We may receive a commission when you use our affiliate links. However, this does not impact our recommendations.
Great-looking wood and bright-colored felt lining reel in my customers.
I’m hooked on making jewelry boxes–for sale. I’m retired, so I don’t live on the income, but making dozens of boxes keeps me in the shop, where I like to be.
I sell my boxes at local craft shows. Let me share with you four secrets to making a sale. First, I use wood with strong character–locally-grown, when possible. Second, I line all my boxes with felt. (This feature really appeals to the ladies). Third, my design is very simple, which keeps my prices low. These small jewelry boxes sell from $65 to $95, depending on the wood. Fourth, I always include a little story about the wood and where it came from.
Make the Sides and Lid
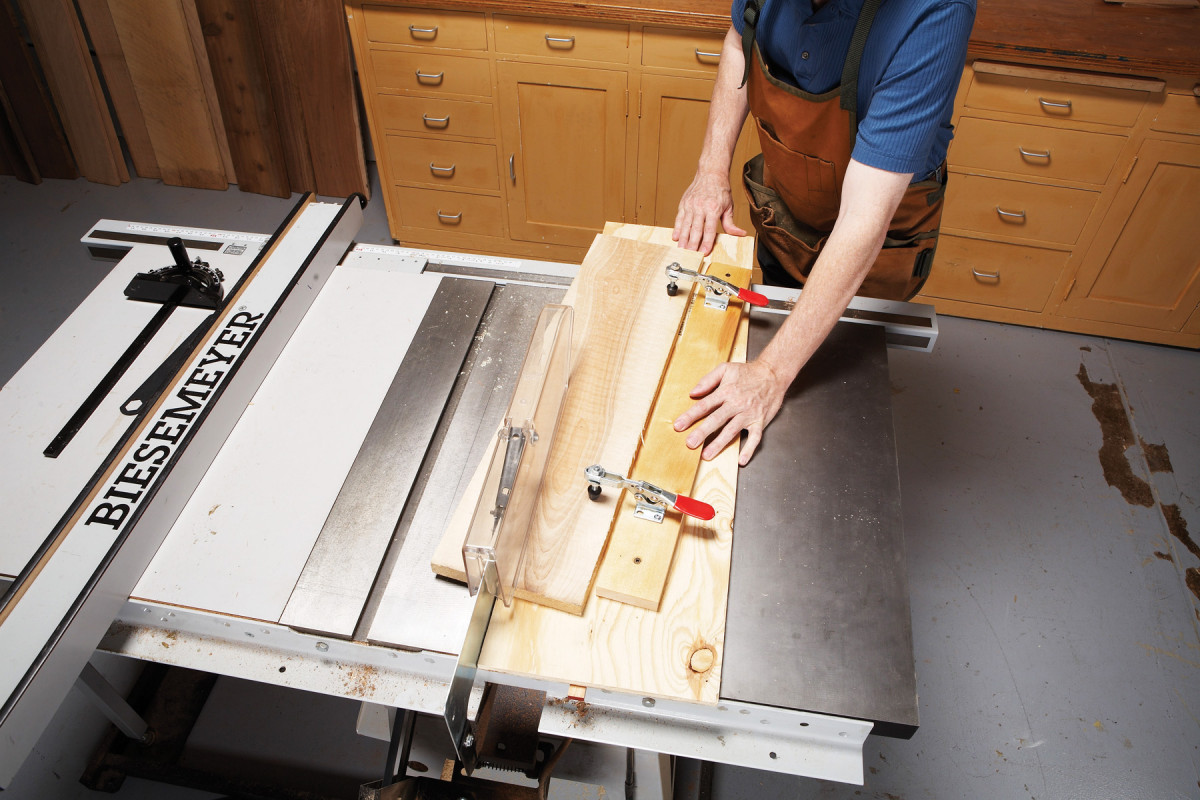
1. I use scrounged wood to make my boxes, so I don’t mind wasting a bit to get the figure I want. I use a jig to rip boards so their grain patterns run parallel to the edge.
1) I use lots of low-grade lumber from a variety of sources. What I’m looking for is terrific figure; it’s OK if the boards are short or thin, because one box doesn’t require much material. If the figure runs at a slant, I use a sled with a runner and toggle clamps to make a straight cut (Photo 1).
2) I make boxes in a variety of sizes, depending on what the wood allows. These plans are for a relatively small box, but all my boxes have 7/16-in. sides and 1/2- in. lids. Most lids (A) are glued from two or more pieces. I plane this wood to 9/16 in., glue the lid, then take it down to 1/2 in. using a drum sander.
3) The sides (B and C) must be straight and flat in order to make accurate miters. Mill this wood to 1/2-in. thick and 1/4 in. over the final width. Let it sit for a few days, then joint the face sides again and plane and rip the pieces to final dimensions.
