We may receive a commission when you use our affiliate links. However, this does not impact our recommendations.
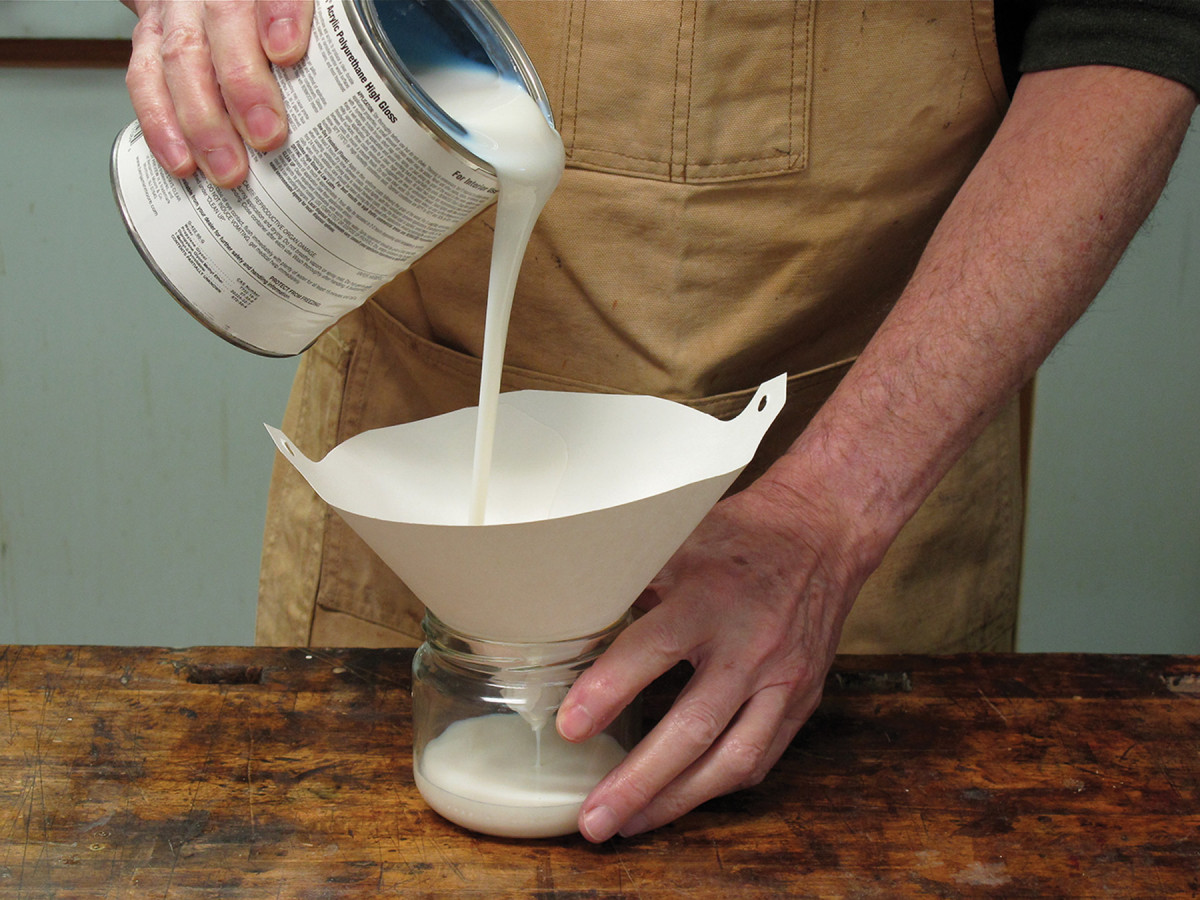
Straining. Though it’s always good practice to strain a finish before applying it, straining is doubly necessary with water-based finishes because there are usually coalesced particles in them that can mess up your finish. That isn’t the case with true lacquer.
The two products – both useful – are quite different.
