We may receive a commission when you use our affiliate links. However, this does not impact our recommendations.
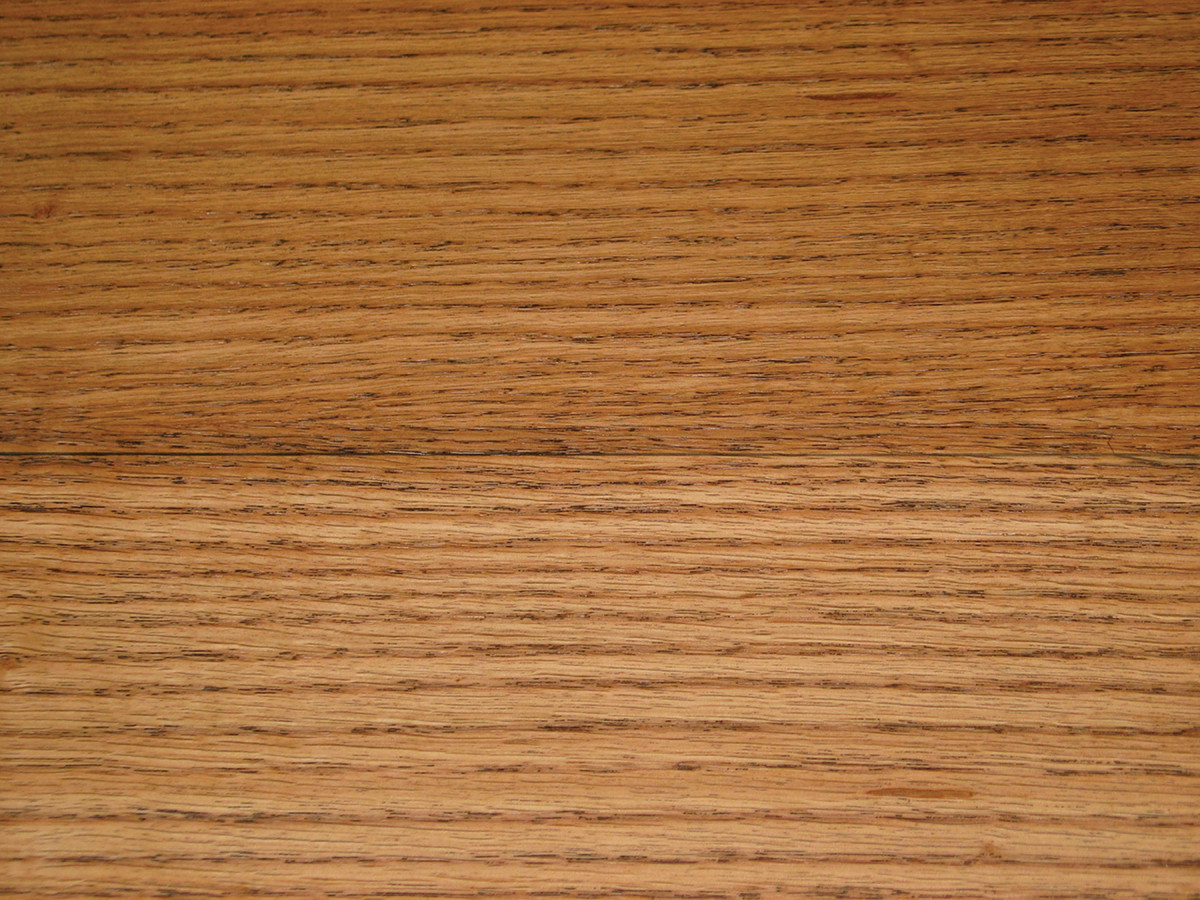
Fine sanding. Sanding to finer grits, as on the bottom half of this oak panel, which was sanded to #600 grit as opposed to #180 grit on the top half, doesn’t close the wood’s pores as is often claimed. It creates finer scratches that retain less stain after wiping off the excess.
Knowing which half to believe is why finishing seems so difficult.
Many years ago I coined what I call my “half-right rule.” That is, half of what you read or hear about finishing is right; you just don’t know which half.
You may suspect that I developed this rule in response to all the contradictory information published in woodworking magazines, but I didn’t. The rule originated from my experience with the elderly clerk, Glen, at the paint store down the street from my shop, where I bought most of my supplies.
I always enjoyed my trips to the paint store because I was greeted warmly, and I knew I was going to learn something. Glen had been around paints and finishes all his life, and he gave me many tips that helped me raise the quality of my work. He also led me astray just about as often.
