We may receive a commission when you use our affiliate links. However, this does not impact our recommendations.
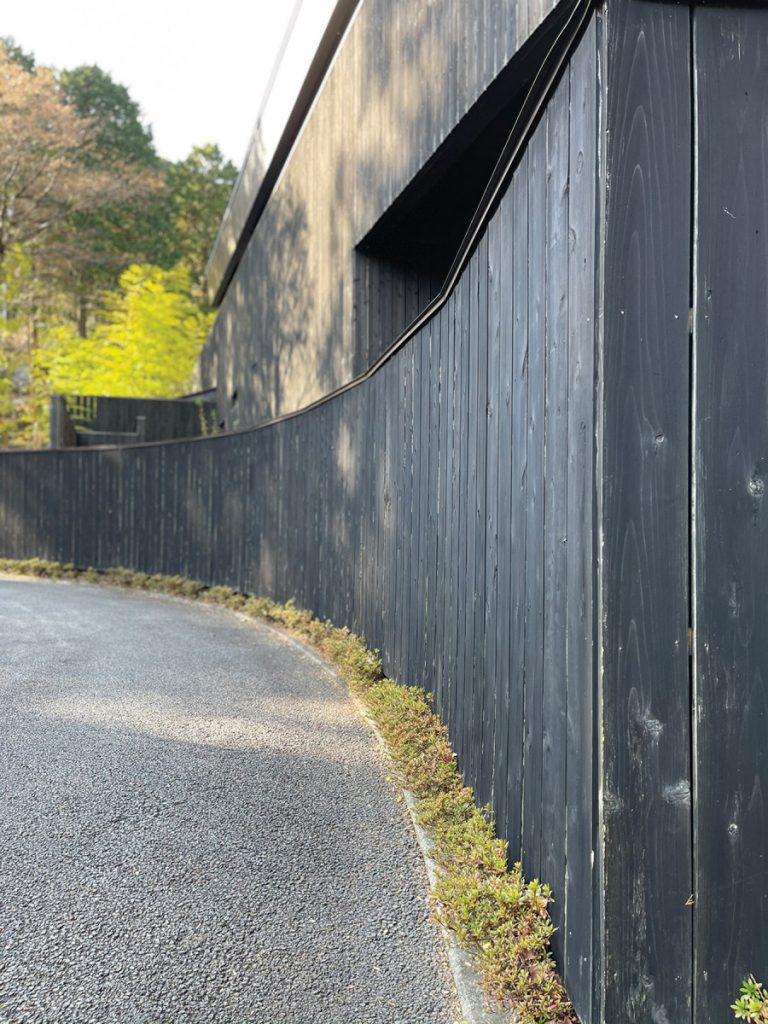
This yakisugi covers an upscale hotel in the mountains of Kanagawa Prefecture.
It isn’t called shou sugi ban, nor is every charred workpiece in a project called yakisugi. It’s simply a charred finish with its origins in Japan.
An important lesson I learned during my five-year military enlistment was the concept of always leaving something better than it was. My unit would ensure a range used during a field operation was cleaner than it was before we came. When required to check out a vehicle as a command driver, upon return, it was cleaned and topped back up with fuel. Borrowing any gear from a fellow Marine or the local supply was always returned pristine and organized, regardless of the state of receipt. This principle remained with me, even after I transitioned out of the military.
As artisans, our development involves borrowing concepts and techniques from those who came before us. The hope is that, beyond making quality bespoke products, through our training and guidance, access to information about our craft will increase. In turn, this will help preserve knowledge for future woodworkers. This dedication should be extended to all forms and techniques, especially when borrowed from other cultures, and more so with those that become a trend.
Origins of Words: Shou Sugi Ban
Several years ago, I was introduced to something called the “shou sugi ban” technique via social media. Touted as a Japanese finishing technique, it simply involved charring wood with fire. It seemed deceptively simple. Proponents of shou sugi ban purported its ability to protect wood, yet gave no information as to the mechanism of how the protection occurred. Living in Japan, I chose to invest some of my time to learn about it. Yet, after significant research locally and on the internet, I learned that everything being taught to approach this technique was misguided. Even the name being used for the trending hashtag is inaccurate. Shou sugi ban, as it is known in the west, is an incorrect misreading of the Japanese kanji used to form the word.
