We may receive a commission when you use our affiliate links. However, this does not impact our recommendations.

Can America’s most recognizable woodworking personality actually retire?
Editor’s note: This interview originally appeared in the November 2012 issue of Popular Woodworking
Norm Abram first stepped in front of a television camera in 1979 as the lead carpenter on “This Old House,” a show on which he still appears. A decade later, Norm began “The New Yankee Workshop,” and for 21 seasons he taught a glued-to-the-screen audience how to make furniture. Norm never skipped the hard parts, and while he didn’t make them look easy, he did show you that they were doable. As such, his gentle smile and reassuring manner coaxed countless people to take up the craft of working wood.
He has appeared on lots of other shows as well as in countless magazines, including two articles in the August 2005 issue of Popular Woodworking Magazine (#149). “The New Yankee Workshop” may be over, but Norm is hardly retired. He just bought a new old house that he’s renovating and he’s mulling over ideas for a new shop, so he can keep building and building.
In a recent discussion, Norm talked about TV, the Internet, woodworking and safety.
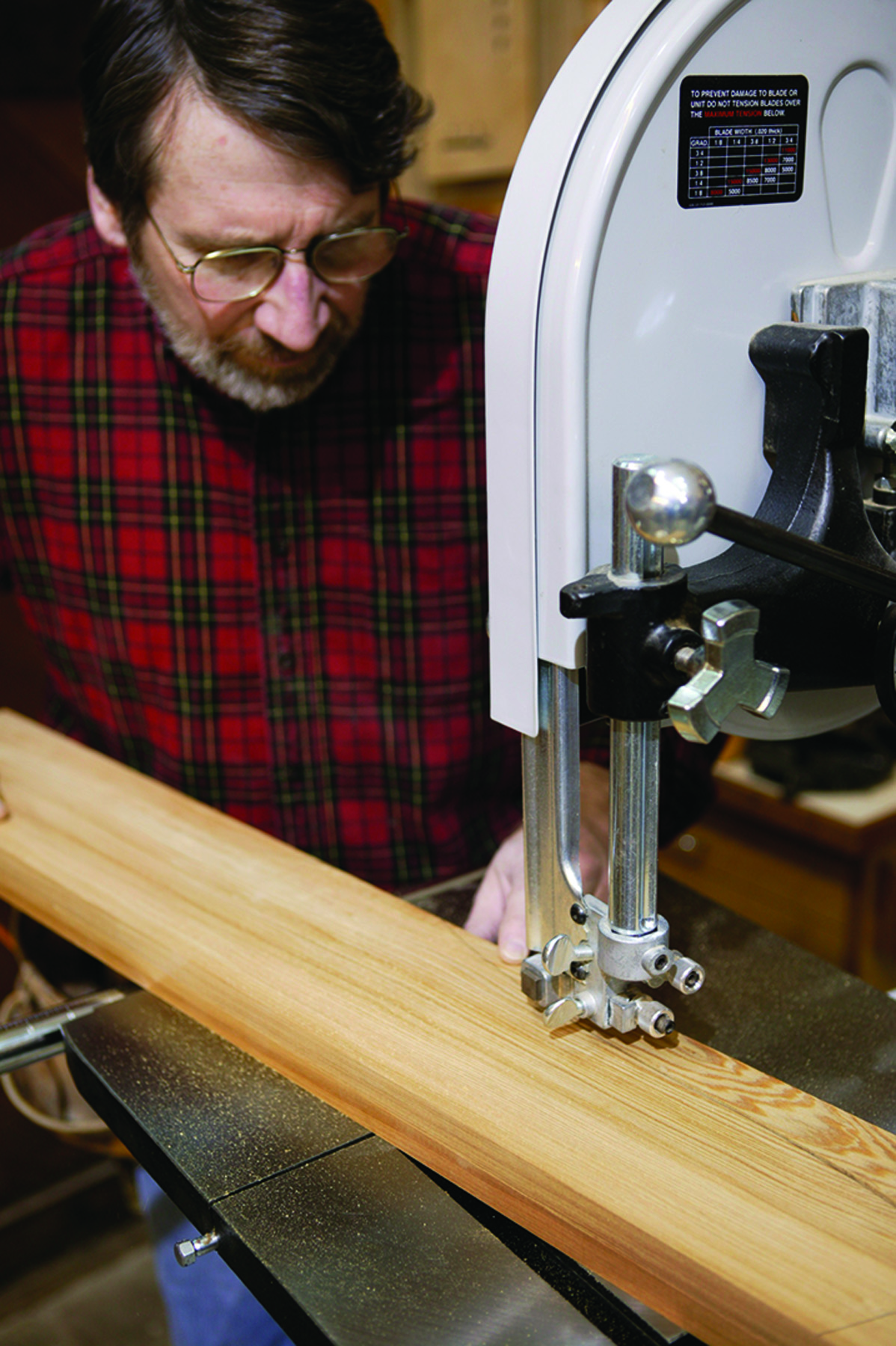
The real deal. Norm developed his skills while working as a carpenter, and those skills led to his appearances on “This Old House.”
Your show, “The New Yankee Workshop,” introduced countless people to the craft. What’s the best thing people can learn from watching a woodworking television show? Also, what are the limits of TV? In other words, what can’t people learn from watching “New Yankee.”