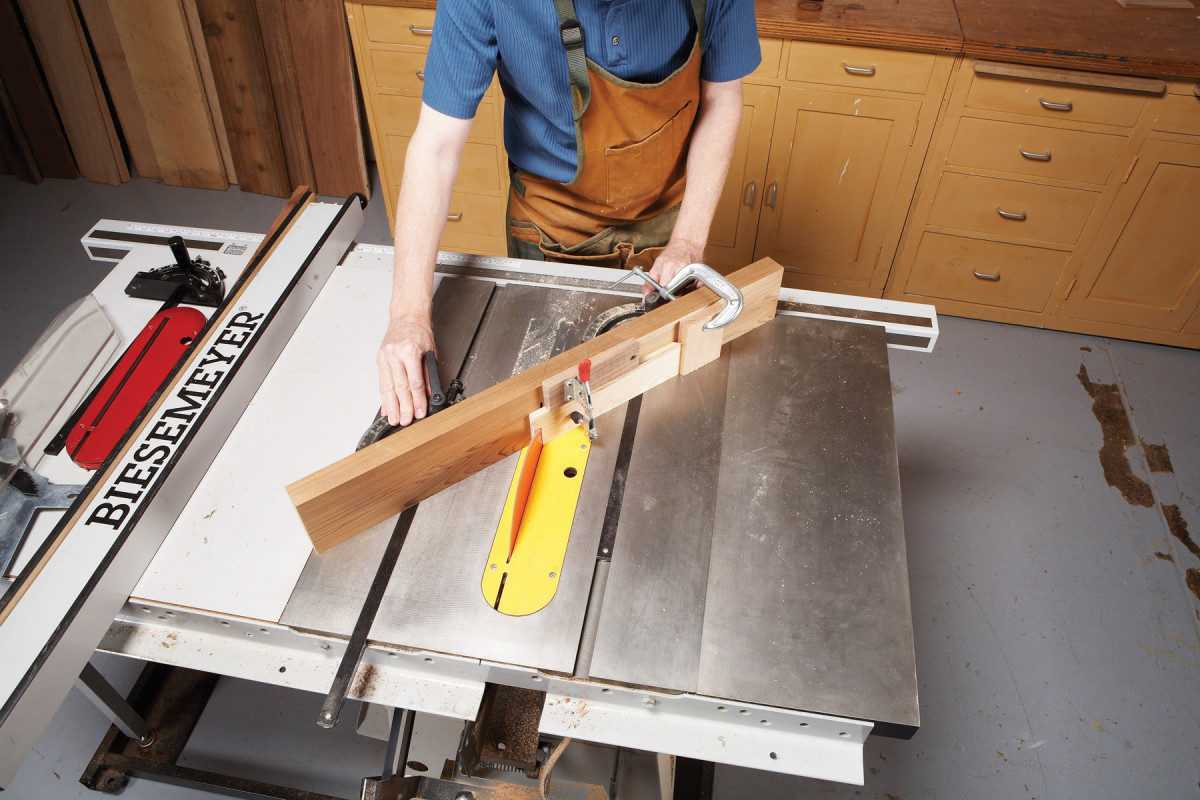
2. Miter the sides. Clamp the pieces to the subfence and use a stop block to cut them the same length. Fastening two miter gauges to the subfence eliminates wobble as you cut. Caution:You must remove your blade guard for this cut.
4) Cut miters using a crosscut blade (Photo 2). I get the best results on my contractor’s saw by standing the pieces on edge. I use a premium miter gauge that doesn’t wobble in the saw’s miter slot, but I’ve found that two standard miter gauges, fastened to the subfence, are just as stable.
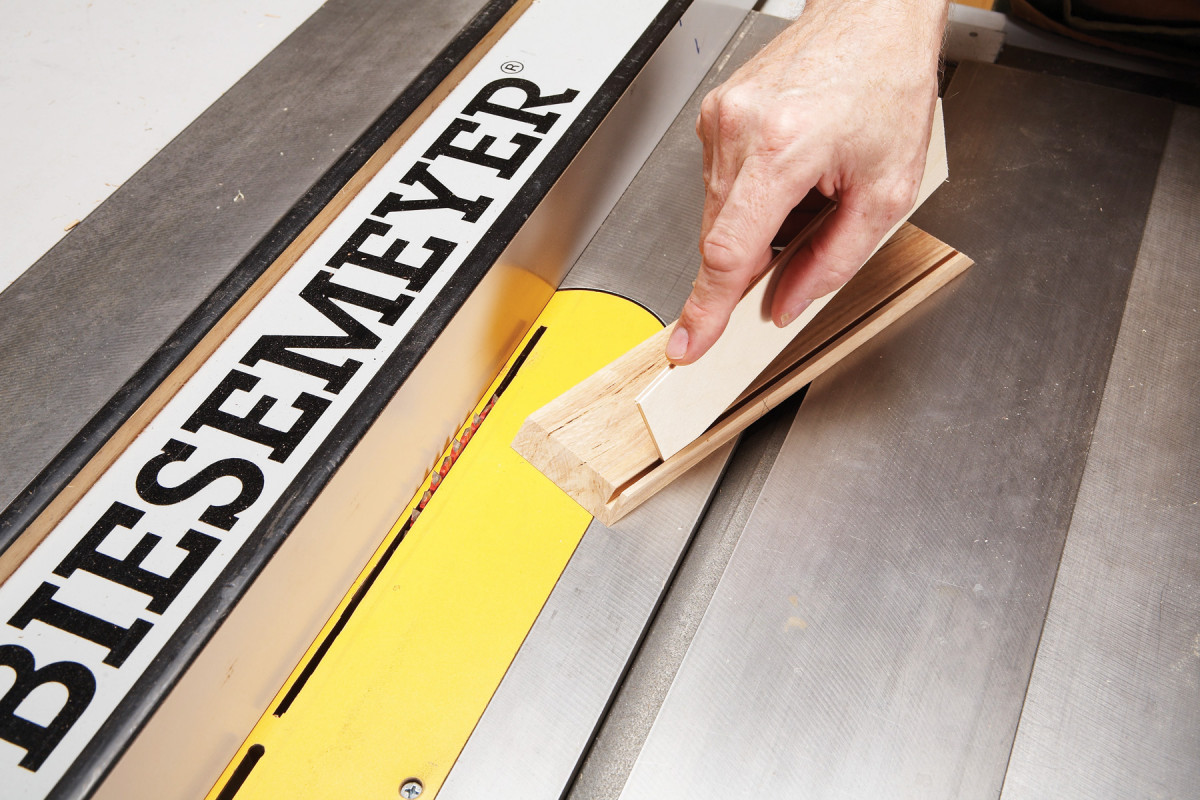
3. Saw grooves to receive a 1/8-in. plywood bottom. The fit can’t be tight, or the box will be too hard to assemble. Shift the fence about 1/64 in. to widen the groove until the fit is just right.