Dating back at least 100 years, the term “lacquer” has referred to a non-crosslinking finish that thins with lacquer thinner. The most common type is nitrocellulose lacquer.
In the late 1980s water-based (or waterborne) finishes became available and some were labeled “lacquer.” The reason, as one manufacturer confided at the time, was to make woodworkers think they were using a familiar finish, one that would apply and perform like the traditional lacquer they were used to. This might make them more likely to try it.
To justify the name, manufacturers claimed that their water-based finish “burned in” like traditional lacquer. That is, each freshly applied coat dissolved into the previous coat, creating in effect one thicker coat. So the example of equivalency was burning in.
To some degree this is true. Water-based finishes do bond fairly well to previous coats, but the similarities pretty well end there. In virtually every other important quality, the two finishes are very different and should have different names to avoid confusion. Manufacturers, writers and teachers should stop referring to water-based finishes as lacquer, or water-based lacquer.
Water
The biggest difference, of course, is that water-based finishes contain a lot of water and lacquer doesn’t. Consider these consequences of water.
■ Water raises the grain of wood. To get a smooth final result you have to sand the raised grain level and do so without sanding through to the wood or a stain. Though you should also sand the first coat of lacquer or lacquer sanding sealer, it is much easier than sanding the raised grain caused by water.
■ Water-based finish is much more sensitive to temperature and humidity than lacquer. There’s not much you can do to control the drying rate of water-based finish other than control the temperature and humidity in your shop, which can be expensive. In contrast, the drying rate of lacquer can be controlled by adding lacquer retarder in hot or humid conditions and acetone in cold conditions.
■ Even in moderate temperatures and low humidity, water evaporates more slowly than lacquer thinner, increasing the risk of runs and sags. Moreover, most lacquer thinners contain six or more solvents that evaporate at different rates, further reducing the likelihood of runs and sags.
■ Water-based finishes often contain coalesced particles that can mess up your finish; that isn’t the case with lacquer. So it’s doubly important to strain water-based finishes before using.