He wasn’t misleading me on purpose, of course. He was merely passing along tips and explanations he had picked up from painters and finishers who he came in contact with. A lot of nonsense is passed around in these circles, and some of it has become deeply embedded.
Here are a few examples that may sound familiar.
■ Thin the first coat of finish by half for a better bond. On the contrary, full-strength finishes bond perfectly well. The purpose of thinning is to create a thinner build that is easier to sand.
■ Don’t sand to too fine a grit or you’ll close the wood’s pores and it won’t take stain as well. You don’t “close” the pores with finer grits. You create finer scratches that retain less stain when you wipe off the excess.
■ Use sandpaper to soften sharp edges because these will show wear too easily. The better reason to soften edges with a couple of sandpaper passes is because the finish is likely to peel away from sharp edges.
■ The longer you leave a stain wet on the wood the more it soaks in and the darker the coloring when you wipe off the excess. This isn’t the way it happens. The stain isn’t soaking deeper; the thinner is evaporating, which leaves a higher colorant-to-liquid ratio.
Notice that in all these examples the problem with the instruction is not that you should or shouldn’t do it. It’s the explanation of what’s going to happen or why it happens or how it happens that is incorrect.
When the “what,” “why” and “how” explanations are wrong, you are left struggling to understand finishing. Which side of the half-right rule is correct?
My Culpability
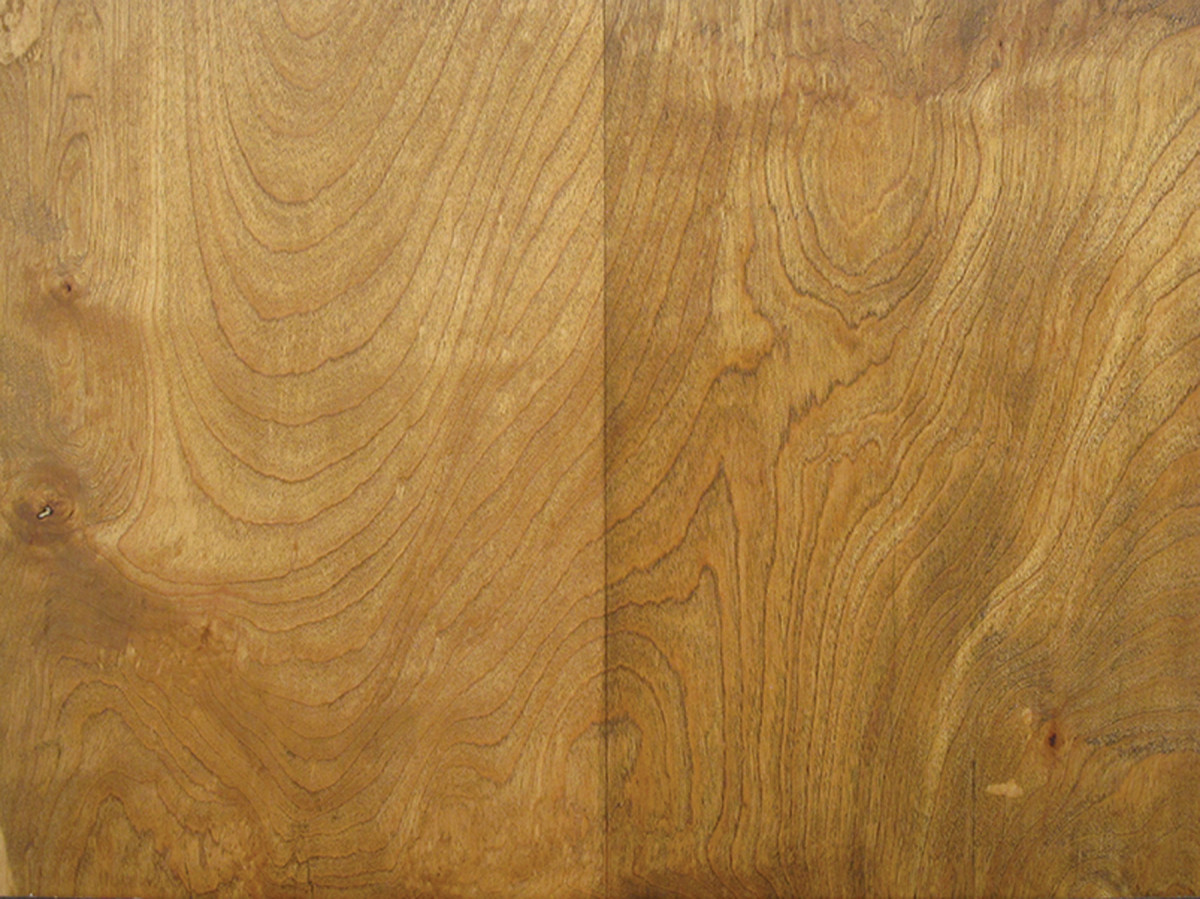
Stain gets darker. I wiped off an oil stain within a minute (left) and after 30 minutes (right). After 30 minutes the stain is darker, not because it penetrates deeper but because a lot of the solvent has evaporated, leaving a higher colorant-to-thinner ratio.