In the television show, we touched on every step in the process of making a piece of furniture. Because of the time constraints we couldn’t show every setup – every time we set the rip fence on the table saw, for instance. And if there were four table legs to make, for instance, we’d only show how to make one of them. The idea was to give a woodworker the inspiration to try building a piece of furniture.
Sometimes people who ordered the plans from an episode would write to say that they thought the cutlists should have exact measurements for every single piece of wood. I’d tell them that for many of the pieces the cutlists only contain approximate dimensions to be used as a guide. Part of making furniture is cutting and fitting pieces as you work your way through the piece. It’s a step-by-step process.
For all the confidence and inspiration we gave viewers – and I think video is better at this than a book or magazine – there are some things that television can’t do. It can’t teach you how it feels to have a tool in your hand or what wood grain feels like. It can’t show you what it’s like to squeeze just the right amount of glue out of a tight mortise-and-tenon joint. Hands-on is the only way to learn. You have to get out in the shop and work the wood, learn how the tools work.
So, watch a video to get inspired, then get out there and put that inspiration to work.
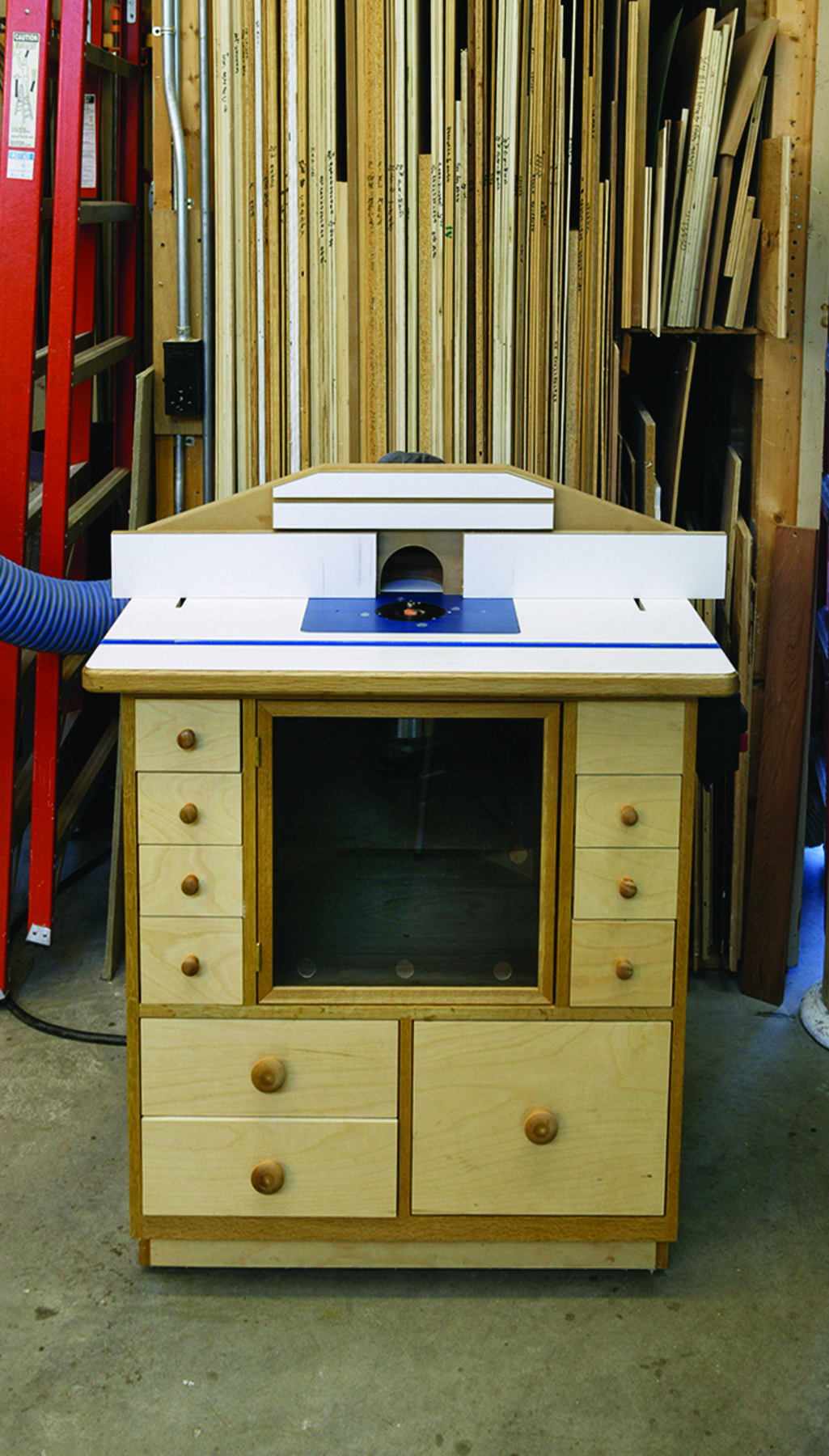
Popular project. This router table was one of the show’s most popular projects; versions of it can be seen in shops around the country.
What’s the appeal of woodworking in the Internet age? It seems as though today’s focus is always on the newest electronic gadget or technology. How does an ancient craft such as woodworking compete against other activities that are vying for people’s time?
Woodworking gained a real momentum from the Internet, which is good, but the problem is that the Internet is a two-dimensional medium, and woodworking is a three-dimensional activity.
