We may receive a commission when you use our affiliate links. However, this does not impact our recommendations.
Most magazine articles about jigs miss the point entirely. Jigs exist to make work easier, safer and more accurate. They shouldn’t be complicated projects in and of themselves – they should be something simple you can put together quickly so you can get on with your work.
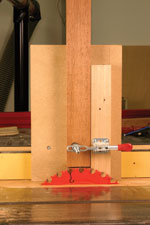
Start low and move up. Set the height of the saw blade to the shoulder line by sighting from the edge of the table. Make sure that one tooth is at top dead center, and make your initial setting slightly lower than you think you should. It will be easier to move up after a test cut than it would be to move down.
We admit to falling into this trap ourselves in the magazine’s shop. The corners of our shop are home to jigs that were built for articles about jigs. We can’t throw them out because the amount of hardware and time that went into making them has us convinced that they’re valuable. The problem is, we almost never use them. They’re too big, heavy and complicated to bother with.
Instead, we use a handful of truly useful jigs that we’ve put together quickly to meet a need. This new column is all about this kind of jig. We’ve made some promises to ourselves about the kind of jigs we’re going to present. For starters, we’re going to keep it simple. Most of the jigs we really like only do one thing, but they do it very well.
And we’re going to focus as much on how to use the jigs as on how to make them. You won’t see a cutting and hardware list that takes up more than a line or two, and we’ll let you decide whether to get a sheet of Baltic-birch plywood or use whatever you have.
We will show you sound principles and simple techniques that we have used over and over again. If your hobby is making jigs, you may be disappointed; if you want to work smarter, we think you’ll be pleased.
This jig enables you to safely make a cut on the table saw with the workpiece held vertically as it moves over the blade. I’ve seen this done freehand on television and it always makes me cringe. The chances of the piece catching and kicking back are too big to risk.

Start wide and move in. When you’re satisfied with your height setting, set the fence. A zero-clearance insert on the saw will make it easier to set the blade to your layout line.
Smooth Moves Make Tight Joints
The key element in making this jig is to get it to slide nicely along your table saw’s rip fence. It needs to be free to move, but not sloppy. This depends on the width of the horizontal piece that goes on top of the fence, between the two vertical pieces. If you screw the pieces together without gluing them, you’ll be able to make some trial runs and get it just right.
Changing the width of the horizontal piece changes the fit, so if you’re not sure of the exact width you need, start big and trim a little off at a time. Trial and error is a good process, but it’s wise to structure it so that an error doesn’t ruin the part.
I made this jig from 3/4″-thick MDF, but it could just as easily have been made from a decent piece of plywood. Stay with the 3/4″ thickness so there will be room to drive screws without splitting the wood.
After getting the width of the horizontal piece right, put glue on the two long edges, set it on top of the fence, then put the vertical pieces in position on either side. Use clamps to hold things in position and drill countersunk holes for #8 x 1 1/2″ screws. The large vertical piece is 3/4″ x 8″ x 12″, but this can be varied to suit your needs. The smaller vertical piece that captures the jig on the fence is wide enough to reach from the top of the saw table to the top of the horizontal piece.
Get on the Fence
When the screws are in place, remove the parts from the saw fence and clean up any excess glue on the fence, or the inside of the jig. After the glue has dried, rub some paraffin on the inside to help it slide smoothly.
The fence can be made from any hardwood. I used a 1 1/4″-thick by 1 3/4″-wide scrap of cherry. These dimensions are also arbitrary, but this size works well to mount and use the clamp on material between 3/4″ and 1 1/4″ thick. It was 12″ long originally, but the bottom became ragged from use, so I cut the end off and remounted it. No glue is used to hold the fence on, only screws so it can be replaced as needed.
Locate the clamp above the highest position of the saw blade, and screw it in place. Adjust the arm on the clamp to firmly hold the material. Add a handle to the jig to make it easier to push.
The advantage to a jig like this is that once it is set up, you can quickly make a bunch of identical tenons. Layout work and fussing is minimized by making a few extra pieces for test fitting. Setting up the cuts is an easy, two-step process.
Cut the tenon shoulders first, then clamp a part in the jig and move the fence next to the blade. A rip blade will make easier cuts than a combination blade, but either will work. Raise the blade until it is just below the shoulder line.
Setting the width is next; a zero-clearance insert on the saw makes this easier as well as safer in use. Slide the fence over until your layout line is on the edge of the kerf in the insert. Set up so that the scrap falls to the left. Make a test cut and examine the result.
If the blade is too low, there will be a ridge of material left between the cheek and shoulder of the tenon. If the blade is high, it will show as a nick in the shoulder line. With most saws the blade is likely to drop from backlash in the mechanism if you lower the blade. Starting with the blade low allows you to raise the blade a tiny bit at a time.
Adjustments in the thickness of the tenon are made by adjusting the rip fence. Start outside the layout line and make a cut on both cheeks. Measure the mortise with a pair of calipers, and check the thickness of the tenon with the outside jaws. When you think you’re close, check the fit of your test tenon in a mortise and tweak as necessary. Make a final test cut in a new piece of stock. If you’re just shaving a bit off, the blade can deflect, affecting the size of the tenon. PW
Click here to download the PDF for this article.
Here are some supplies and tools we find essential in our everyday work around the shop. We may receive a commission from sales referred by our links; however, we have carefully selected these products for their usefulness and quality.