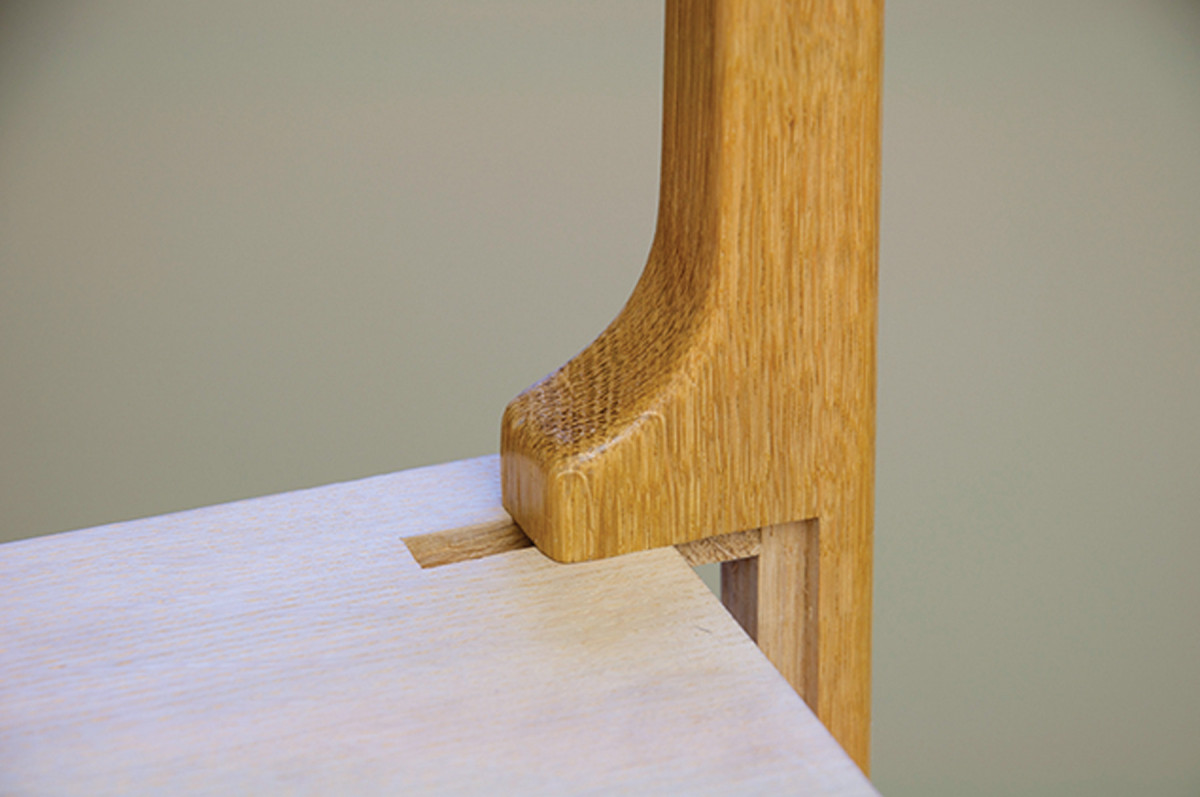
Enter leg. Each leg slides laterally into the main case, dovetail first.
Make the outer frame from 1⁄2” stock ripped to 1 5⁄16” wide. Mark the length of one rail and one stile directly from the rabbet in the back of the cabinet, adding just a whisper to each. Transfer those lengths to the other two pieces. Using a knife and an adjustable square, scribe the miter angle onto both faces of the pieces and square across the edges. Ensure that the bevel of your knife falls on the waste side to prevent damaging the edge of the miter.