In addition to nonsense explanations, mislabeling by manufacturers and poor instructions are also at fault. Here, I have to take some responsibility for contradictions you have to work through. Take these examples.
■ Manufacturers typically tell you to apply stain within two hours when using a wood conditioner to reduce blotching. I’m telling you that you have to let the wood conditioner, if it’s oil- or varnish-based, dry at least six hours to overnight to get good results.
■ Watco and other manufacturers of Danish oil, which are mixtures of oil, varnish and thinner, tell you to let the first coat penetrate for 30 minutes then apply a second coat and let it penetrate 15 minutes. Finally, wipe off, and the finish is ready to use in 8 to 10 hours. I (and others) tell you to let the first coat dry overnight after wiping off the excess. Then sand lightly, apply a second coat, wipe off and let dry overnight again.
■ Manufacturers of virtually all brands of teak oil tell you that their finish provides UV resistance for outdoor use. I tell you that this isn’t true. You need a build (with UV absorbers added) to effectively provide UV resistance, and there is no build with oil finishes.
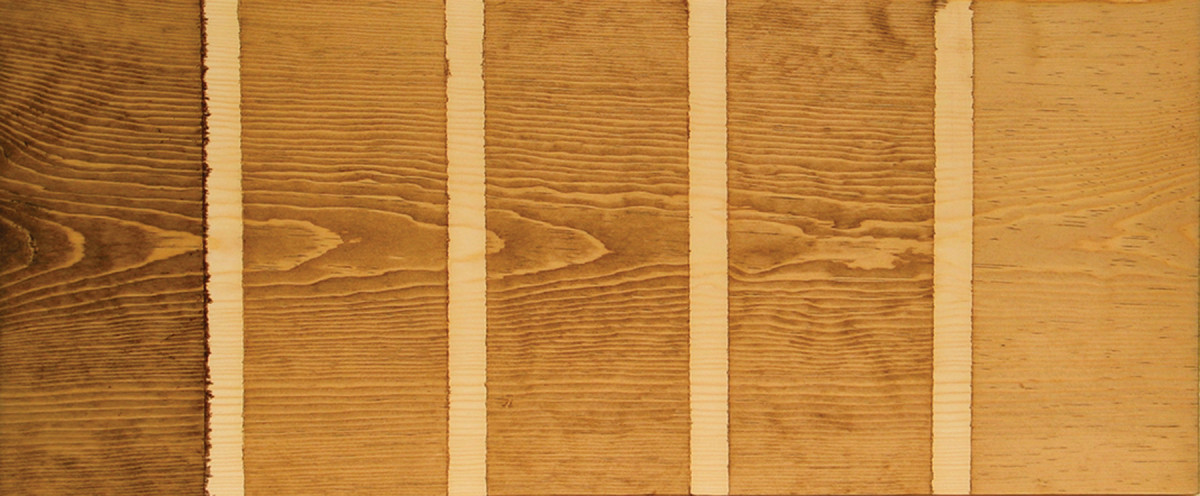
Wood conditioner. Instructions tell you to apply stain within two hours of applying the wood conditioner. This doesn’t reduce blotching. In fact, waiting for two hours increases blotching because more of the thinner has evaporated. Here, I applied stain directly to the top section of this pine board. Then I applied wood conditioner to the rest of the board and stain immediately, stain after 10 minutes, stain after two hours and stain the next day. After the wood conditioner dried, the color is lighter, but there isn’t any blotching.
Again, you have to decide which side of the half-right rule is correct.