The danger will be if people start to rely on the Internet as a real woodworking community. If you think about it – and I know this is certainly true for me – there is a huge benefit to hanging out with other woodworkers and talking shop. Regardless of what some people want you to believe, you can’t get a real community with Twitter.
And unfortunately, there is lots of bad information online; some of it is really scary. It’s probably not intentional, but I’ve seen some content that sets up the illusion that you can do whatever you want and get away with it.
Similar to television, the best online woodworking content gets people to try something, get their hands dirty.
But, you know, I think what’s going to happen is that people are going to turn to woodworking as a way to get away from the Internet. People who spend their work days in front of a computer are going to go down to their shops to get away from the virtual world to something more real.
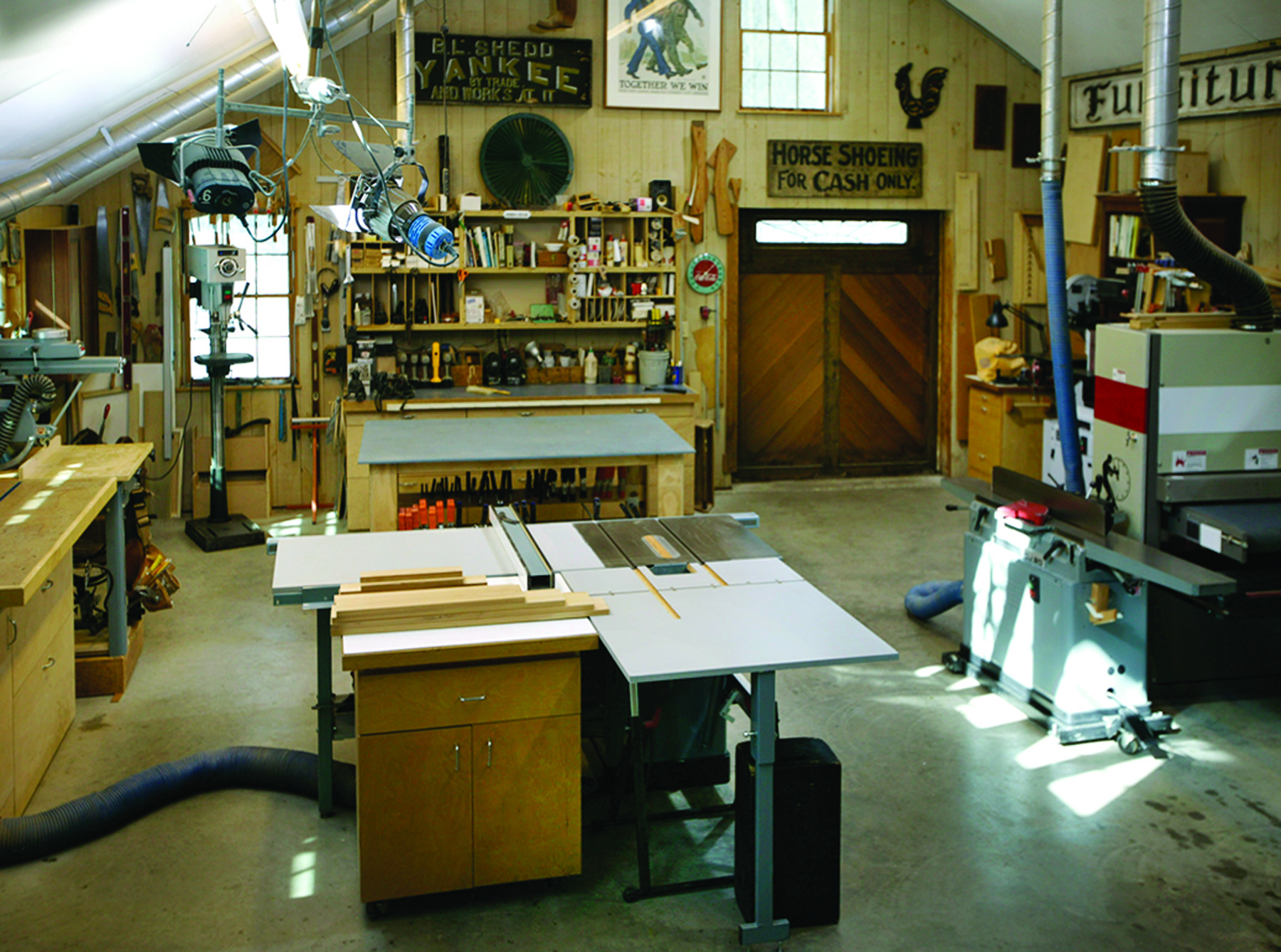
Familiar scene. For 21 seasons, Norm Abram hosted “The New Yankee Workshop” on national public television and inspired thousands of people to get involved with woodworking.
What’s next for woodworking? Any new tools or materials that have caught your eye lately?
Finishes and adhesives have gotten better in recent years. They are easier to use, quicker to clean up and – the major benefit – more environmentally friendly, not just for the people using them but for the planet, too.
Dust-collection devices on handheld tools have improved a lot since they first came out. Most of them actually work real well now.
One power tool that I really like is a hand-held tool that cuts mortises for a proprietary floating tenon. We all figured out pretty quickly that a standard biscuit joiner was good for registering pieces but not great for structural applications.
I was talking recently to a professional cabinetmaker about the floating-tenon tool and he said, “But the thing costs about $800.” My point to him was that the tool would pay for itself in one job, just because of the time it saves.