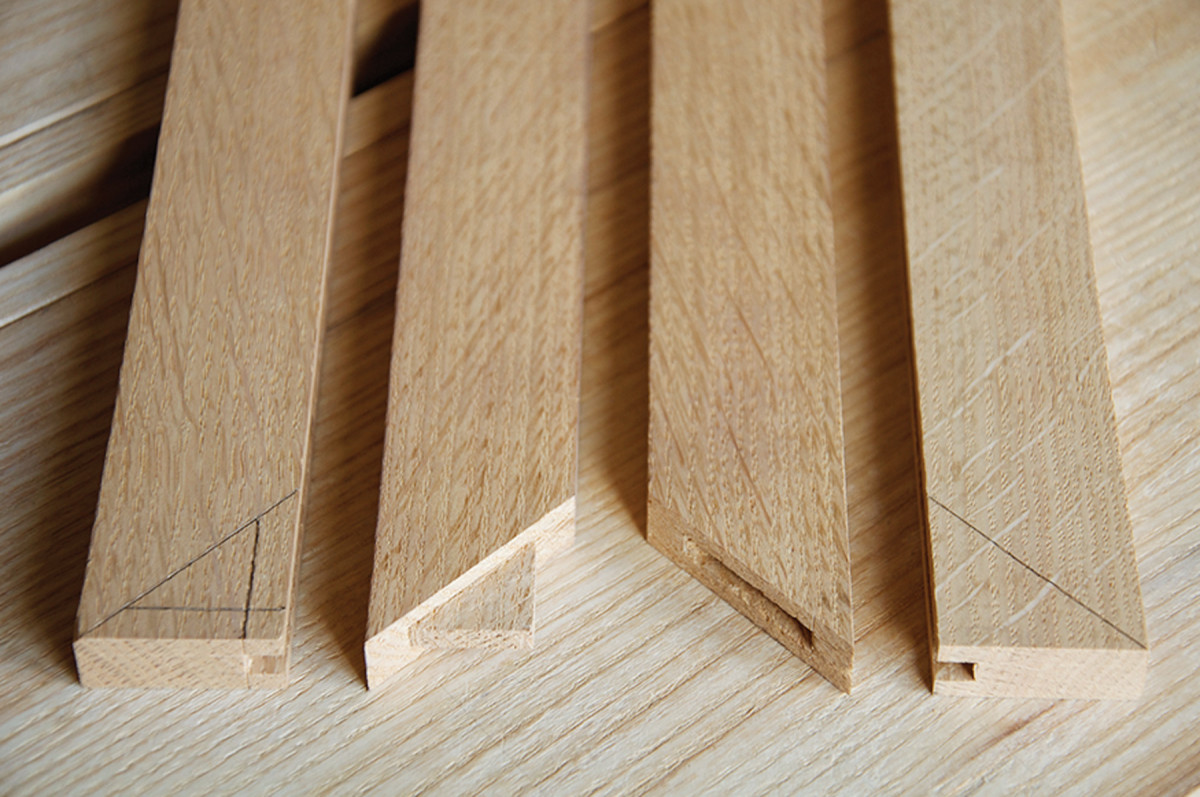
More than meets the eye. Within the back’s mitered stiles and rails lie hidden tenons and mortises.
Stub tenons project from the mitered ends of the stiles but stop short of passing through the rails. To achieve this, cut the stiles to their exact finished length, then use a mortise gauge to scribe the thickness of the tenons. The settings on the gauge should match both the 3⁄16” width of your plow plane blade and its distance from the fence when centered on the stile. Use another marking gauge set to 1⁄4” to scribe the length of the tenon (using the end of the stile as a reference) and then to mark its width (using the inside and outside edges). Saw the waste, being careful not to spoil the cleanly marked baseline. Finish by paring the shoulders square.
