We may receive a commission when you use our affiliate links. However, this does not impact our recommendations.
One of most fun aspects of furniture is not necessarily found in the shop. Yes, making wood dust and building furniture is a blast – that’s why we do it. But discovering something that is not easily explained is fun, too.
The week immediately after labor day – that would be beginning Tuesday September 3rd – I have a class scheduled at the Connecticut Valley School of Woodworking (CVSW). During that week long class, the project is an early, transitional lowboy that straddles both the William & Mary and Queen Anne periods. (It’s the piece shown above.)
I’ve written a few posts about this lowboy on my personal site, woodworkersedge.com, if you’re looking for more information. One recent post discusses how easy it is to build this piece. There are a couple of openings for the class if you want to join us. Contact Bob Van Dyke at CVSW to register.
So here is the not-easy-to-explain discovery. The dovetailed drawers on this early piece of Queen Anne furniture have tapered sides, as seen in the right-hand photo. Tapered sides in drawers are not new to me, or to you for that matter if you’re a regular reader of Popular Woodworking Magazine.
In the June 2012 issue (#197), we published an article on how to build a Shaker Counter that was originally built by Grove Wright. It is on Shaker furniture that I have seen this drawer characteristic. Each time I’ve seen this interesting and more-challenging-to-complete technique, it has been on a piece of furniture built by or in association with Grove Wright. Here it is now on a piece that is not associated with Wright, and not even a Shaker design – the lowboy is far too decorative to be found anywhere near (relatively speaking) a Shaker community.
Grove Wright, according to the book “Shaker Design,” by June Spriggs, was born in 1789 in Pittsfield, Mass. and was raised in the Tyringham Shaker community. I don’t have a date on the lowboy, but I do know it’s a Connecticut piece and the design would date the piece to around the first quarter of the 18th century, some 60 years before Wright’s birth.
Did Wright see this drawer technique as he traveled the Northeast? Did a family member outside the Shaker community own the lowboy at one time? Is it possible that the craftsman of the lowboy joined the Shakers and taught tapered sides to young Master Wright? Or was this technique an accepted method that, for some unexplained reason, we don’t see often? These are the mysteries of reproduction furniture.
If you’re interested in building this lowboy, sign up at CVSW and join us for the week – nothing is better than having to spend a week doing nothing but woodworking. Another option is to take off and build this piece on your own, working up the drawings and working out the details. Or, you can sit patiently for a few months until we publish the article in Popular Woodworking Magazine. In that article, I’ll have step x step instructions and complete drawings. I may even have the answer as to why tapered drawer sides show up on the lowboy and in the work of one of the most recognized Shaker craftsman.
Don’t hold your breath on that last one.
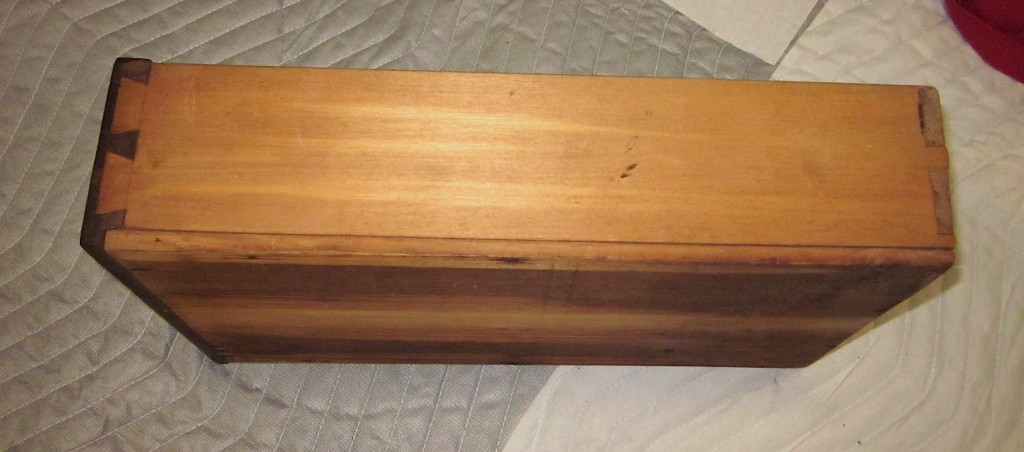
Here you can see the drawer side. It does appear to be riven or at least quartersawn. Also, as pointed out by an astute reader, the side/back dovetails are reverse of what we consider optimal. It also appears as though the taper of the drawer back is upside down. Questions.
You can get more information on Shaker furniture in “The Complete Shaker Collection” by the Editors of Popular Woodworking, or in the complete updated and improved classic by Thomas Moser, “How to Build Shaker Furniture.”
If you want to build an easy Queen Anne Dressing Table (also known as a lowboy), download my article from the June 2010 issue (#183).
Here are some supplies and tools we find essential in our everyday work around the shop. We may receive a commission from sales referred by our links; however, we have carefully selected these products for their usefulness and quality.
I’m no expert, but the inside tapering of the drawer reminds me of a serving tray. Perhaps the reason for doing the extra work was to create a special feature to distinguish Grove’s work from others in a competitive environment. It’s also similar to why we might under bevel a table edge, to make the table look lighter and more refined. Opening the drawer would display the thin upper edge, making the drawer appear more delicate and refined. Once you’ve mastered regular dovetailed drawers, is the extra work to bevel them such an added time sink that it would be economically unfeasible? Not sure, but I do love a good mystery. Thanks, Glen.
I thought the reason for the tapered sides was so the face of the drawer could have a closer tolerance and look better closed, yet if the whole drawer had that small of margin of clearance it could easily swell shut and not be able to open it.,
Am I correctly interpreting the photos and the sides have pins while the ends have tails? If so how common is that?
My cousin, who used to be an antiques dealer, once told me he had seen a number of 18th-century pieces from Maryland with tapered drawer sides.
Another possible explanation for the tapered sides is the thicker bottom provides more space for a groove for the bottom while the thinner top looks more refined when the drawer is open.
Maybe not so difficult to explain. Were the drawer sides riven with the bark side to the bottom of the drawer? Riven stock would naturally be tapered like this.