While these characteristics can be seen as negatives, water contributes one very important positive quality: lower odor. Water-based finishes are far less smelly and irritating to apply than lacquer.
Resin
A second important difference is the resin used.

Different resins. Lacquer is composed of long stringy nitrocellulose molecules that pack together when the solvent evaporates.
Lacquer is composed of long stringy molecules of nitrocellulose that entangle in liquid form (like stirred spaghetti in a pot of water) and form a hard film after all the solvent evaporates. This film can easily be returned to liquid form by bringing it into contact with lacquer thinner.
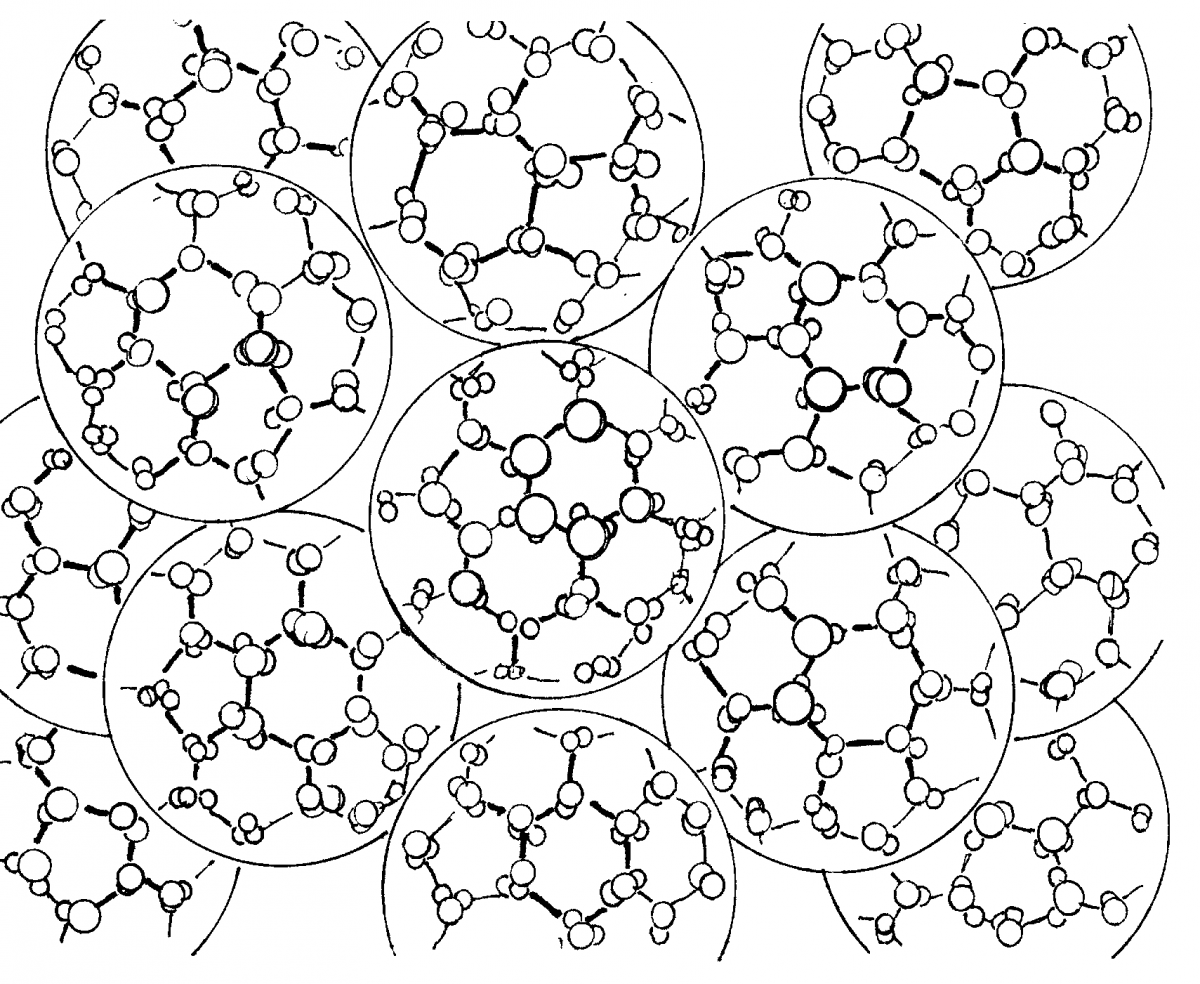
Water-based finish is composed of emulsified droplets of crosslinked acrylic and polyurethane resins that stick to each other when the water, then the solvent, evaporates.
In contrast, water-based finishes are composed of emulsified droplets of acrylic or polyurethane resin that come together and stick to each other when the water (which evaporates first), then a solvent evaporate. Inside the droplets, the resin molecules crosslink – that is, form chemical bonds – but with few exceptions the droplets themselves just stick to each other. They can be separated with several solvents, but with more difficulty than with lacquer.
The different resins and the way they cure account for significant differences in the way the two finishes can be manipulated.
■ Lacquer can be repaired invisibly by melting (with heat) or dissolving (with solvent) more lacquer into the damage. Because of the crosslinking within the water-based droplets, however, there’s usually a visible boundary with water-based finishes. This boundary has to be disguised with color, often a difficult task.
■ Lacquer is easier to rub to an even sheen because the spaghetti-like molecules are easily separated with an abrasive, while the crosslinked molecules within the water-based droplets resist separation. They have to be torn apart, creating a more uneven sheen.
■ Also because of the crosslinking, water-based finishes are more difficult to strip. Lacquer can simply be dissolved and wiped off with lacquer thinner or paint stripper.
■ Water-based finishes are also more difficult to clean from a spray gun. You usually have to disassemble it to remove all the finish. In contrast, lacquer can be left in a spray gun for a week or longer and still be totally cleaned when more lacquer, or lacquer thinner, is sprayed through it.