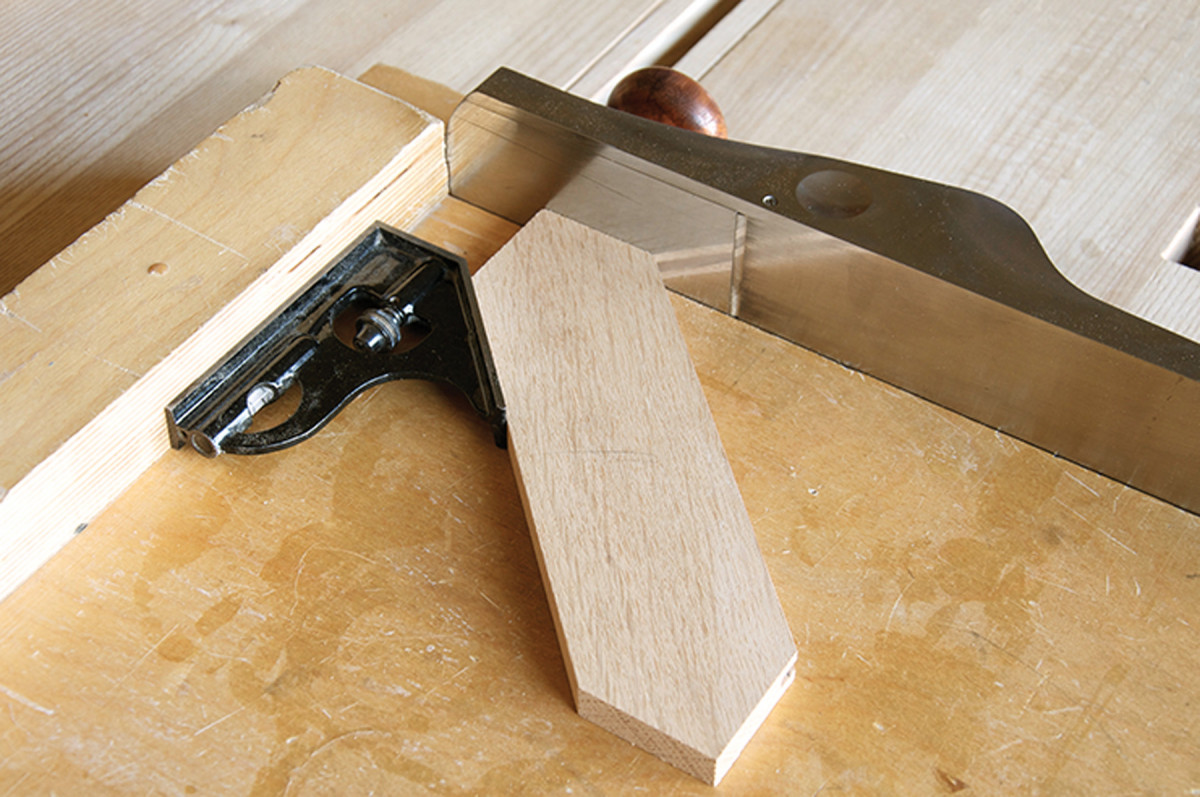
Fence, improvised. The head of an adjustable square makes a suitable temporary fence for shooting miters.
The tenons slip into mortises cut into the mitered ends of the rails. Shoot the rails to their finished length using an angled fence or adjustable square. Use the same mortise gauge to mark the mortise widths on the mitered ends. Mark the mortise lengths by squaring across the mitered ends from measurements made on the reference faces. Then simply stand the rails on edge and make alternate chops of the chisel with paring strokes to remove the waste.
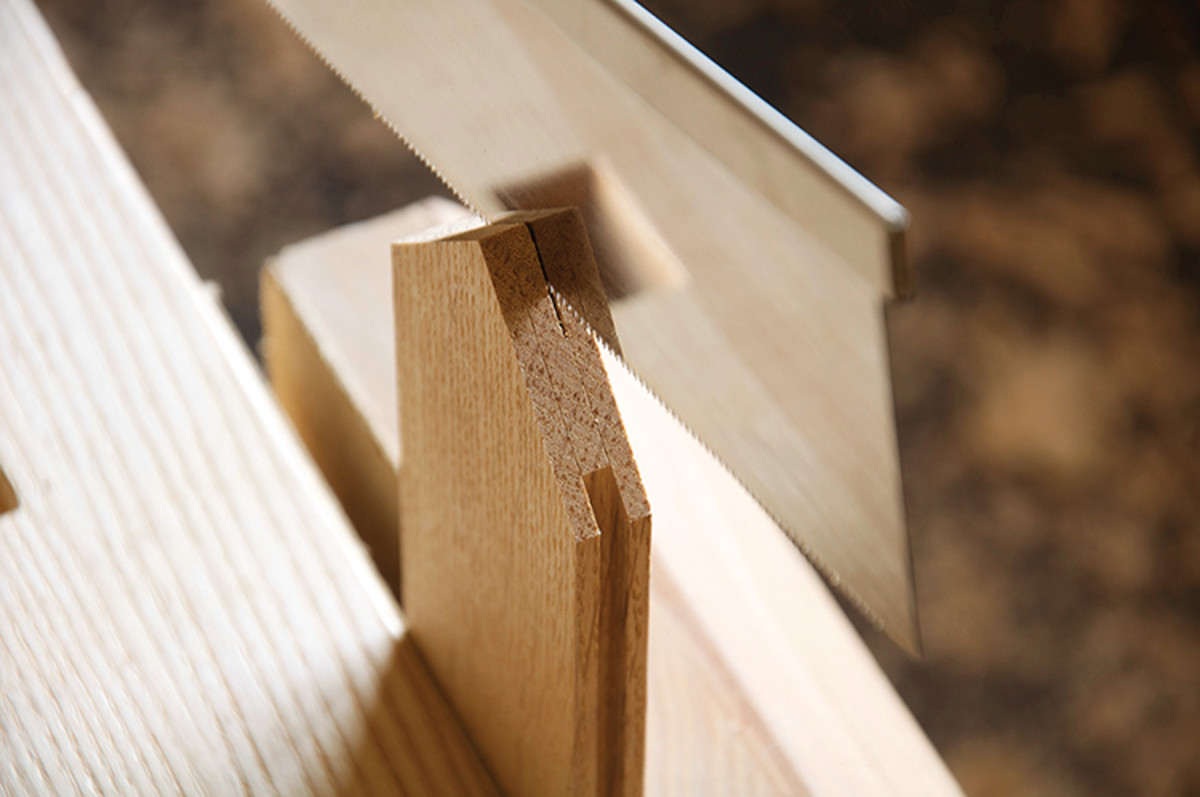
A pointed endeavor. Begin the back’s trickiest joint by sawing out the middle 3⁄16″ of the central stile’s pointy ends.