5) Saw grooves for the bottom (D) (Photo 3 and Fig. A). Set the fence 1/8 in. from the blade and saw each piece once, then move the fence about 1/64-in. farther from the blade and make a second pass. The plywood for the bottom should easily slip into the groove.
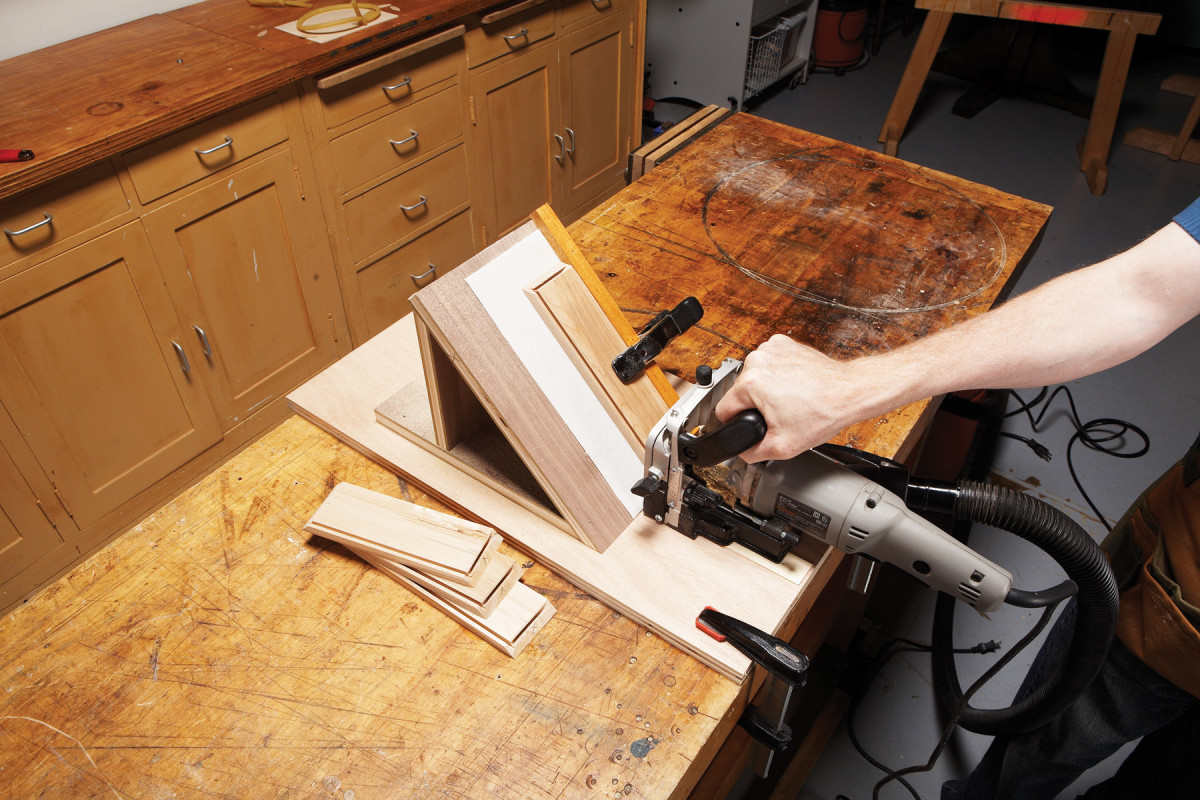
4. Cut biscuit slots in the miters. Build a 45-degree fixture to hold the pieces. Locate the slots just below the miter’s inside edge by raising the plate joiner on shims nailed to the fixture
6) I use a fixture to cut biscuit slots (Photo 4). I use special FF biscuits, which are very small, because there’s more leeway in locating the slots. Only a few plate joiners can make slots this size, however, so I’ve experimented with #0 biscuits. They work fine, but the slots have to be precisely located and the sides can’t be less than 7/16-in. thick. In fact, it would be better if they were about 1/32-in. thicker.
For making #0 slots using my Porter/Cable plate joiner, I nail 1/16-in. thick shims to the jig. This places the slot 1/16-in. below the miter’s inside corner. Experiment with scrap wood before you cut slots in the real pieces. The last thing you want to see are slots going all the way through the sides–and it’s mighty close!
Glue the Box
7) Cut the bottom to size. I use 1/8-in. thick plywood for making the bottom and dividers (E and F). This plywood is only available at craft and hobby stores, but 1/8 in. hardboard would be OK, too. When you figure out the bottom’s exact size, leave 1/32 in. of play all the way around, so the miters are sure to draw up tight. I use my crosscut blade to saw this thin plywood for a smooth, vibration-free cut Sand the plywood’s edges to make them easier to insert into the grooves.