Though the crosslinking within the droplets can be seen as a problem for manipulating water-based finishes, it’s an advantage for better abrasion resistance and even some solvent and heat resistance. This is due to the entire surface area being composed of crosslinked molecules except where the droplets stick together.
Decoration
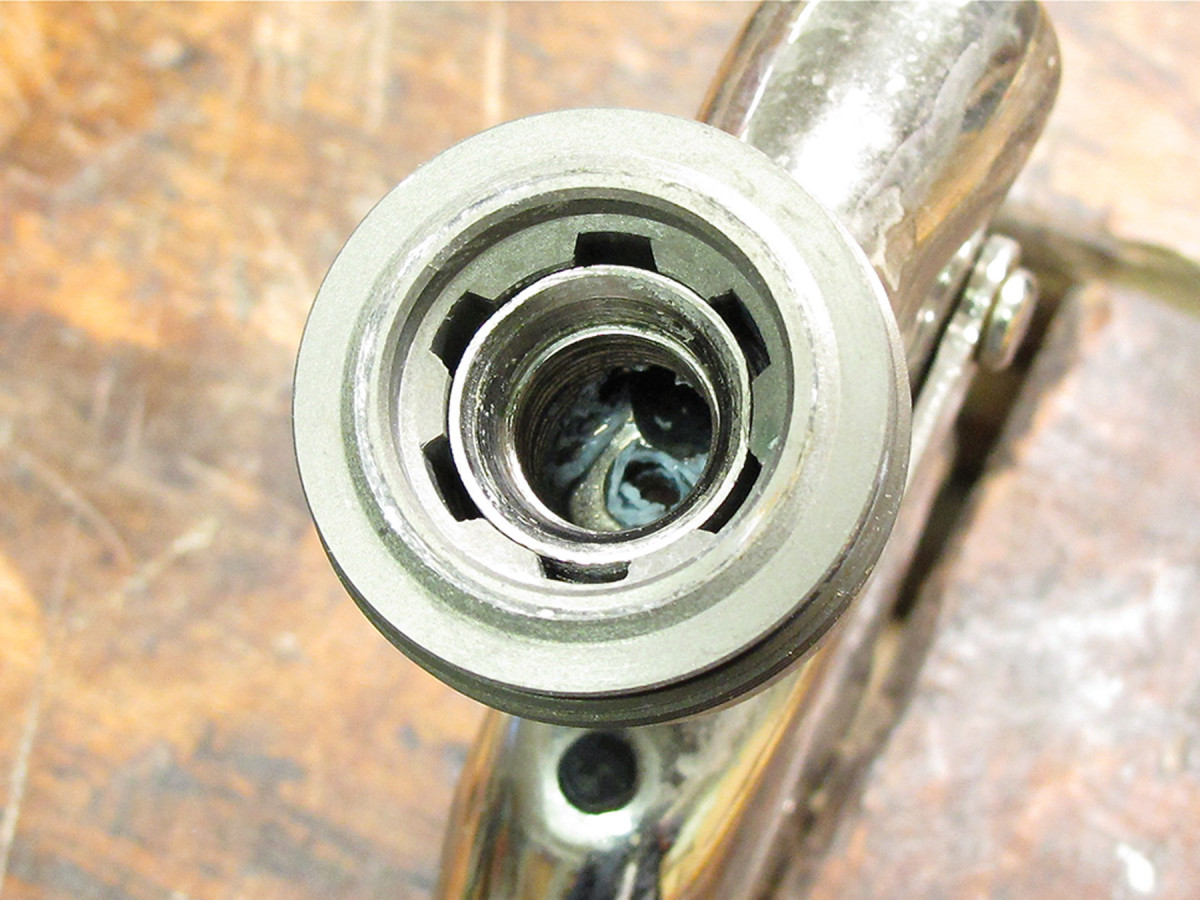
Cleaning spray guns. Cleaning is more difficult with water-based finishes than with lacquer. Usually you have to disassemble the gun and scrub the parts with a brush. To show this, I ran hot soapy water through the gun for several minutes, but white clumps of finish remain that will dry and disrupt the spray pattern.
