We may receive a commission when you use our affiliate links. However, this does not impact our recommendations.
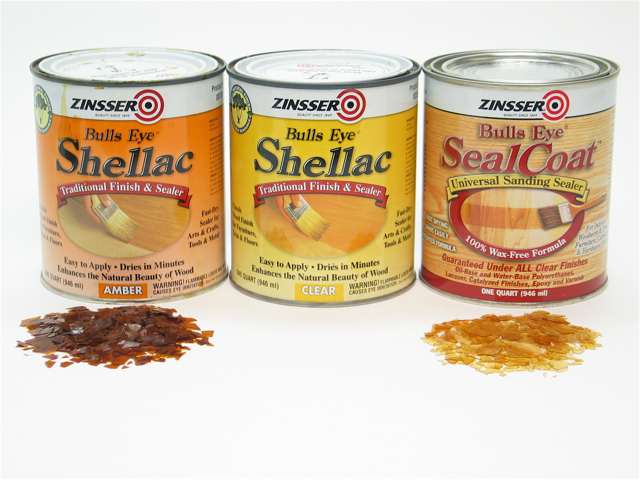
Zinsser also changed the name of its “orange” shellac to “amber” shellac (who wants orange wood?) and its “white” shellac to “clear” shellac.
Here’s a short history of shellac, some of it from my own experience.
Shellac was almost the only finish used on furniture from the 1820s to the 1920s when nitrocellulose lacquer was introduced. Shellac continued to be used widely as a complete finish by painters working in buildings until the 1950s.
By the 1990s the only remaining supplier of shellac in liquid form was Zinsser, which sells the shellac under the brands “Bulls Eye” and “SealCoat,” which is a dewaxed variety. Zinsser specializes in sealers and primers, so it markets the shellac as a sealer.
The marketing strategy as I have experienced it centers on getting influential magazine and book writers to recommend shellac as a sealer. This has led to shellac becoming widely identified as a sealer rather than as a complete finish.
Too much so, in my opinion, because shellac still makes a great complete finish just like it used to, and because there’s no reason to use shellac as a sealer unless there’s a problem you need to seal off. The four common problems are:
· Silicone contamination in the wood from the use of certain furniture polishes. This contamination causes the finish to fish eye, which shows up as ridges, often in the shape of craters.
· Oil or wax on the wood. Shellac bonds better than other finishes to oily and waxy surfaces.
· Odors in the wood for example, from smoke damage or animal urine. Shellac blocks these fairly effectively.
· Resin in the wood, especially from pine and other softwood knots and in certain exotic woods that grow in jungles. Examples include teak, rosewood and cocobolo. Shellac also blocks this resin fairly effectively.
Notice that except for the last one, the problems are typically refinishing problems. Also notice that all the major writers on finishing are, or were at one time, professional refinishers. So shellac was a very useful tool for them (us).
But shellac is not necessary if these problems don’t exist. And this is the point of this short history. No furniture or cabinet manufacturer uses shellac as a sealer. Only woodworkers who read the magazines think they should always use shellac as the sealer.
– Bob Flexner
Here are some supplies and tools we find essential in our everyday work around the shop. We may receive a commission from sales referred by our links; however, we have carefully selected these products for their usefulness and quality.
I primarily use shellac then wax to finish my pieces. It’s easy to use and looks good.
To be honest, I like starting with shellac because it’s fast & easy but I too fell into the sealer myth.
Thanks for your blogs Bob. You always clearly demystify wood finishing. I use super blonde de-waxed shellac to warm up a water borne top coat. I believe you have recommended this in the past, do you still recommend this (vs tinting the top coat, or other process)?. I have read your 2005 book, and would love to hear your 2017-updated opinions on the best water borne finishes. Thanks again!
Bob, I agree there are other ways to washcoat wood than shellac. It is unfortunate that shellac is considered useful only as a sealer. I use shellac for various finishing processes and to make my own stains . I have been experimenting with button lac lately.
As you stated, the longer drying/cure of varnish based wash coat leads to user error. Maybe they suggest shellac because they think their readers are impatient?
Also, instructions on Rust-Oleum Ultimate stain state that no conditioner is needed. They claim use of nano pigments for more even coverage.
Bob, do you get blotching if you use dyes without a washcoat?
I have been experimenting with dyes. I get varying blotching results depending on whether I use oil, alcohol, or water based dyes. Alcohol based dye with a splash of shellac in the solution has given me the best results so far.
I like to use dewaxed shellac for “sealing” (if that’s the right word) the end grain of wood so that it doesn’t soak up more stain than the surfaces, and therefore look darker.
I would add this to your “odors” and “resin in the wood” reasons
I’ve always read that using shellac as a base coat is a good reducer of blotchiness in a finish as it pertains to pine, maple, birch and cherry. I didn’t see that mentioned in the article.