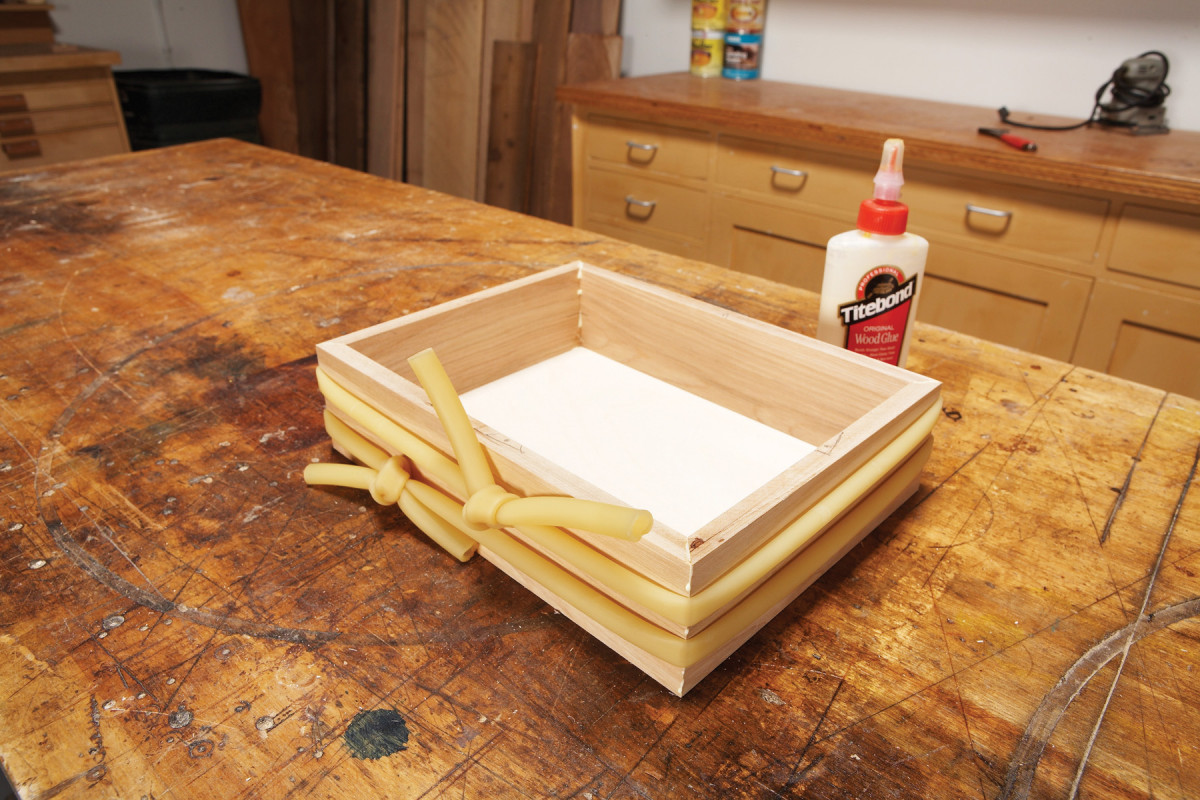
5. Glue the box using rubber tubing or a band clamp to pull the miters tight. After the glue is dry, sand the sides and their top edges, then apply a finish. You don’t have to sand or finish inside the box.
8) Apply glue to all the miters and slots and clamp the box together (Photo 5). I like rubber tubing because it’s inexpensive. You can get it at a medical supply or sporting goods store. Tie the knot beforehand, to make a loop that stretches taut around the box. One good thing about tubing: glue won’t stick to it.
9) After the glue is dry, sand the outside faces and top edges. Round over the corners so they aren’t sharp. Spray or brush a finish on the box and its lid. Finish both sides of the lid, but only the outsides and top edges of the box.
Add Felt Lining
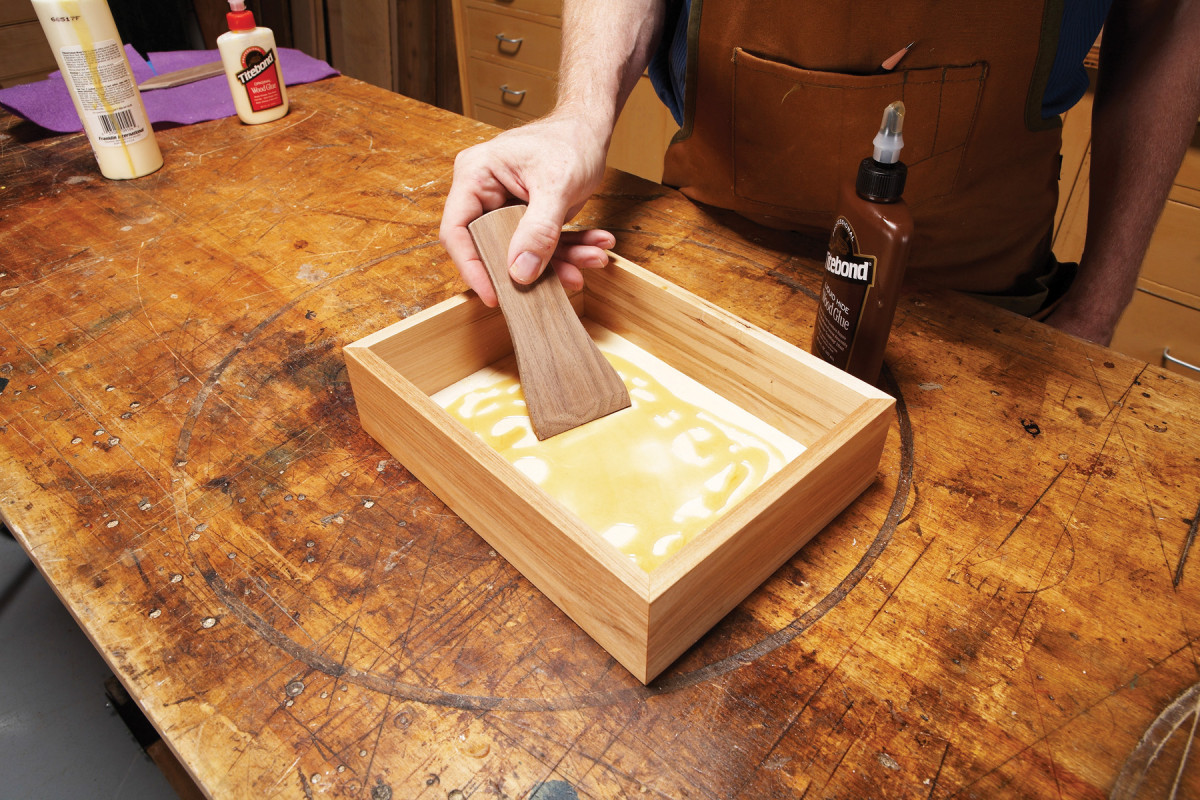
6. Spread a thin layer of glue over the bottom in order to attach a felt lining. Yellow glue works fine; liquid hide glue, as shown here, gives you a little more working time.