The wide central stile is joined to the frame by means of a double-mitered bridle joint. For the miters to be even, the stile must be 2 5⁄8” wide – exactly twice the width of the rails – and the same length as the other two stiles. Find the center at each end and scribe the miters from those points. Saw the waste then finish the miters on a shooting board. Now use the mortise gauge to scribe the pointed ends then make vertical saw cuts down to the baselines. Remove the waste in the middle with a coping saw and paring chisel.
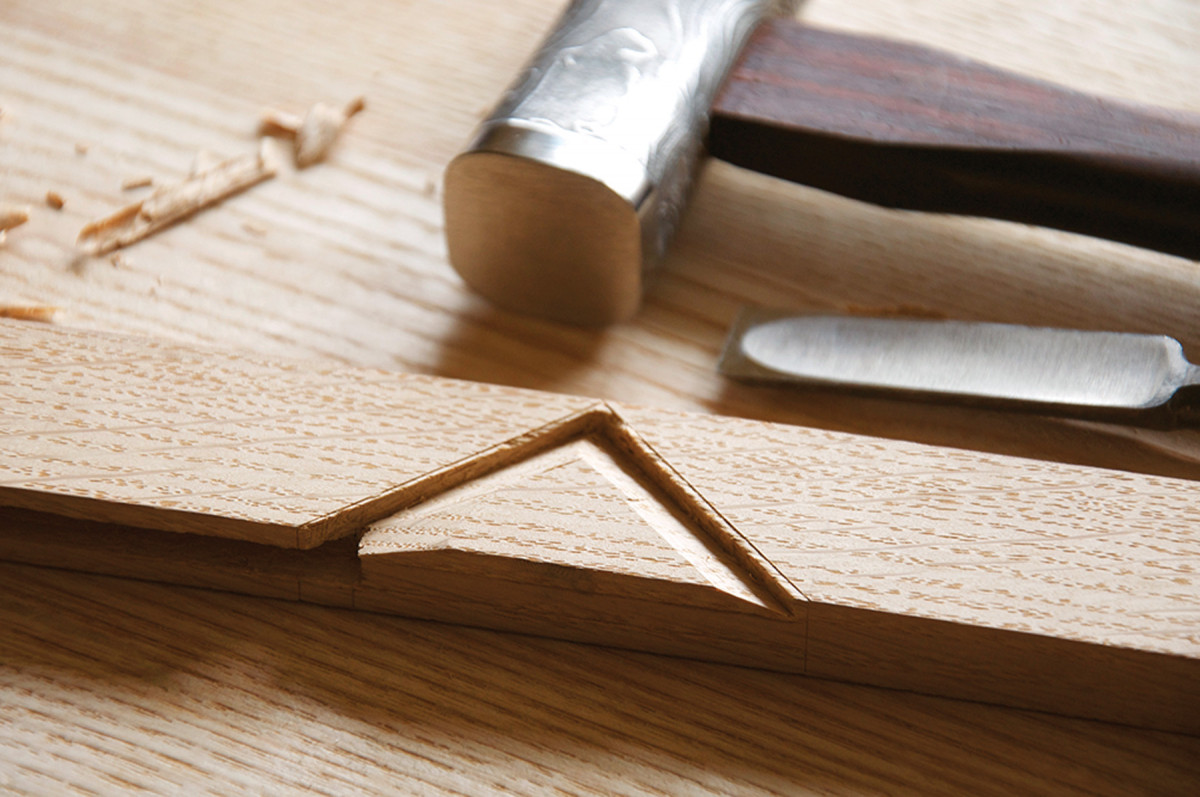
Clear the decks. After marking the long rails with converging miters, chop and pare a notch close to your layout lines.