In Japanese, there are four total writing systems if you count Romaji, which is the Romanic alphabet used to assist non-Japanese readers with spelling and pronunciation. The other three are hiragana, katakana, and the most daunting, Kanji.
Why is Kanji daunting? Kanji are characters that were adopted by Japan from China. They are logographic symbols that represent a concept or object. Kanji characters are written strokes. The shortest being one stroke (一 which means one) to 25 or more strokes. A proficient reader knows around 2100 Kanji.
Each Kanji can have multiple ways to be read. For the example of one (一), it can be read as ichi, itsu, or hito. The first two are called the on-yomi reading and this pronunciation derived from Chinese reading. The second is kun-yomi and these are Japanese-language-derived specific readings.
Shou sugi ban is an incorrect reading of the word 焼杉板 or, in Romaji, yakisugita. The first (焼) encompasses the concept of burning or heating up. It is read as either shou or yaku. The last kanji (板) means board or plank. It can be read as ita, ban, or han. Since yakisugi is a vernacular construction technique derived in Japan, it carries the kun-yomi reading. The tangible board is called yakisugita. The technique is called yakisugi. It has unfortunately trended under an incorrect name for many years.
Only Cedar for Yakisugi
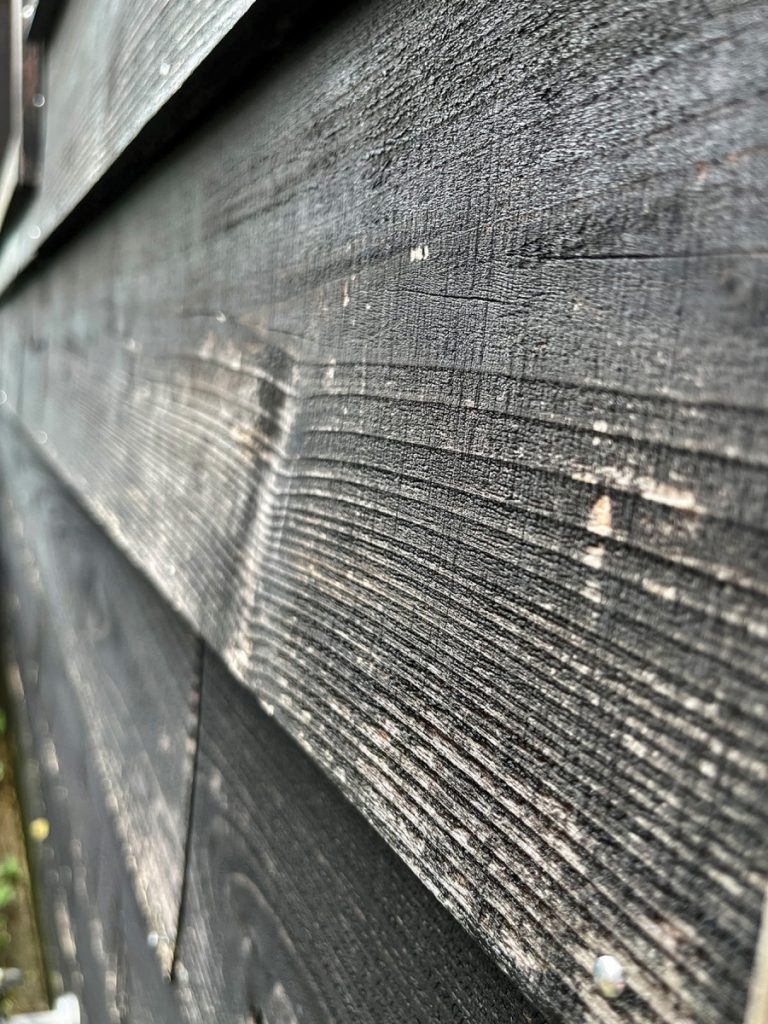
Through years of exposure to the natural elements, the dramatic textures are presented while still providing ample protection.
Another unfortunate aspect of this technique lost with the trend is found in the translation of the middle Kanji—sugi (杉). Sugi means cedar; specifically a species called Cryptomeria japonica, the national tree of Japan. This means that yakisugi can only be correctly done on cedar. Charring other species besides sugi invalidates the use of the word “yakisugi.”
Sugi is a popular species for siding in Japan. With a long rainy season in the middle of the year, Japan has relatively high humidity between April and November, depending on latitude. Bugs can also be overwhelming during their active months. This has varying negative effects to homeowners like rot, mold, and infestation. Among the native tree species in Japan, sugi has the best properties for rot resistance from bugs and moisture.