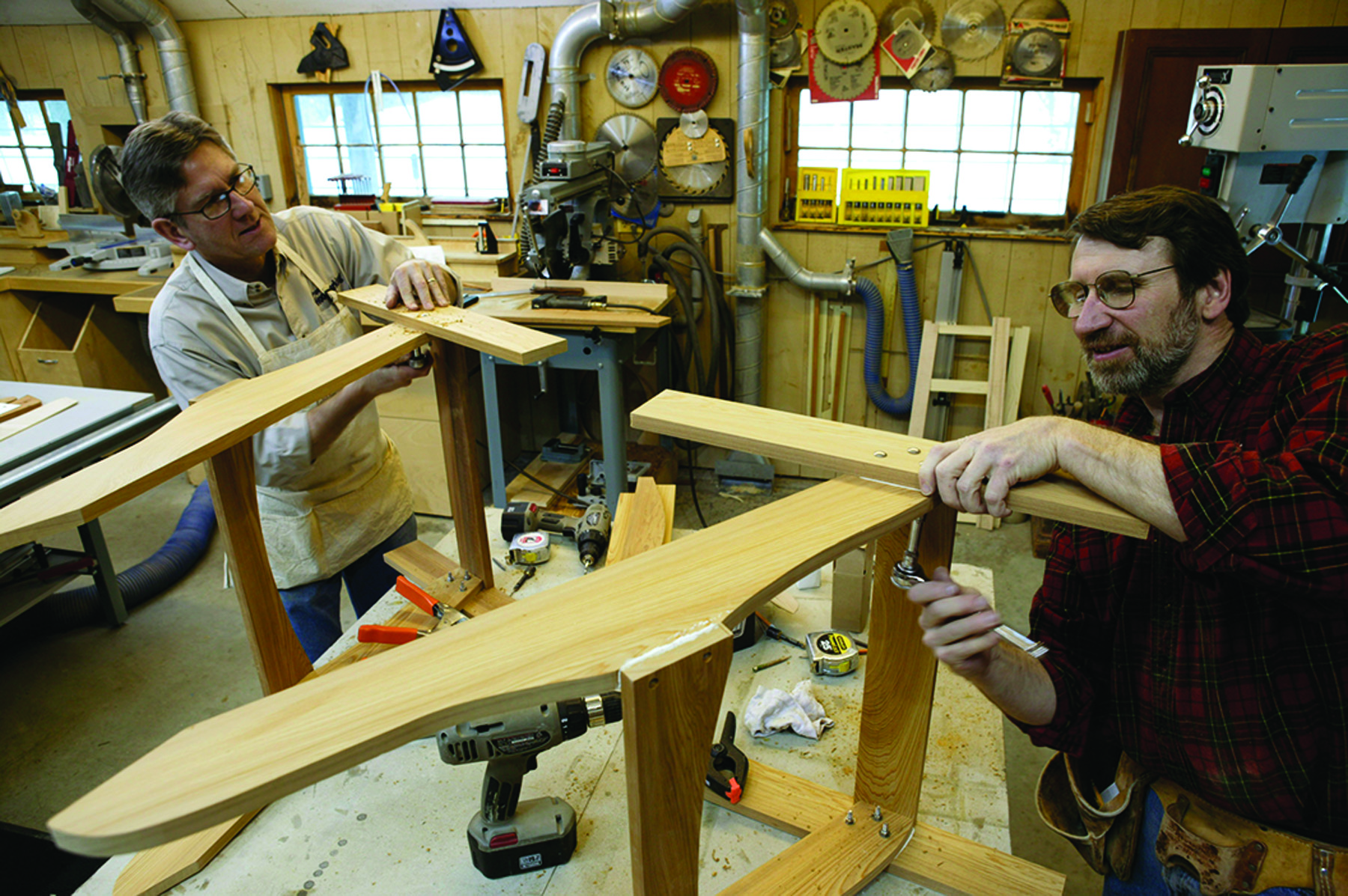
Tag team. In 2005, Steve Shanesy (who at the time was publisher and editor of this magazine) joined Norm in building a pair of Adirondack chairs.
You mentioned that one of your interests in semi-retirement is developing your own style of furniture. You said, for instance, that a Sam Maloof chair is immediately recognizable. Any hallmarks of the Norm Abram style that you can tell us about?
I’m not certain yet. It won’t be contemporary – that’s just not my thing. I think it will be an adaptation of period furniture, along the lines of what Thomas Moser did with Shaker furniture. Mainly, it will be very functional.
I’ve got some ideas for outdoor furniture, too. I built an Adirondack chair for “New Yankee” that had a much different seat angle than traditional ones. The best thing about it was that you could easily stand and get up out of the chair once you were seated, which is real difficult to do in the traditional design.
Maybe there won’t be a Norm Abram signature style, but it’s something I’m looking forward to playing around with.