Plow 1⁄4” deep grooves in the central and right-hand stiles. The grooves in the long rails stop at the central stile, so cutting them involves an extra step. First, use a plow plane to cut as deep as possible without overcutting the stopped end. Then, with a narrow chisel, mortise out enough material at the end of the groove to allow the front or back half of the plow plane to sink fully into the groove. Continue plowing until you reach full depth.
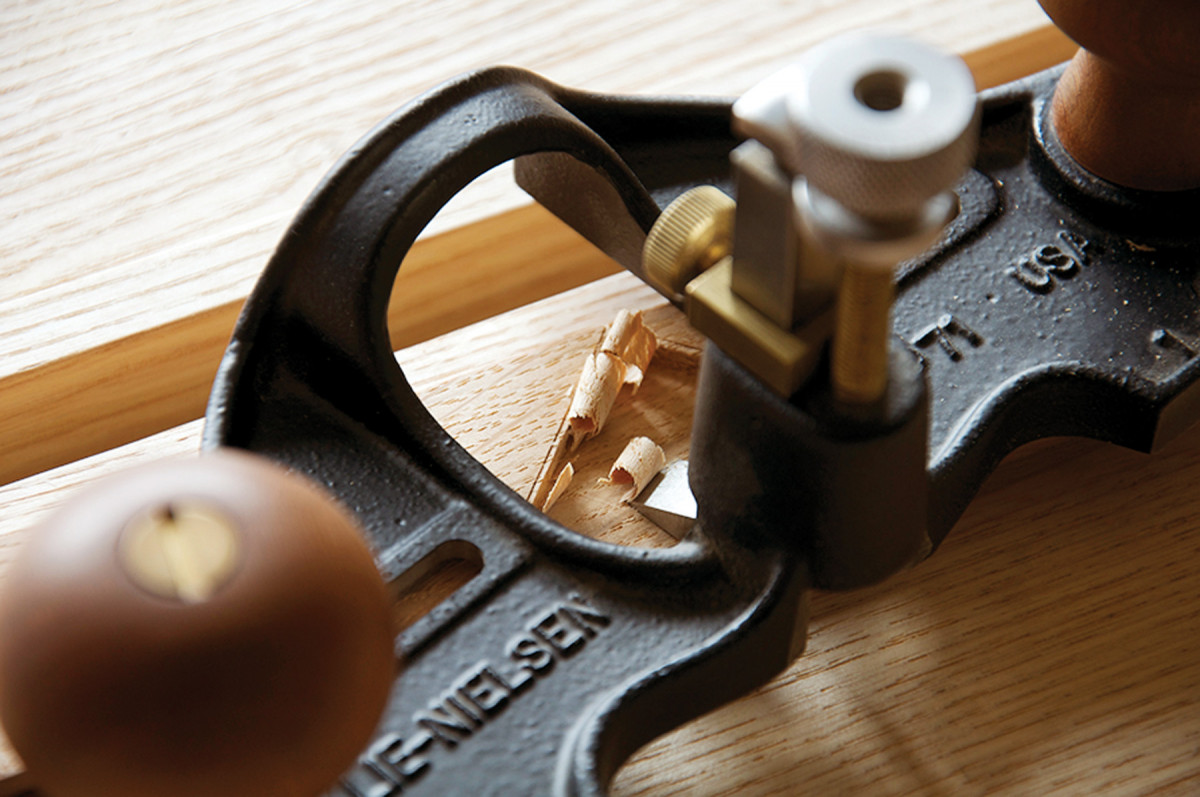
Scraping bottom. A router plane leaves a smooth, consistent surface for the mouth of the bridle joint to close on.