10) Cut a piece of felt, with notches, so its center section exactly fits inside the box. Scissors work better than a knife. Dribble some glue on the box’s bottom. Use a thin wooden spatula with a tapered end to spread the glue (Photo 6). Make sure the glue is spread thin, or it will soak through the felt.
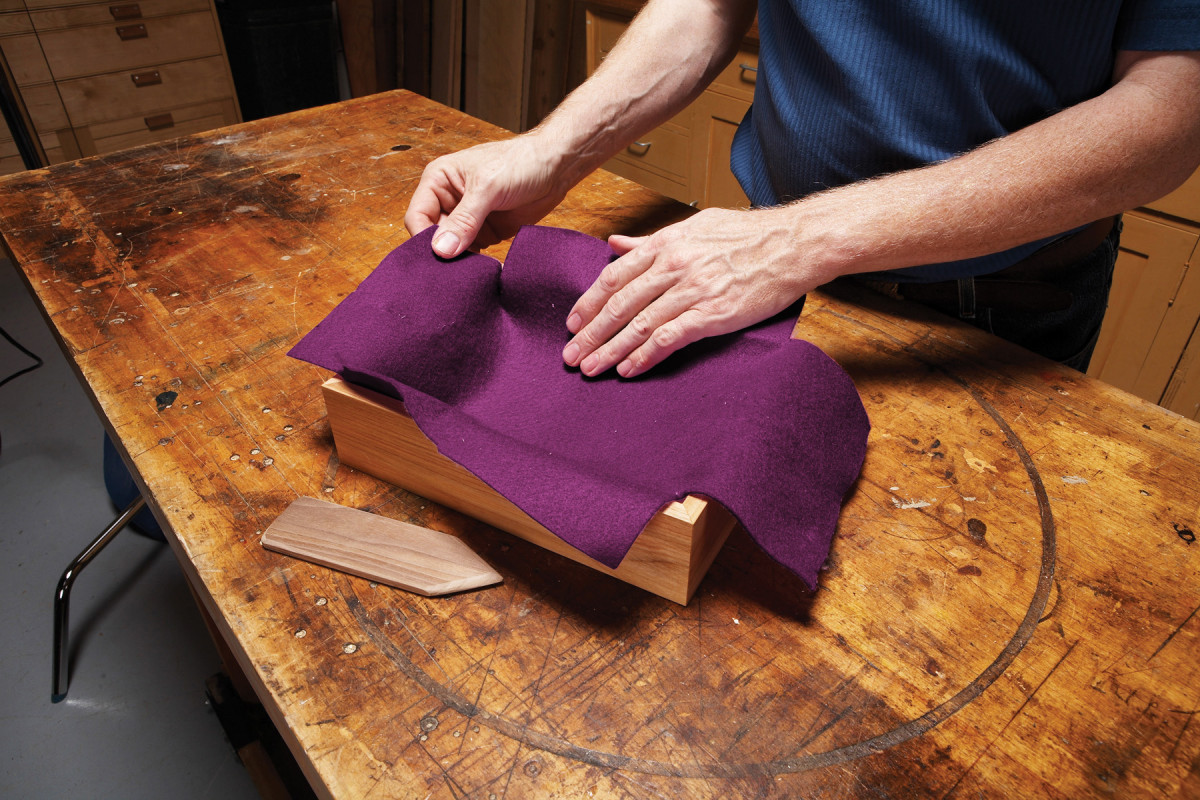
7. Place a piece of felt inside the box. Push down on the felt with a rounded wood stick to smooth it out. Then apply glue to the sides and smooth out each flap using the stick’s point to get into the corners.
11) Place the felt inside the box (Photo 7). Smooth it out on the bottom, making sure the cut corners line up correctly. Then glue the sides, one at a time. A pointed stick with rounded edges is an invaluable tool for smoothing the felt near each corner.