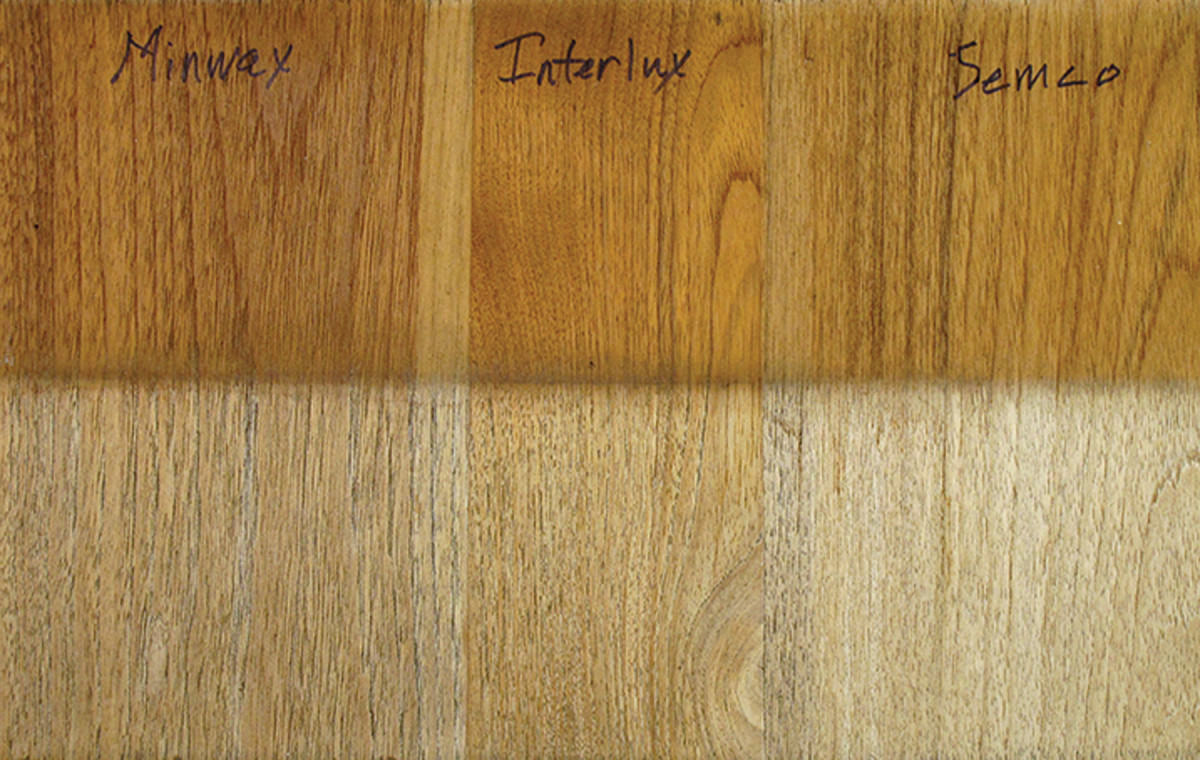
Teak oils. Oils sold for preserving teak don’t work well, as shown by the fading on the bottom half of this teak panel after less than two months of exterior exposure. Excess teak oil has to be wiped off, so there is no build. For UV absorbers to be effective against sunlight, there has to be a build of finish, as happens with many coats of marine varnish.
What’s the Solution?