Coloring and filling steps are more difficult with water-based finishes than with lacquer. For example, lacquer can be thinned infinitely with lacquer thinner to make toners while water-based finish cannot. Adding too much high-surface-tension water causes water-based finishes to bead up.
Also, because of lacquer’s ability (due to the lacquer thinner) to penetrate through layers of color (stain, glaze, pore filler) and bond to washcoats or full coats of finish underneath, it’s possible to build a multi-color-step finish that has considerably more film integrity (resistance to separation at the color layers) than can be achieved with water-based finish.
As a result, factories often do their decorative steps with a solvent finish, then topcoat with water-based finish to comply with VOC laws.
Color
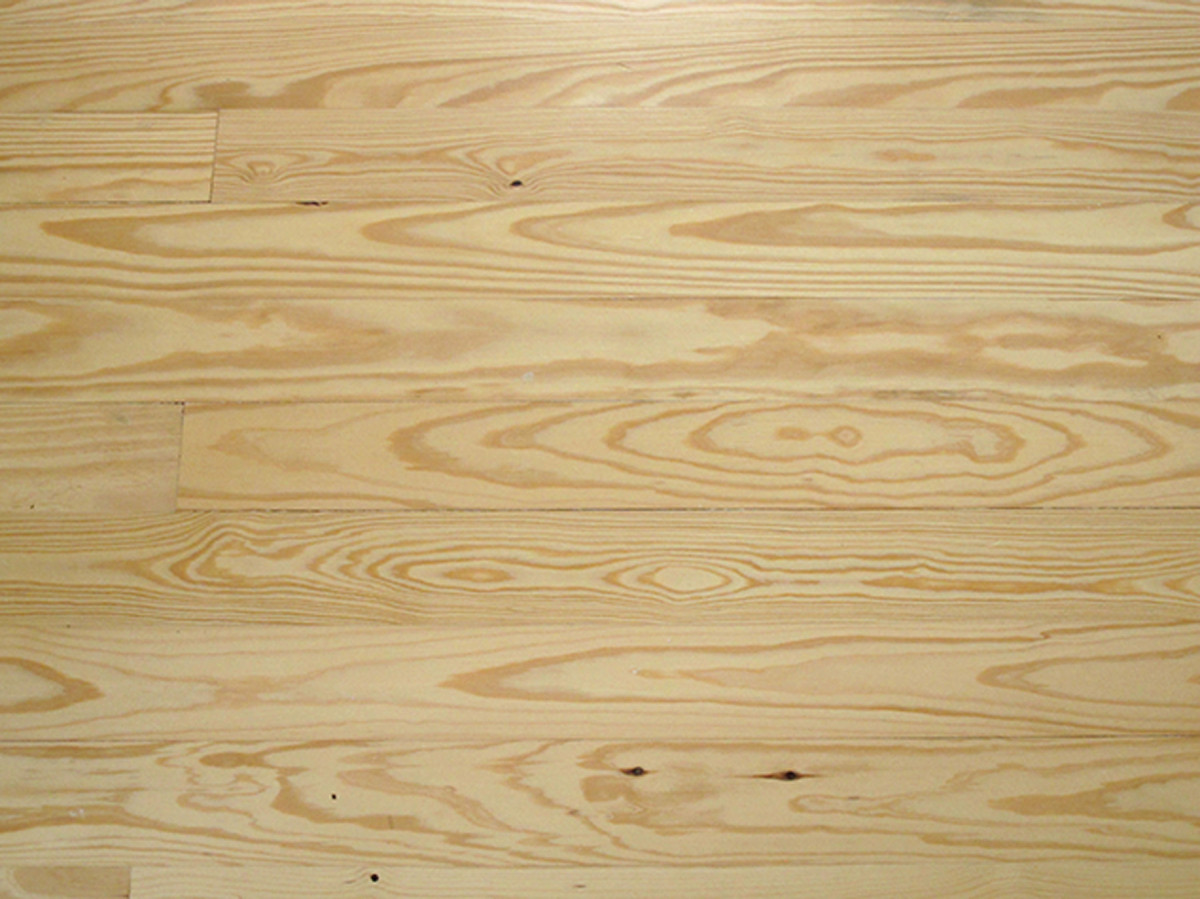
No color. Most water-based finishes add no color to the wood. I find this quality to be very attractive on “white” woods such as maple, birch and ash, and on this pine floor. Lacquer adds an orange coloring to the wood.