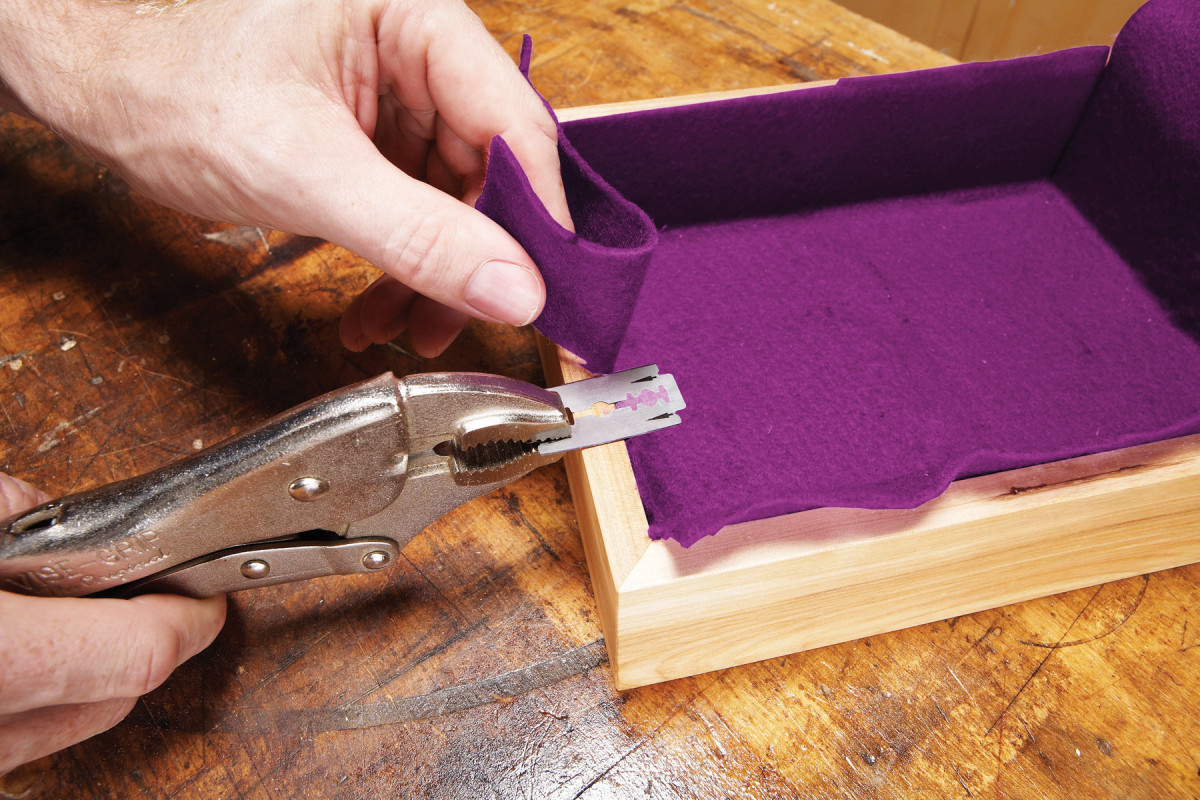
8. Trim off the excess felt using a doublesided razor blade held in a Vise-grip.
12) Cut the excess felt flush (Photo 8). The cutting tool has to be extremely sharp, so I use a double-sided razor blade.
Make the Dividers
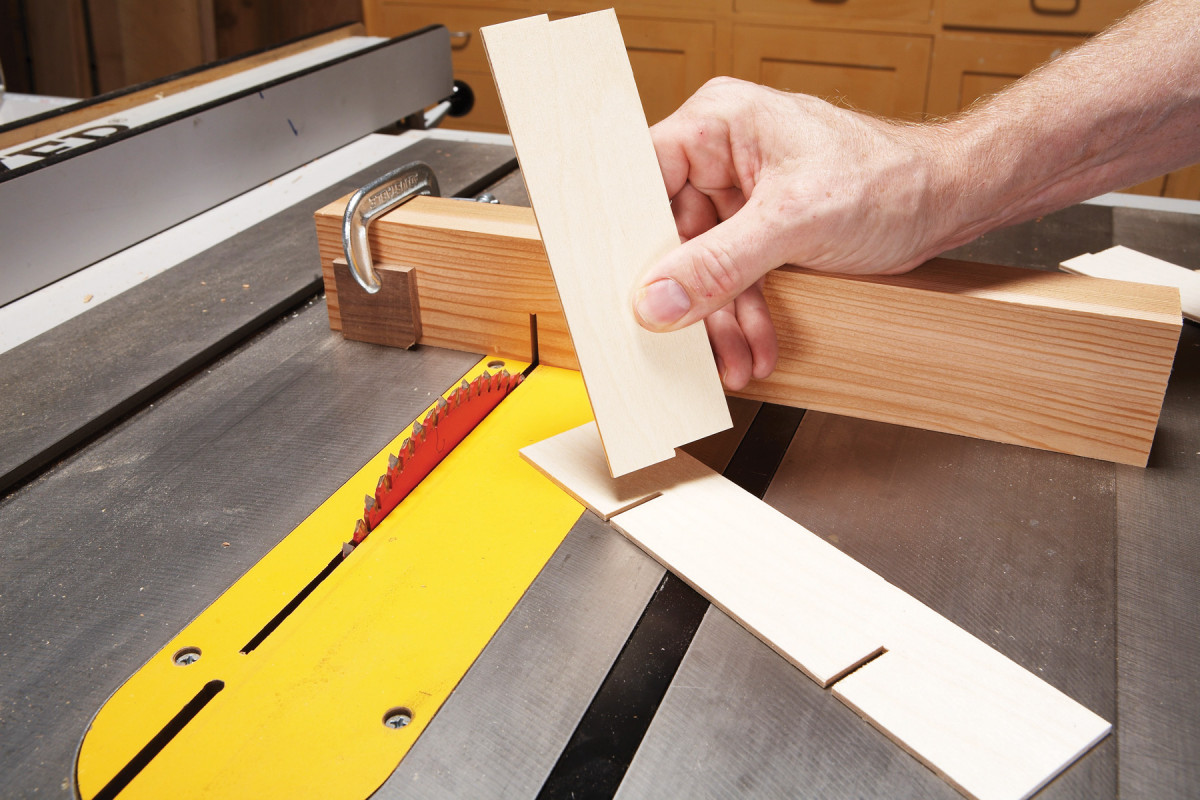
9. Cut slots in the dividers to make bridle joints. Using 1/8-in. plywood for the dividers, the slots are one saw-kerf wide. If that’s too tight, insert a piece of paper next to the stop block in order to widen the slots.