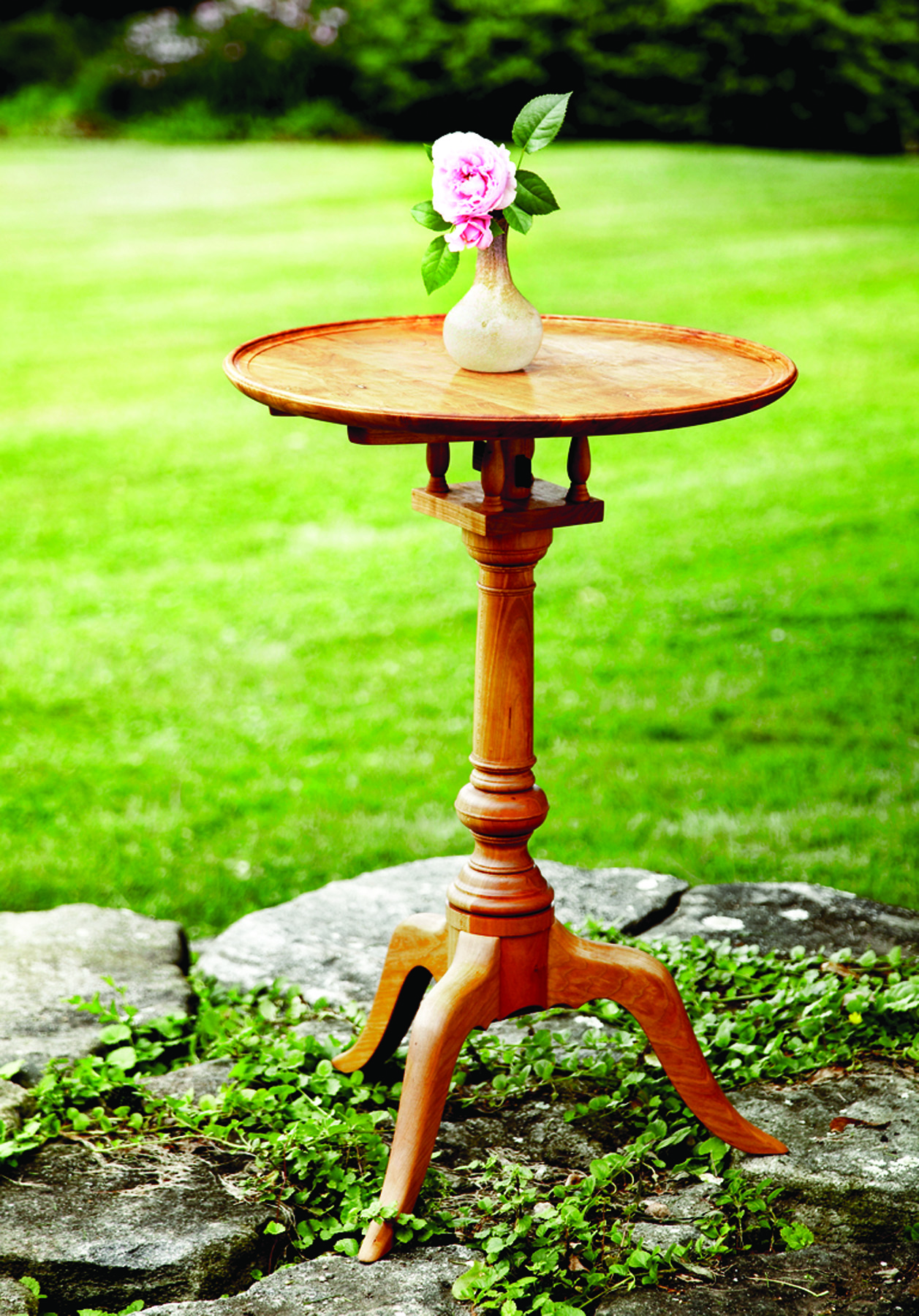
One of many. Abram built hundreds of pieces for the show, many of them reproductions from historic locations, such as this candle stand from Mount Vernon, built from a cherry tree that grew on the estate.
What do you admire most about period furniture makers, and conversely, what do you admire most about your contemporaries?
For me, one of the best parts of “New Yankee” was that I was able to travel around and look at some of the best furniture in the country. And as much furniture as I’ve seen, I am still amazed at the quality of work that was done by hand. The marquetry and inlays…just astounding.
Getting back to furniture styles for a moment: I really admire that so many of the period furniture makers never signed their work, yet it was distinctive enough that experts can identify otherwise anonymous furniture makers by the way a dovetail was cut or by the arch of a ball-and-claw foot. Of course, the experts are also getting regional clues by the secondary wood used or by the style of a geographic region.
My wife, Elise (who is an accomplished potter), and I go to a lot of furniture shows that have many contemporary pieces. I appreciate some of the craftsmanship, but lots of studio or art furniture stretches the limits of my definition of what furniture is. For me, it has to have function first. You have to be able to actually use a chair to sit in, for instance.
You always stressed safety on “New Yankee,” especially safety glasses. What do you think is the biggest reason woodworkers get hurt?
Woodworking takes real concentration. Distraction is the biggest enemy. Lose your focus and you’ll get hurt. If you have to have a TV in the shop, turn it off when you’re making a cut, especially if it’s with a power tool.