Next, cut the second half of the double-mitered bridle joint. Mark the apex of the miters 12 3⁄4” from the left end of the rails. Scribe the miters from those points and use the mortise gauge to mark along the inside edge of each rail. Chop and pare the waste until you’re just above the scribe lines. A final pass with a router plane yields a smooth, consistent surface. Test the joint to make sure all eight miters close tightly.
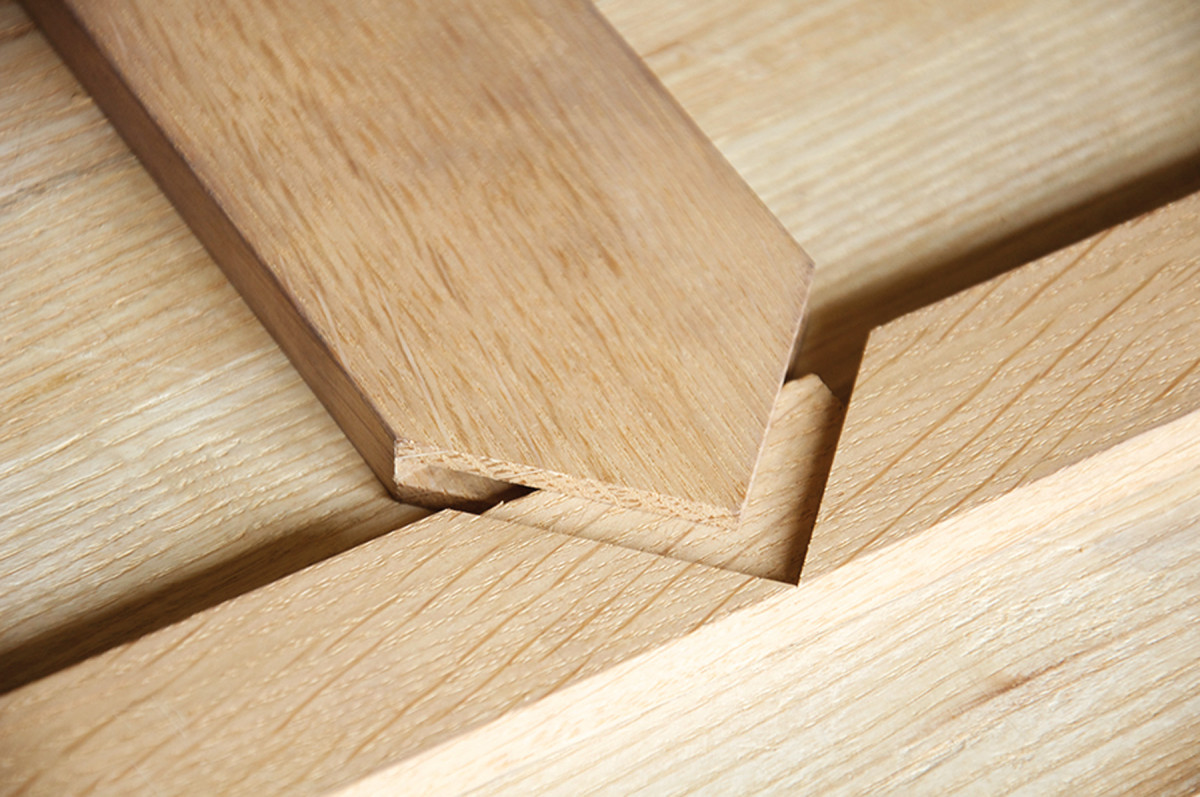
Miter sandwich. The central stile’s two outer points slip over the interior portion of an outer rail.
Apply shellac to the panel, slats and inside edges of the rails and stiles in preparation for gluing. Once the glue has cured and the clamps are off, smooth the faces of the assembled back. It will likely be too large to slip into its recess. Take a few light shavings off each edge, test the fit and continue until it eases in. Work each side evenly so the miters remain aligned. When the back fits, put a thin bead of glue along the top and bottom and press it into place.