13) Cut the dividers (E and F) to width and length. It’s important that their lengths are just right to make a snug fit. Cut the notches on the short dividers first (Fig. B). Make these by placing a stop block right next to the blade. Move the stop block and cut notches in the long dividers (Photo 9 and Fig. B).
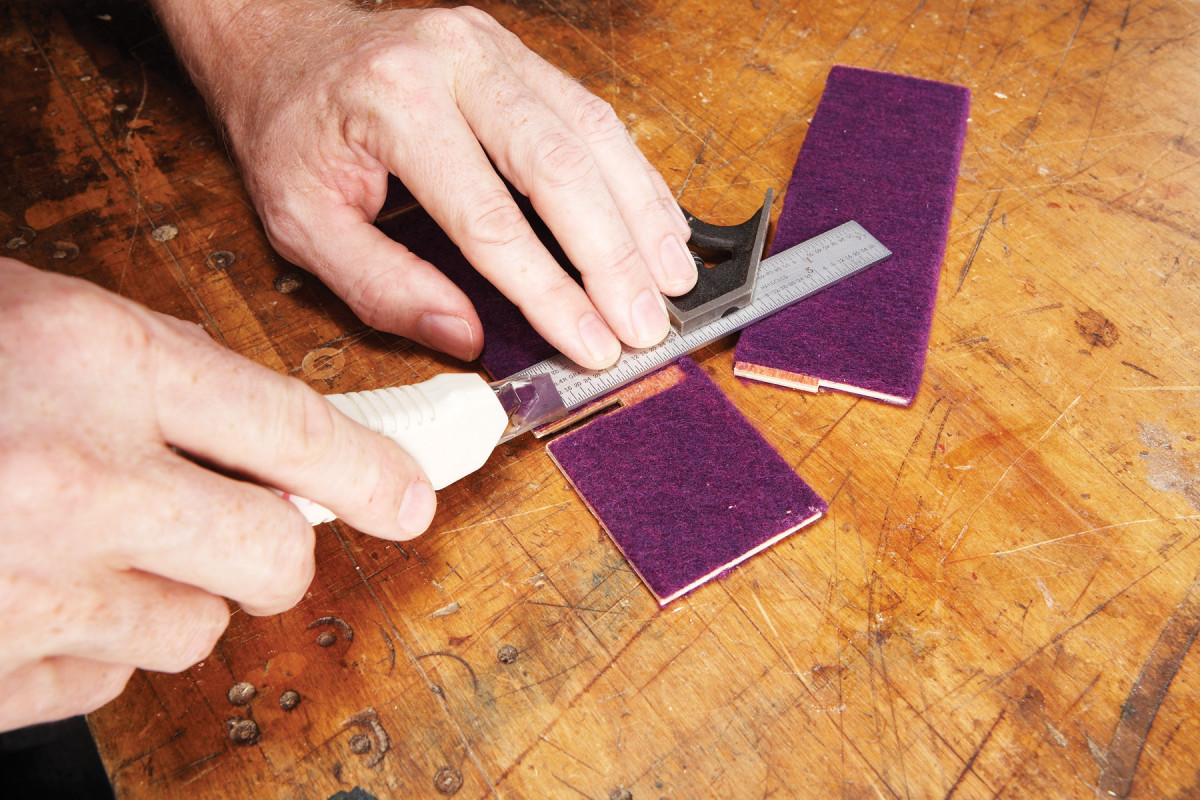
10. Glue and wrap felt around the dividers. Cut around the slots so the dividers butt tight against each other.
14) Glue felt on the dividers. Wrap it around the dividers’ top edges. Trim off the excess. Cut around each notch (Photo 10). Assemble the dividers and insert them into the box. The assembly should fit tight, but not so tight that you’d have to hammer it in place.
Add the Lid
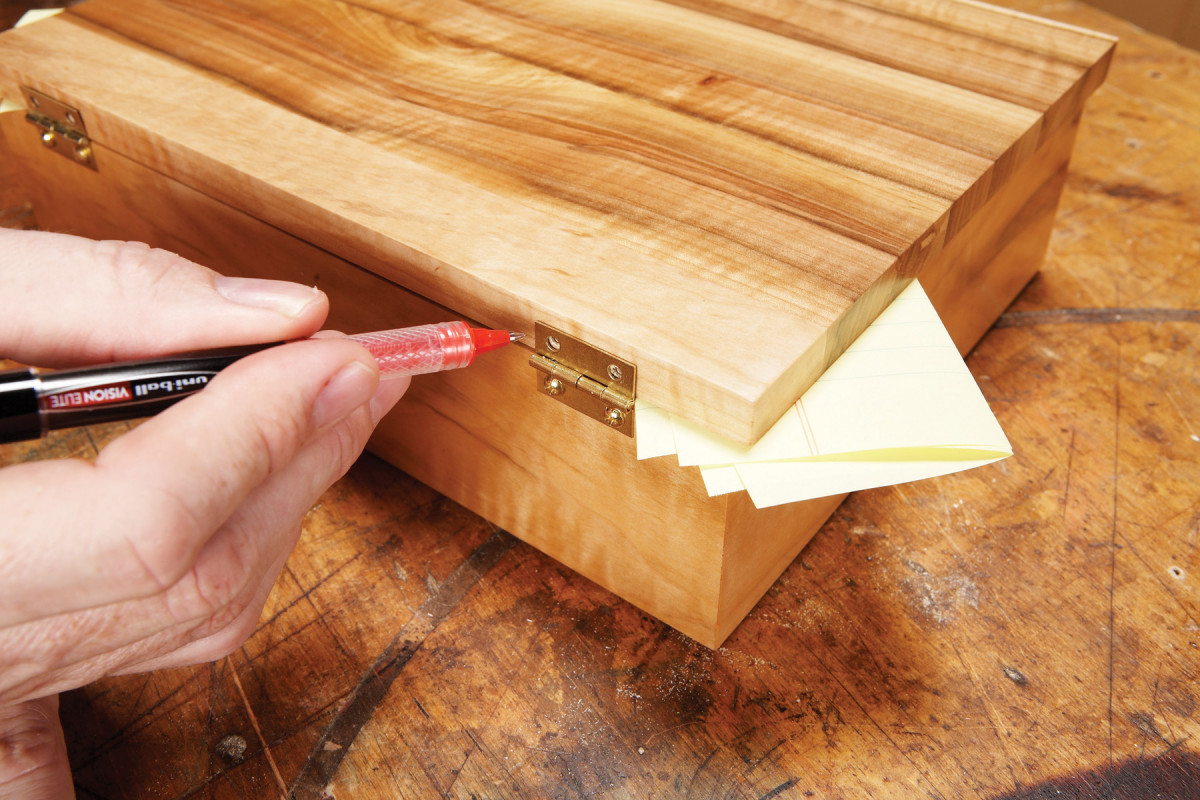
11. Install hinges on the box, then mark screw holes for the lid. Place four pieces of paper between the box and lid so the lid won’t bind as it closes
15) Screw hinges to the box. I keep things simple: they’re mounted right on top of the back. These hinges use delicate brass screws, so be sure to pre-drill the holes. Place four pieces of paper on top of the box. Place the lid on the box, flush with the back. Mark the screw holes with a felt-tip pen or awl (Photo 11). Predrill holes in the lid and attach it to the hinges.