Prior to experimentation with burning, carpenters would harvest sugi trees that were close to ocean water. Salt penetrating the fibers of the tree would increase the rot resistance properties. Due to high demand, salt-penetrated sugi became unsustainable. Carpenters discovered that burning the faces of the siding achieved similar rot resistance protection.
Though slightly counterintuitive, setting fire to the outer layer of wood also provides a level of fire protection as well. Once the wood has already been charred, it does not combust as easily. With 2-3 millimeters of burn, the structural support of the wood remains, but the external layer of carbon provides fire resistance. This is a desirable protection for those living in the countryside who do not have quick access to fire emergency services.
Yakisugi Examples in Japan
Yakisugi siding is common in rural areas of Japan. This house, close to my own, was built prior to World War II. The current resident’s father purchased the house after the end of the war for his family. Though the house was not originally covered in yakisugi, it was added approximately 25 years ago.
The current resident, the original owner’s daughter, has lived in the house for over 70 years. She is pleased with the yakisugi face that covers the house. Along with the beautiful texture of the burnt cedar boards, no maintenance has been required since hanging the siding.
How does it work?
Sugi planks are laid out and ready to be lashed together.
Burning like this could be easily achieved close to the building site and directly hung once burned without further treatment. To achieve consistent and quick charring, triangular prisms of sugi would be laced together with string. Tinder was then stuffed into the center of the prism, lit on fire, and placed upright to form a smokestack. Once flames poured out of the top, it was brought down, unlaced, doused in water, and hung as siding. Done like this, it would last decades with no further intervention. This Yakisugi cladding requires little maintenance, and when it does it can be quickly completed by either burning a new layer or simply replacing worn out stretches of cladding.

With ropes, a prism is made and the center cavity is filled with tinder.
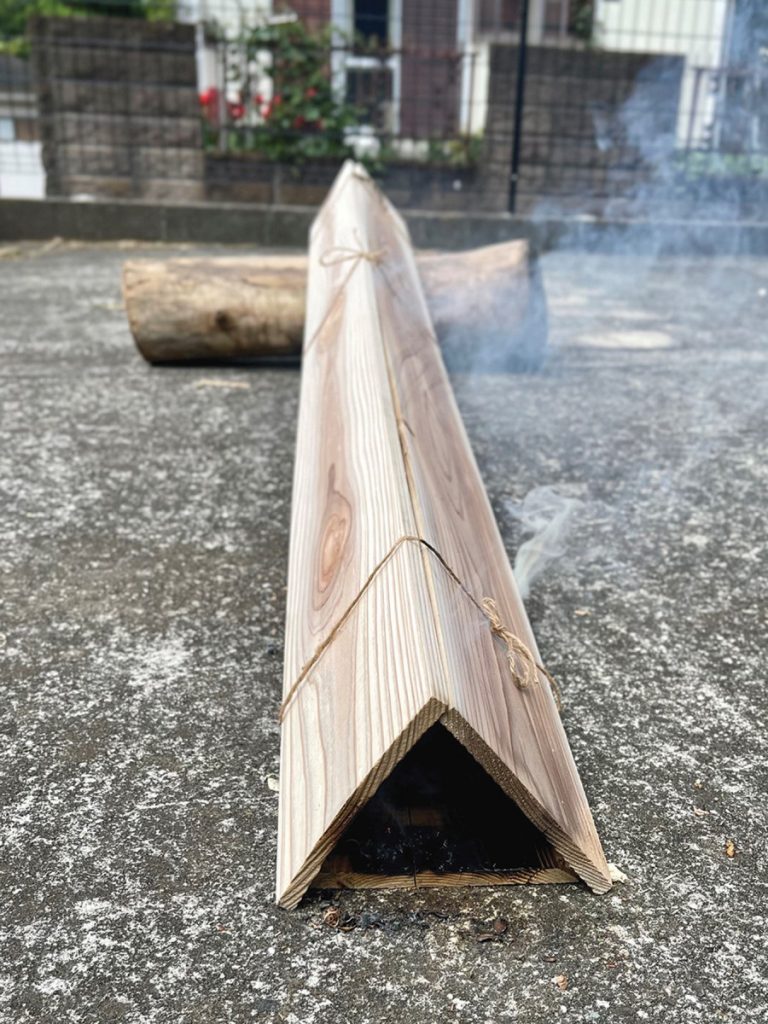
The fire is lit from the bottom and the stack is engulfed in flames.
