We may receive a commission when you use our affiliate links. However, this does not impact our recommendations.
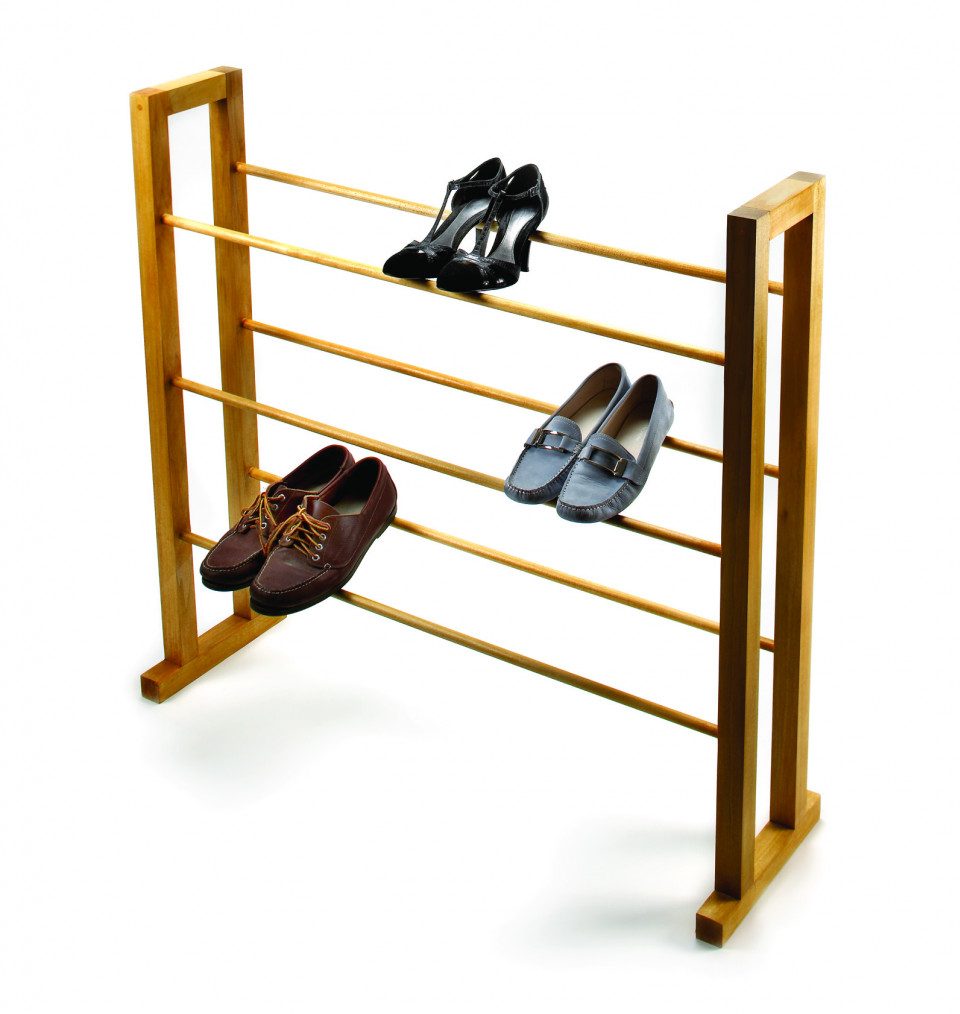
Vertical shoe storage. This cheap and simple-to-build shoe rack can be easily customized to fit any space or shoe-storage needs. And, it’s a lot more solid than the plastic ones you’ll find in most home-storage stores.
This simple rack uses no nails, no screws and holds up to 15 pairs of shoes.
In this “I Can Do That” column, we introduce the use of pegs instead of hardware to hold the project together.
This simple shoe rack uses five pieces of 2″ x 2″ x 36″ poplar (which is actually 1 1⁄2“ square) for the uprights, feet and rails; six 5⁄8” x 48″ poplar dowels for the crossbars; and one 3⁄8“ x 48″ poplar dowel for the pegs.
A good lesson when working with dowels is that not all of them are created equal. Before you start, measure your dowel diameters then select the drill bit to match the smallest one. (Although I bought 5⁄8“ dowels, three of them were actually closer to 9⁄16“.)
First, cut the crossbars to length. I decided on a 36″ span, long enough to hold five pairs of women’s dress shoes. With six dowels to cut to the same length, measure and mark one, then set up a stop-block on the miter-saw fence and cut each to 38″. The additional 2″ is to seat the dowels 1″ at both ends in the uprights.
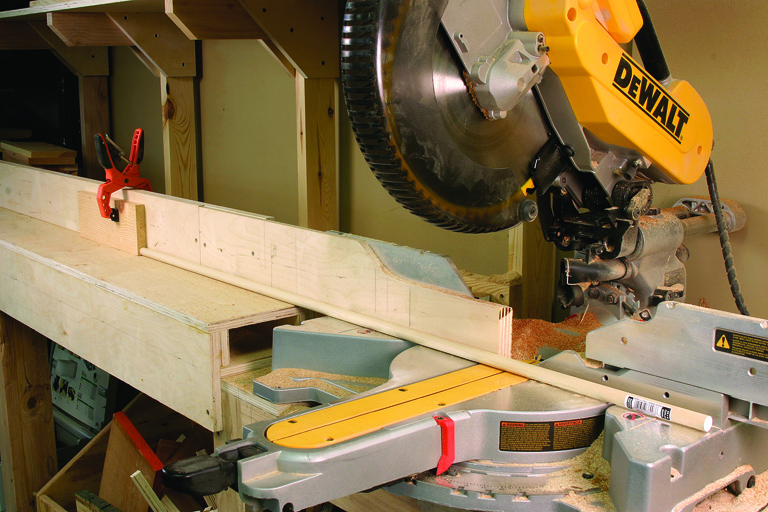
Stop-block. Here, I’ve set up a stop-block on the miter saw fence with a piece of offcut and a spring clamp. This saves a lot of time by not having to measure and mark each piece.