Drawer Construction
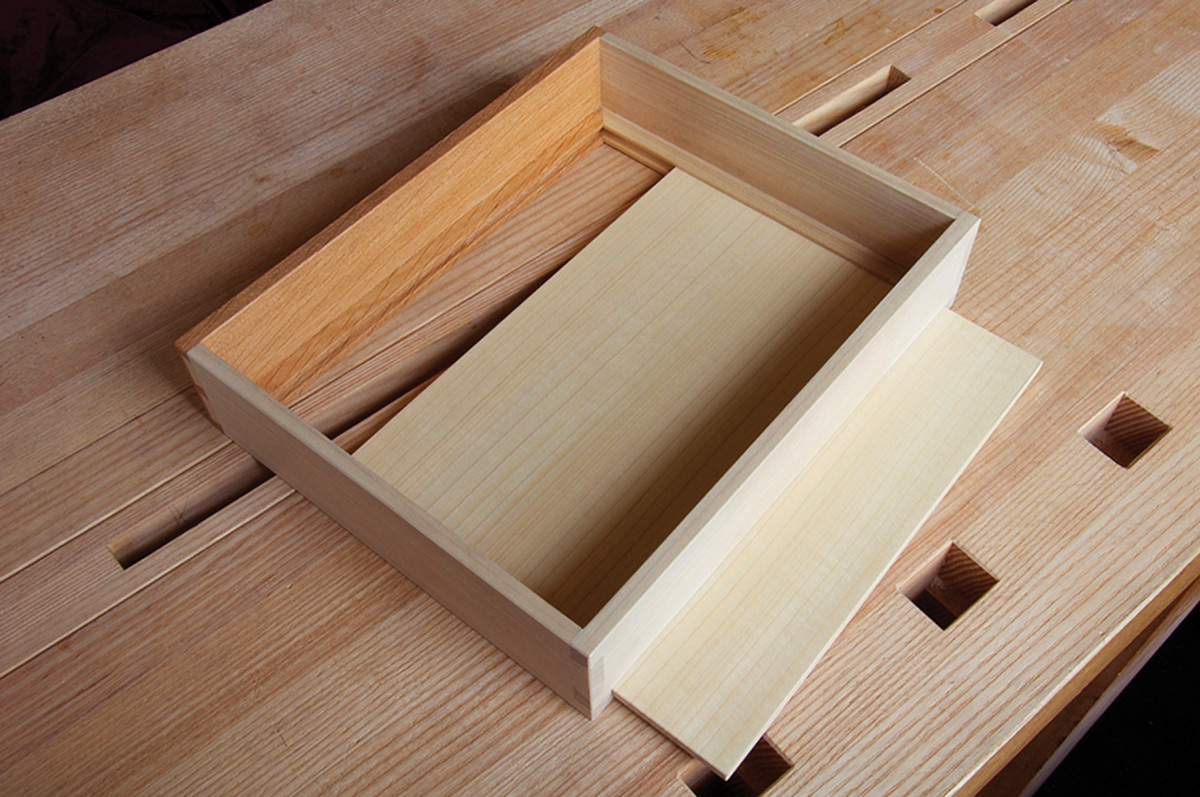
Slips. Instead of a groove plowed in the thin sides and the front of these delicate drawers, mitered slips are used to support the bottoms.
The five drawers are constructed with half-blind dovetails at the front and through dovetails at the back. But instead of a groove in the drawer sides and front to capture the bottoms, I used mitered “slips.” The drawer sides are a slender 5⁄16“; were I to plow grooves sufficient to support the bottoms in such thin stock, the sides would be significantly weakened. Slips, on the other hand, allow for both attractively thin sides and properly supported bottoms.
To make the slips, plane a small board to the appropriate thickness and square one edge. Plow a 1⁄4” groove 3⁄16” from the reference edge, then use a marking gauge to scribe the slip’s 5⁄8” height. Saw close to the scribed line and finish the edge with a block plane.
Miter both ends of the front slip and glue it to the drawer front. Miter the front end of each side slip and cut the back ends flush with the rear of the drawer. Turn the drawer upside down and mark where the side slips meet the inside face of the drawer’s back. Saw a 3⁄16“-deep notch in the top of each slip, stopping at the mark. This notch allows the slip to fit between the drawer’s front and back and aligns the top of the groove with the bottom of the drawer’s back.