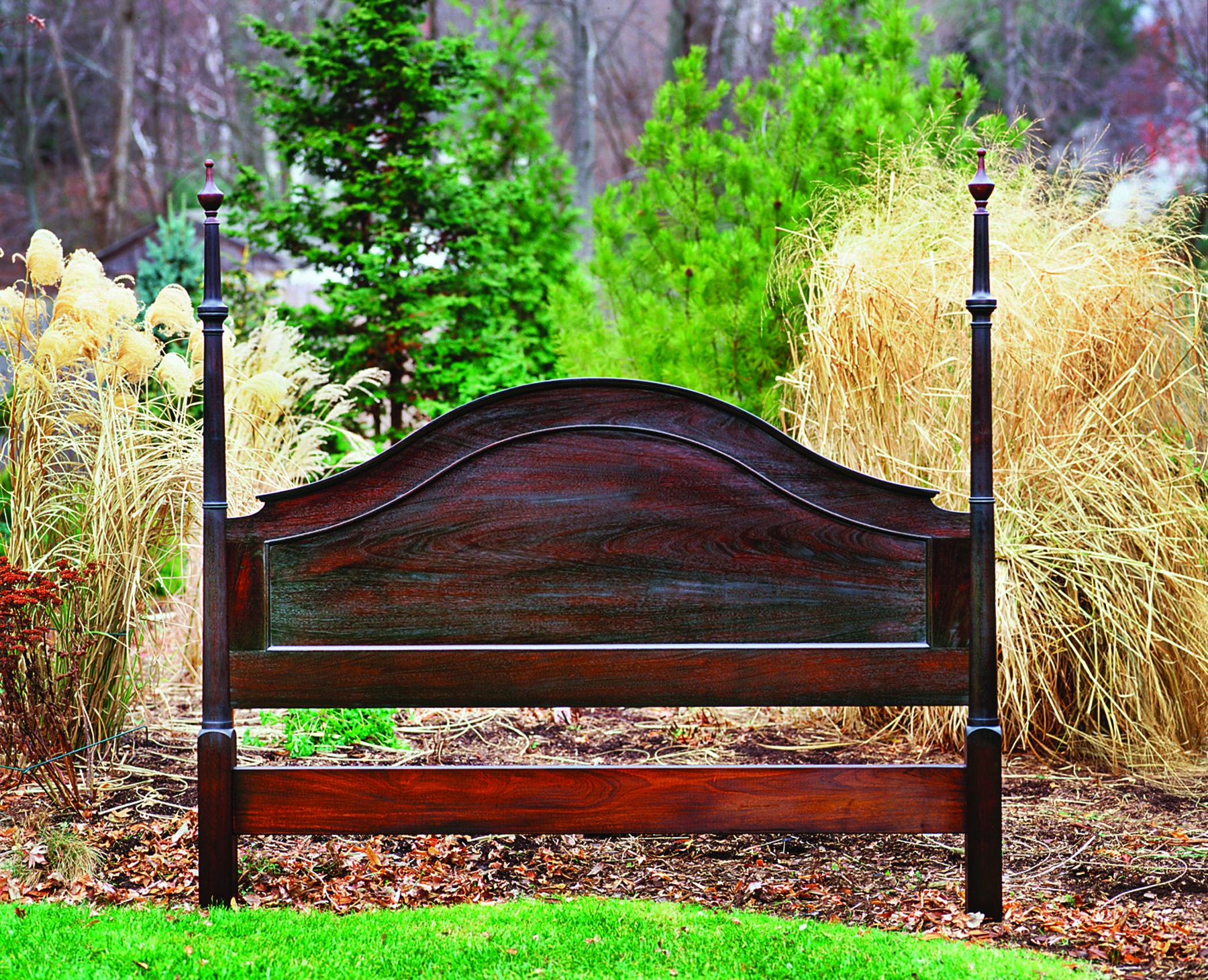
Man of many styles. Projects on the show ranged from simple shop projects to high-style pieces such as this elegant Regency headboard in mahogany.
How about “New Yankee Workshop” reruns or videos?
Put it on pause. Seriously, there are other factors that make it easier to get distracted. It probably goes without saying, but if you have a glass of wine or a drink with dinner, stay out of your shop for the night.
One thing I do to keep focused is talk to myself in the shop all the time. I tell myself what the next couple of steps are going to be because it will have an impact on what I’m doing at the moment. Then I can focus on process, technique and safety.
If you’re tired, you’ll get distracted. Same thing if you’re rushing; your mind will be on completing something rather than concentrating on what you’re doing right now. I’ve learned that the best thing for me to do is walk away if I’m getting tired or if my mind drifts, and come in early the next day.
Another thing that leads to injuries is trying to make the wrong tool work for the right job.
This isn’t woodworking, but it did involve a cutting tool: Recently, I was getting ready to open a bunch of “little necks” (a sweet New England bivalve, usually eaten raw) and I couldn’t find a clam knife, so I grabbed a regular kitchen paring knife. It was the wrong tool for the job, and I thought to myself, “This is just a bad idea.” Sure enough, I slipped and sliced the palm of my hand. Fortunately, no stitches.
Finally, make sure the tool you’re using is sharp. It sounds clichéd but it’s worth repeating: A dull tool is more dangerous than a sharp one. That’s because it takes more effort to cut with a dull tool, and when a dull tool slips off a piece of hard wood it can go right into your soft hand or arm or leg.