Finally, one of the most significant differences is color, or lack of it, the finish adds to the wood. Lacquer adds a warm orange coloring while most water-based finishes add no color.
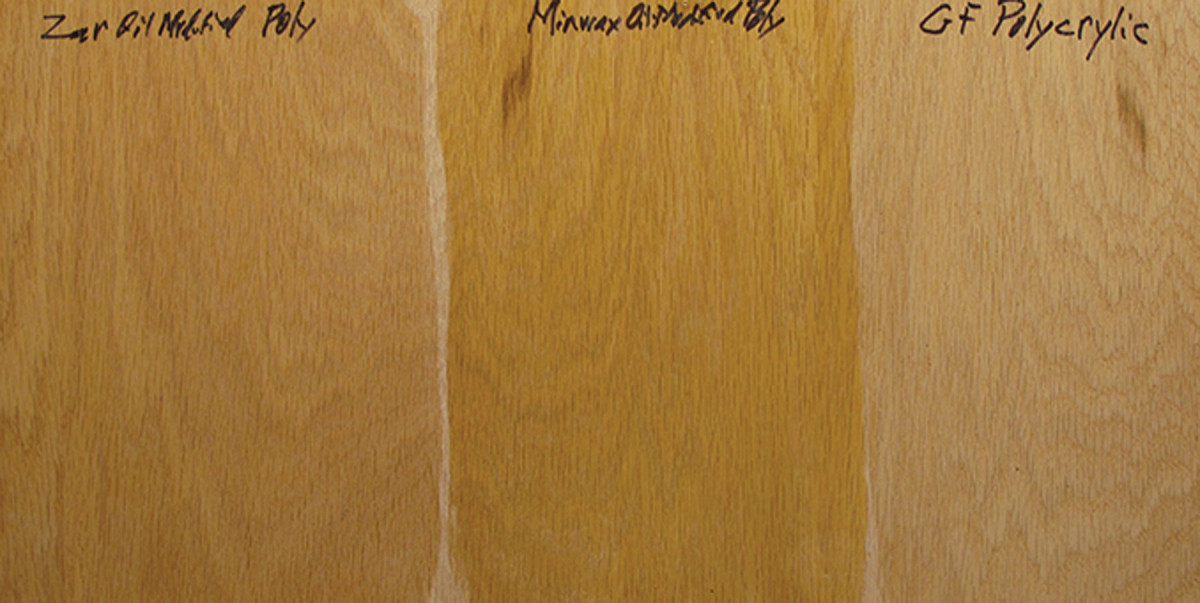
Different colors. Not all water-based finishes are completely colorless. As you can see on this oak, while the General Finishes acrylic water-based finish (right) adds no color, the two oil-modified examples, Zar (center) and Minwax, do add some color. If color is important to you, test first on scrap wood.
The orange coloring warms darker woods such as walnut, cherry and mahogany in contrast to water-based finishes, which deaden the color (unless you apply a stain). On the other hand, most water-based finishes maintain the white coloring of woods such as maple, birch, ash and pine, which I find attractive.
I hope I’ve made the case that water-based finish is very different from lacquer and shouldn’t be called lacquer. PWM
Bob is a contributing editor to this magazine, and author of “Flexner on Finishing,” “Wood Finishing 101” and “Understanding Wood Finishing.”
Here are some supplies and tools we find essential in our everyday work around the shop. We may receive a commission from sales referred by our links; however, we have carefully selected these products for their usefulness and quality.