Profile the top of the slips to your taste; I opted for a simple bevel made with a block plane. Glue the side slips in place, and fit the drawer bottoms as usual.
Savoring the Finish
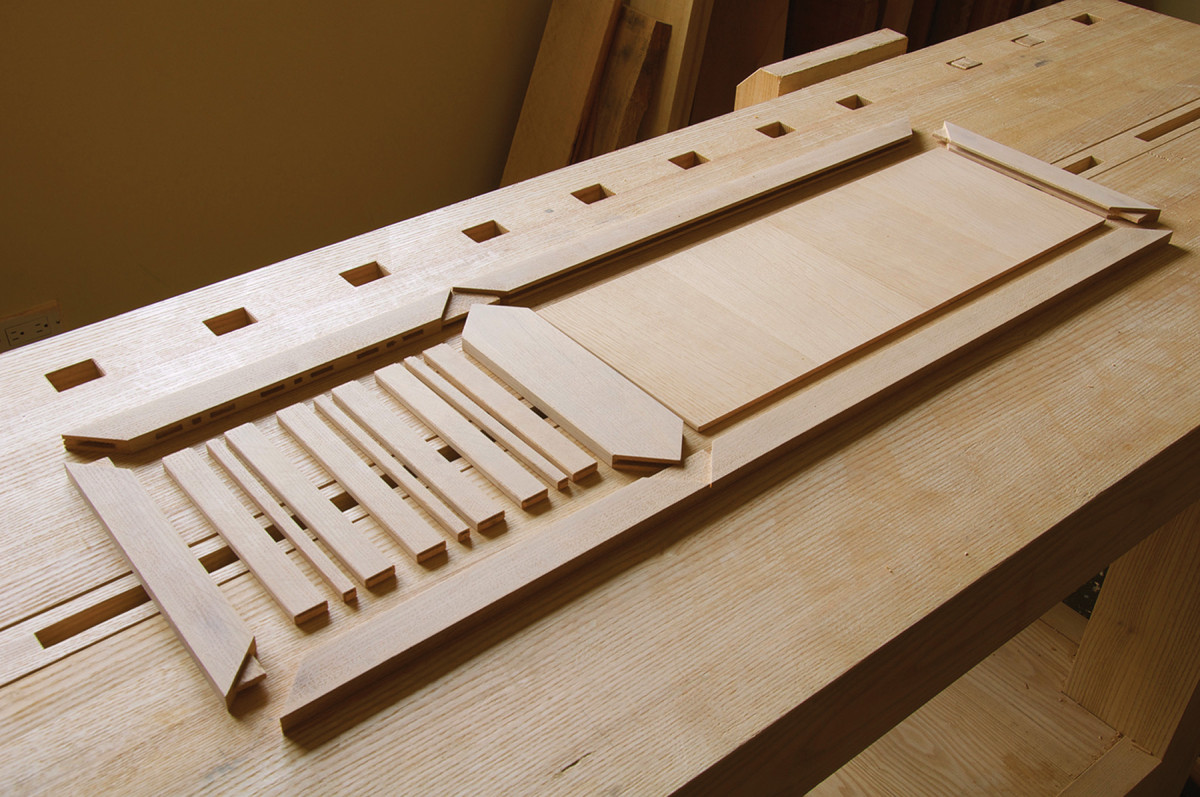
Fifteen pieces. The back has many parts and many angles. For sanity during clamping, use liquid hide glue or another slow-setting adhesive.
Apply finish to the cabinet’s components as they are assembled, ending with the exterior top and sides. For all surfaces, I opted for a few thin coats of shellac applied with a pad, followed by a round of buffing with wax and fine steel wool.
When you’re done polishing, grab a mug and reflect on how a cup of tea may speak of more than sun and earth. Was it prepared thoughtfully or carelessly? Is it savored for its subtleties or unthinkingly consumed at once? Like a finished cabinet and the effort we put into making it, tea is evidence that how we go about our work has as much to do with the character of our creations as the stuff they are made of. If we approach our materials with awe and apply ourselves to laboring with finesse, our lives, like our cabinets, will be richer for it.
Free model: Download a free SketchUp model of this project
Here are some supplies and tools we find essential in our everyday work around the shop. We may receive a commission from sales referred by our links; however, we have carefully selected these products for their usefulness and quality.