In modern yakisugi manufacturing, automated machines achieve burning the planks of sugi in batches. With easier access to oil-based finishes and hardeners, once boards are burned, coats of these finishes may also be applied to add even more protection. It is still a vernacular construction technique used in the countryside for farmhouses and storerooms, but it has made a resurgence in living spaces and office buildings.
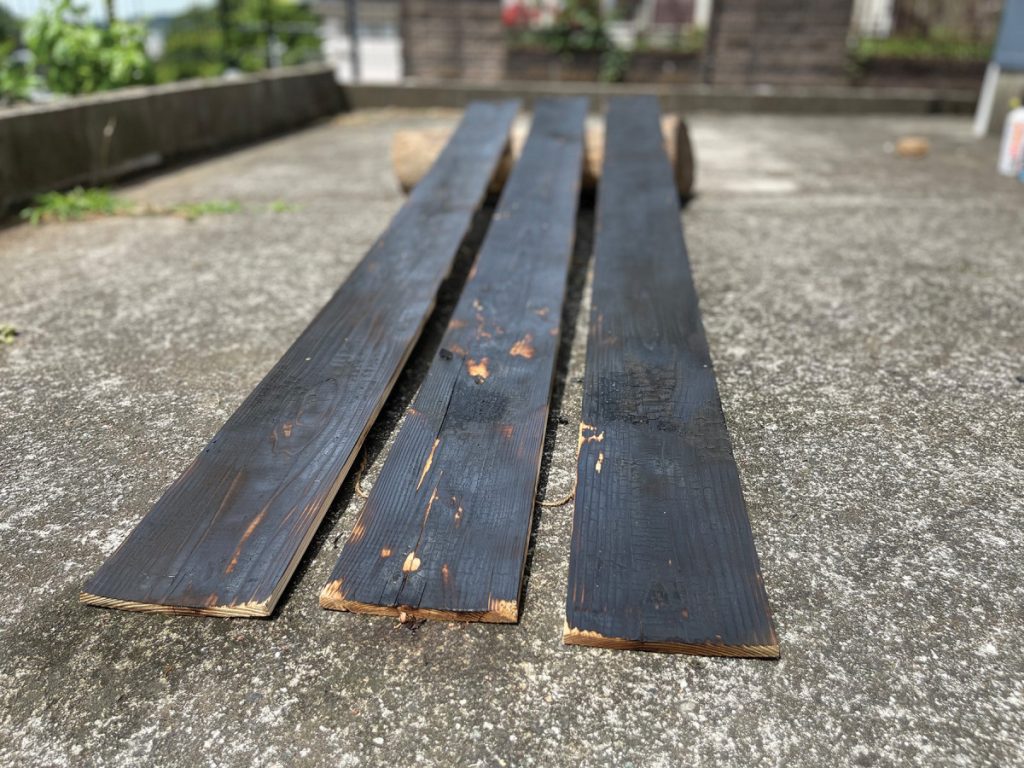
After burning for several minutes, the ropes are cut and planks doused in water.