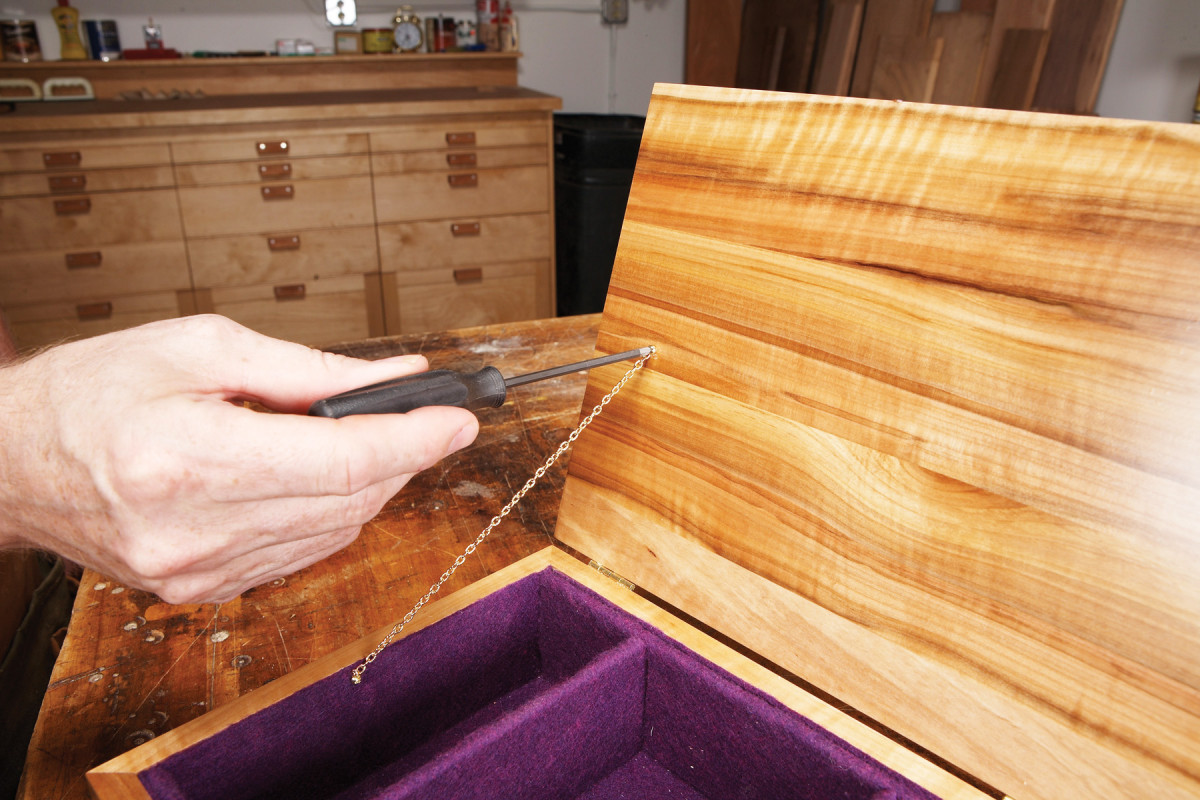
12. Install a chain to hold the lid open. When I make a lid, I look for wood with beautiful figure on both sides. I think a box should be just as pretty when it’s open as when it’s closed.
16) Install a chain. On this box, it’s about 6-1/2 in. long. Locate the screw on the box’s side 3-3/4 in. from the inside edge of the back, 1/4 in. down from the top edge. Stretch the chain tight and lean the lid back a few degrees past vertical to locate the other screw. This screw should be 1-1/4 in. away from the lid’s edge so the chain falls inside the box as it’s closed (Photo 12).
Jewelry Box Cut List
Here are some supplies and tools we find essential in our everyday work around the shop. We may receive a commission from sales referred by our links; however, we have carefully selected these products for their usefulness and quality.
Mr. Adair, I just wanted to thank you for such a well-written box-making article that is full of useful tips. I too love making boxes and am a hobbyist myself. This is the most helpful and informative box-making related article that I have ever read, and sir, I have read many. Thank you, much and Happy Thanksgiving.
H Davis.