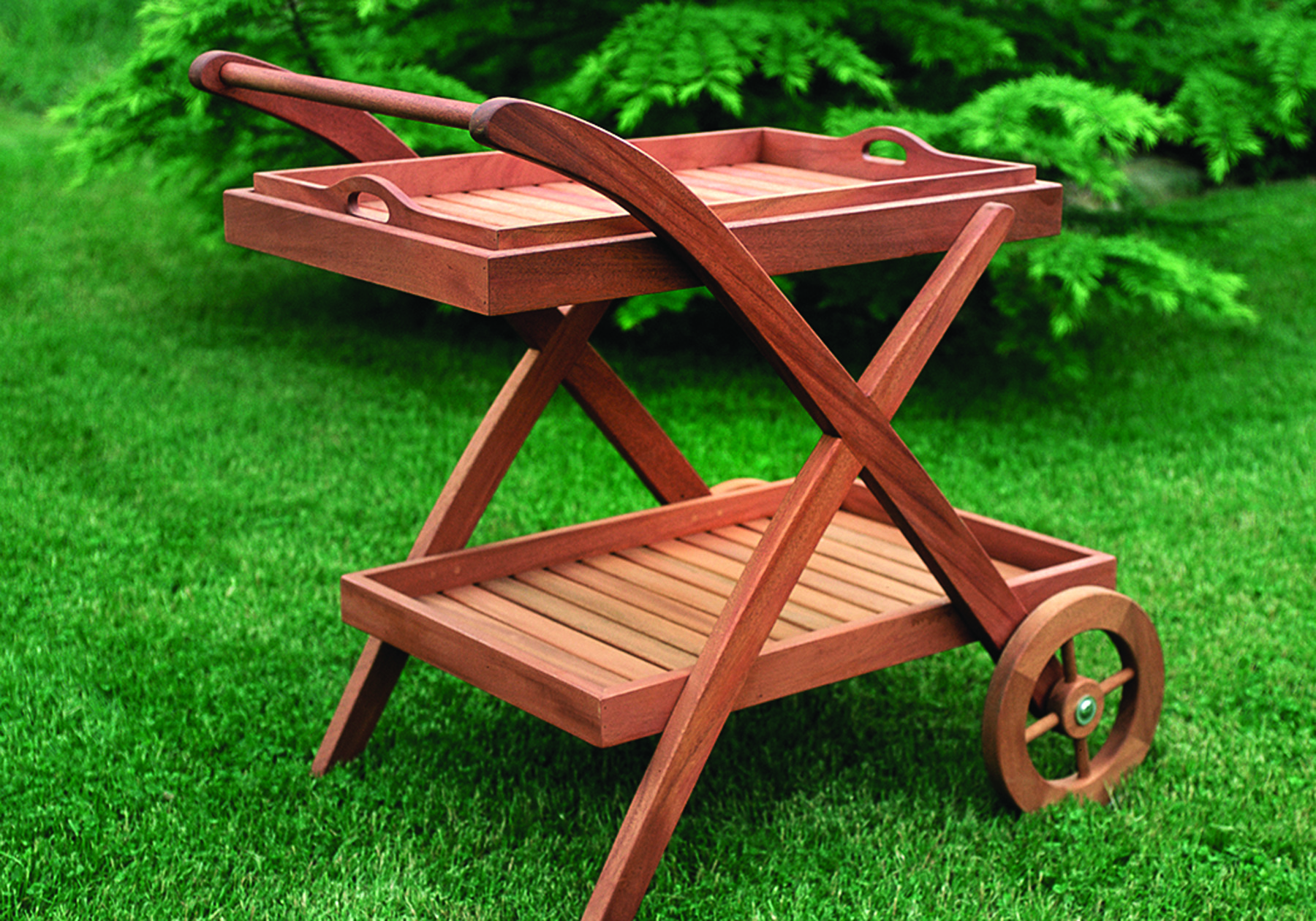
At your service. This serving trolley with a removable tray is one of many outdoor furniture projects Norm built over the run of the show.
Any idea about what was the most popular “New Yankee” project ever?
The comfortable, functional Adirondack chair was very, very popular. And any time we did shop furniture – and by that I mean something like a tool hutch or router table – it was a home run with viewers.
I think there are a few reasons for this: First, shop furniture is accessible, not complicated. Second, it’s more forgiving because it’s not as if it is going to be displayed in your living room. And third, shop furniture is a means to an end. Once you’ve built it, it’ll help you to move onto more refined projects.
After so many years in the shop, what do you hope to learn next? (Or, are there any woodworking skills that you’d still like to master?)
We never spent much time on “New Yankee” talking about finishing. That’s something I’d like to play around with. The wipe-on polyurethanes are great products, but there are so many other finishes out there.
I want to learn about more glazing and built-up finishes: layering and shellac.
Carving is a whole other skill set that I’d like to get good at.

The day job. Norm continues to be a part of “This Old House,” where he got his start 10 years before beginning “The New Yankee Workshop.”
What’s the best tip you ever learned from a fellow woodworker?
One of the most amazing techniques I learned was steam bending from Mike Dunbar (a Windsor chairmaker in Hampton, N.H.). He builds a steam box from PVC pipe and makes the steam using a propane burner to heat water in a 5-gallon can. When the steamed wood comes out of the pipe, you can bend it in very tight curves.
Imagine that a young kid comes to you and says, “I want to be a woodworker. What’s the first thing I should do?”
I get asked this question a lot. And it’s not just kids. People tell me they didn’t have the influence from a father or grandfather, or if they say, “I wish I’d paid attention to my father or grandfather when they wanted to teach me something. I don’t want my kids to make the same mistake.”
It’s really a shame that so few high schools, even vocational schools, no longer have shop programs. As I said before, there is only so much woodworking you can learn from magazines, the Internet and television. You have to get your hands into it.