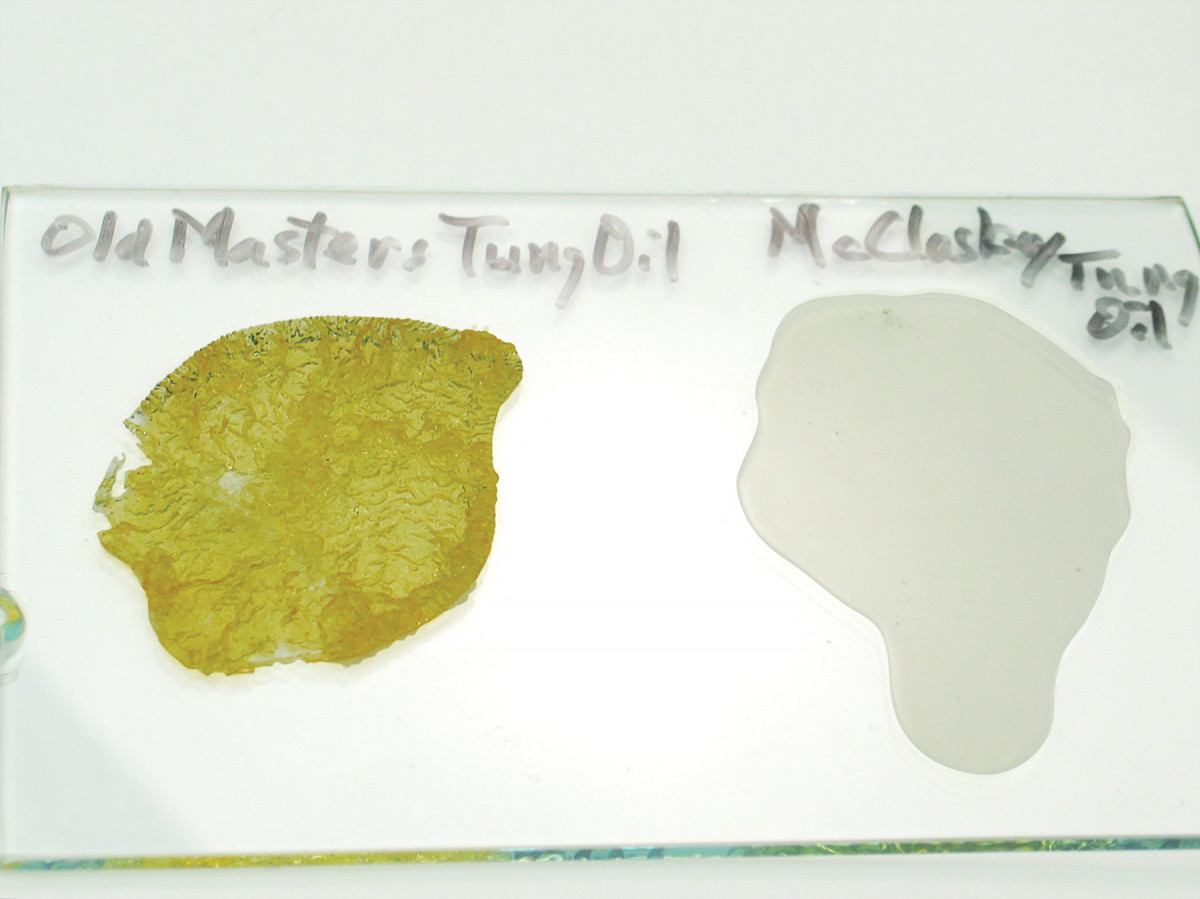
Tung oil. Clearly, the dried puddles of these two finishes are very different, yet both are labeled “tung oil.” This labeling has caused great confusion for many years. The finish at the top is actually thinned varnish (“wiping varnish”). It has nothing to do with tung oil (shown at bottom).
Unfortunately, I don’t think there is an easy solution. Many people pass on information about finishes, including store clerks and many who write about finishing who have never really done much of it. These people often don’t have the experience to contradict what they hear from others or read in the literature.
I can tell you from my own experience that it took me a long time to feel secure enough contradicting what I was hearing to actually say or write that it was wrong. When everyone else is saying the same thing, the inclination is to think that your own experience is lying to you, somehow. Sometimes, I just put something “out there” to see if I got any push back.
For example, I think every manufacturer of wood conditioner says to apply the stain within two hours. It took me a decade of knowing this didn’t work, because the wood still blotched when I followed the instructions, to finally realize that the explanation was drying time. My “washcoats” using thinned lacquer worked well quickly because lacquer dries so much faster. Varnish-based wood conditioner just requires much longer to dry.
It also took me a long time to contradict the prevailing claim that shellac is the best sealer. I finally got the courage to say this can’t be true after I learned that no large cabinet shop or furniture manufacturer uses shellac at all. (I should be careful saying “none” because there might be an exception somewhere.)
Maybe most difficult of all was figuring out what tung oil was all about. Everyone knew there were differences. All sorts of attempts were made to account for these: “resin fortified,” “modified,” “processed,” etc. Finally, a chemist friend suggested that I see what happens when I let puddles of various brands dry on glass, and he tested the brands to see what was in them. Then it was clear. Many of the brands aren’t tung oil at all. They are varnish thinned with paint thinner. They’re just falsely labeled.
When products are labeled correctly with good instructions for using them, and the what, why and how mythologies are cleared up, finishing won’t be difficult at all. The half-right rule will disappear.
Here are some supplies and tools we find essential in our everyday work around the shop. We may receive a commission from sales referred by our links; however, we have carefully selected these products for their usefulness and quality.