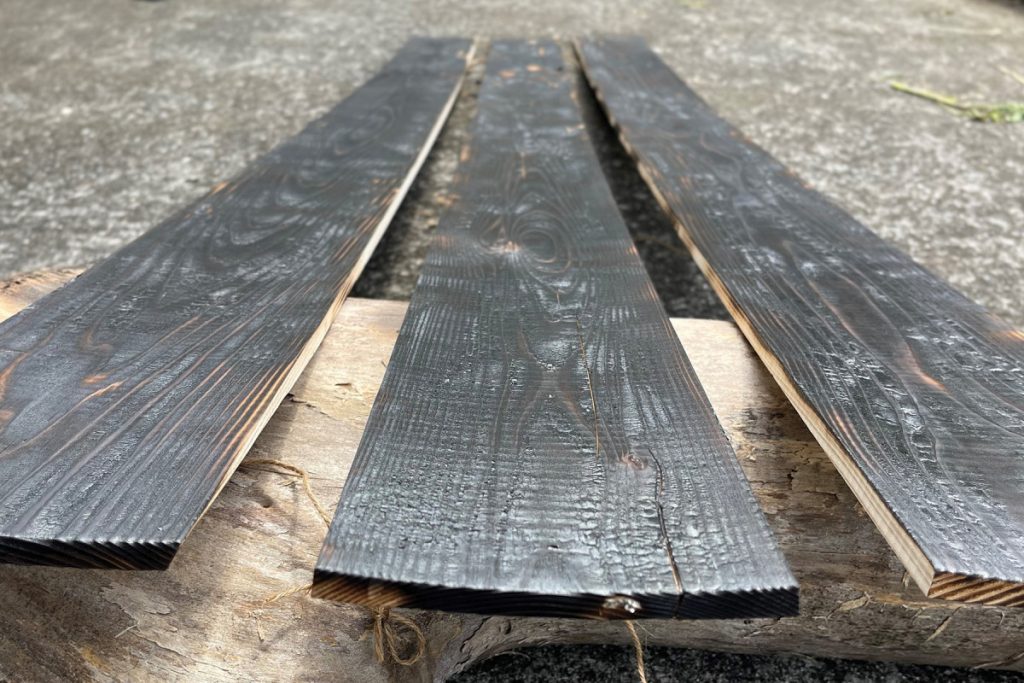
For a deep burn, this method can be dangerous without taking safety precautions.
You do not need an industrial machine or a prism structure to experiment with the yakisugi technique at home. A simple propane or MAPP gas torch will work. True yakisugi requires Japanese cedar but similar results can be obtained on other cedar species. Different increments of burning along the grain provide different textures. The charred layer needs to be able 2-3mm deep for adequate levels of protection. Once completed, no wire-brushing is necessary. An oil finish can be applied but is also unnecessary.
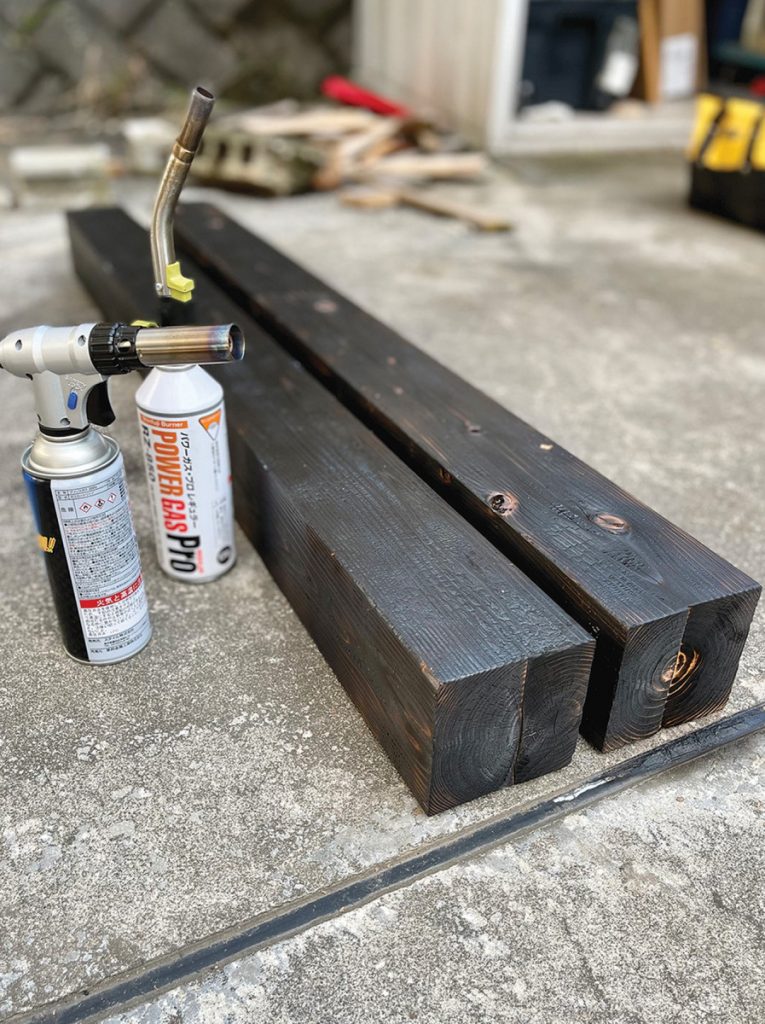
Alternatively, simple propane torches can be used to create a consistent burn.