I encourage people to find a local woodworking group or club. Some woodworking-supply stores hold classes where you can learn hands-on. And there may be a woodworking school in your area. You need to find people to connect to.
And there are a surprising number of woodturner groups that are always looking for new blood. That can be a good way to get a kid’s juices flowing. I also tell people that they have to be patient; these skills don’t come quickly. Too many kids don’t want to start at step one. There’s a reason it’s known as skill-building.
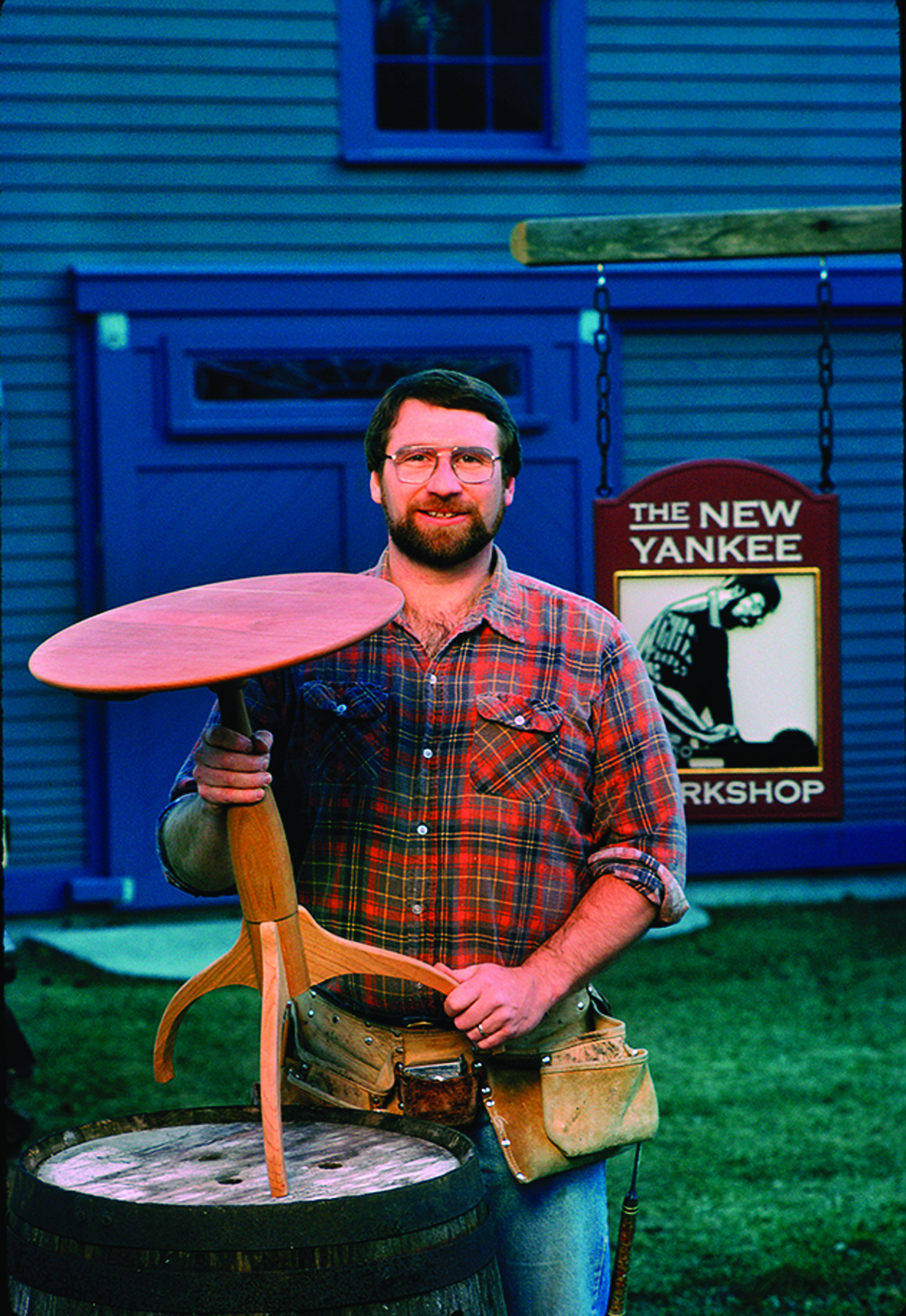
How it all began. “The New Yankee Workshop” was always project-oriented; on episode 110, in 1989, Norm showed viewers how to build this candle stand from Hancock Shaker Village in Massachusetts.
So, Norm, can you tell us what are you going to build next?
A shop. I still have access to “The New Yankee Workshop” building, but that won’t be forever. Elise and I recently bought an old house near the ocean, and there is no shop on the property. And it might surprise you, but I’m not going to build a wood-frame building. I’m going to build the walls out of ICFs (insulating concrete forms) and the roof from SIPs (structural insulated panels) because they are so energy efficient.
And then I want to build a sailboat – a Herreshoff sloop. I’ll probably go to a boat-building school to learn some skills first. There are quite a few in New England.
Video: In 2007, Norm Abram was interviewed by Popular Woodworking Magazine senior editor (then editor and publisher) Steve Shanesy.
Blog: Read this blog post about Norm’s decision to stop production of “The New Yankee Workshop.”
Here are some supplies and tools we find essential in our everyday work around the shop. We may receive a commission from sales referred by our links; however, we have carefully selected these products for their usefulness and quality.