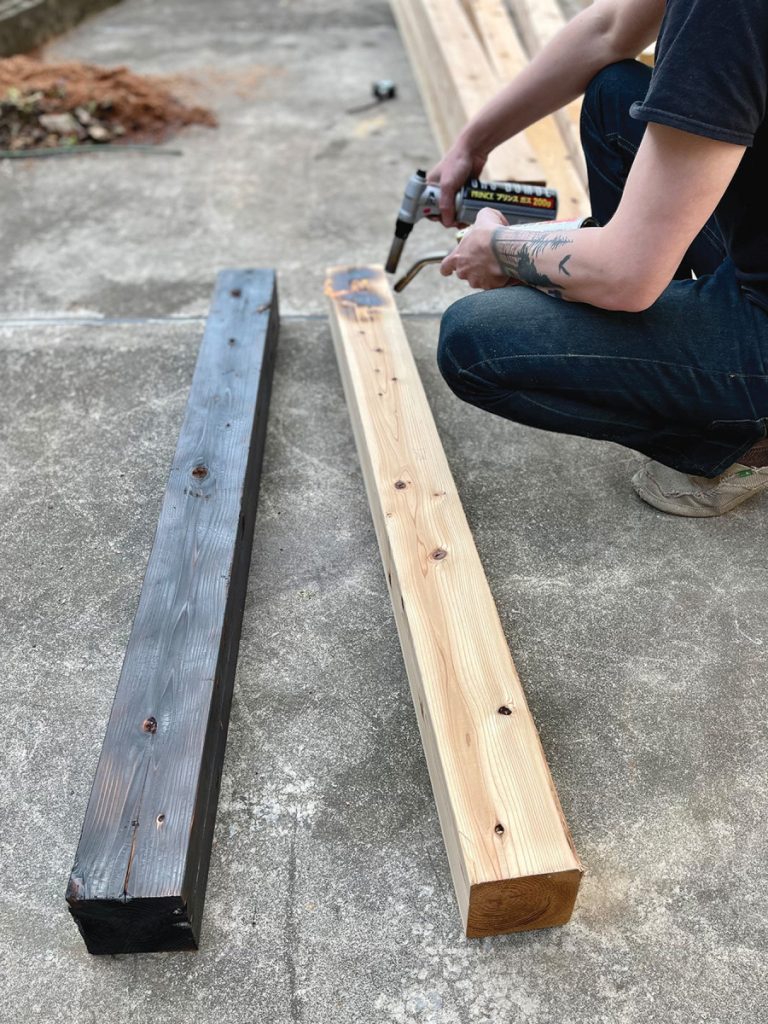
This method requires more time but allows for more control and is slightly safer.
More important than experimenting with and implementing yakisugi, we should understand its history. The hope is that we, the community of woodworkers, will leave the collective knowledge of woodworking techniques better off than what we received. The start of this goal is to appreciate, respect, and correctly use those techniques, including the name of the techniques themselves.
In the realm of those techniques is yakisugi; it is not called shou sugi ban, nor is every charred workpiece in a project called yakisugi, the name being reserved for a specific species. As an alternative, one can call it a charred finish or a carbon layer. Please join me and a growing number of woodworkers in correcting this inaccurate terminology. Help us leave woodworkers of tomorrow accurate and more robust knowledge than what we received—knowledge that will last longer than yakisugi siding, hung beautifully on the side of a country farmhouse in rural Japan.
Here are some supplies and tools we find essential in our everyday work around the shop. We may receive a commission from sales referred by our links; however, we have carefully selected these products for their usefulness and quality.
Very thankful for this article. Having made attempts at shou sugi ban in the past I always felt everything about what I was attempting was not true or correct. And know I know why. Because I was misinformed. Maybe someday I can actually create yakisugi until then I can confidently practice the carbon layer technique. Thanks again.
Great article by a woodworker, writer, historian and linguist all in one. It’s not that builders shouldn’t burn other woods (pine can look awesome), but you’ve done a lot to clear up the origins of the technique and the correct usage of the words.
Great article, very informative 🙂
Shou-Sugi-Ban is actually the trade name of a company in the UK who supply charred timber cladding. I guess the company name was marketed well and happened to be in the right place at the right time so became popular (plus it sounds good?!) and has been misused on social media ever since!