While at the miter saw, cut your two 12″ feet and two 5″ rails – again, with a stop-block. Then, pencil a line on the right-hand side of your fence at 21⁄2“, and cut 16 21⁄2“ pegs from the 3⁄8“ dowel (only 12 are needed, but extra is never bad). Holding the dowel in place against the fence on the left side and cutting these short pieces to the right side of the blade keeps your hands safely away from the blade. Once your pegs are cut, slightly taper one end on each a bit to make them easier to drive into place. An old-fashioned pencil sharpener on its largest setting works well for this task.
The uprights are 36″ in length so no cutting is needed on these.
Next, align the two feet and clamp them together to lay out the locations of the four uprights and the dowels to join them. First, measure 2″ from either end and use a combination square to mark a line across both pieces; then measure 11⁄2” from those marks and strike another line across both pieces. Mark a diagonal line from corner to corner of the resulting squares on each foot. I eyeballed the placement (along the diagonal line) for each of the four 3⁄8” pegs that are driven through each foot to seat into the bottom ends of the uprights.
Now move on to the layout of the crossbars in the uprights. Again, it’s important that they align perfectly across the width. Clamp the two back uprights together and mark across both simultaneously for the crosspiece locations at 10″, 20″ and 30″ up from the bottom. Mark the center point in each location (3⁄4” from either edge). The crosspieces in the front uprights are offset down 11⁄2” from those in the back. Clamp one of the uprights lengthwise (marked side up) securely in your Workmate, chuck the appropriate bit in your drill, put a piece of tape 1″ from the tip of your bit to act as a depth stop, and drill a 1″-deep hole in each marked location on the upright, then repeat on each.
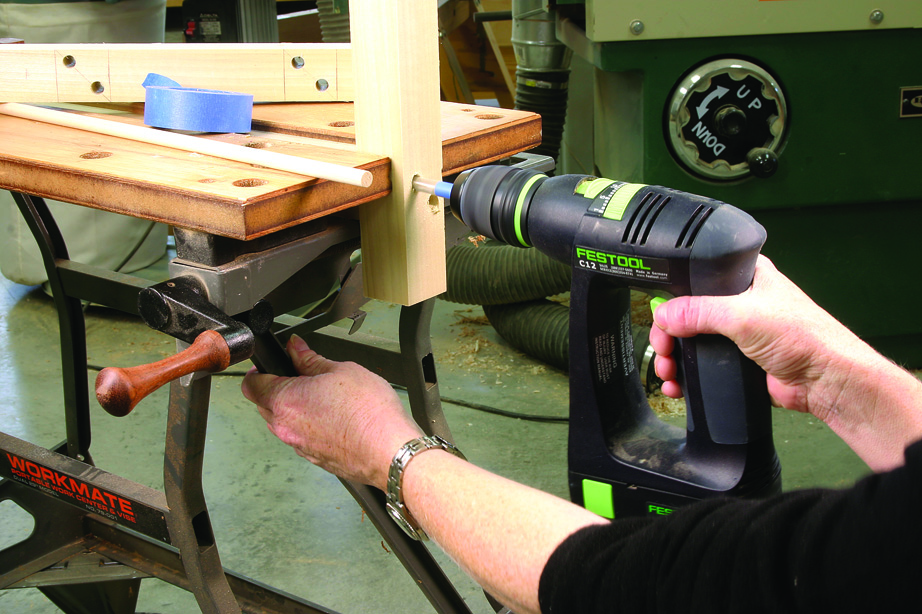
Drill straight. As you drill through the foot into the bottom of the upright, keep your drill level.
Then clamp each of the feet securely to drill through-holes that match the size of your pegs in all eight marked locations. Keep your drill level for this operation; you’ll be using the foot as a jig to drill the corresponding 1″-deep holes into the ends of the uprights, and you need these to align straight.
Now clamp the two front uprights together with your already-drilled holes facing down, and mark the location for 3⁄8“ through-holes at the top, 3⁄4” down from the top edge, and 3⁄4” in from either side, then drill straight through. As on the feet, this hole will be used as a jig to drill corresponding 1″-deep holes in the two top rails between the uprights.
Now clamp one of the back uprights loosely lengthwise in the Workmate vise with the holes along the length facing upward, leaving enough room at the bottom to align the foot with the layout marks you made, then clamp everything tightly together. Wrap a piece of painter’s tape 21⁄2” from the bit tip to mark the hole depth. Use the through-holes in the feet as a guide to drill two 1″-deep holes into the bottom of the upright.
Before you unclamp this setup, put glue in the holes and drive the two pegs in with a hammer or mallet. Try to seat the pegs completely so you have sufficient holding force between the two pieces (if you’ve a bit of peg sticking out, you can later sand it flush). Clamp the corresponding front upright (holes facing down) to the foot, drill your holes and seat the pegs. Do the same with the other side.
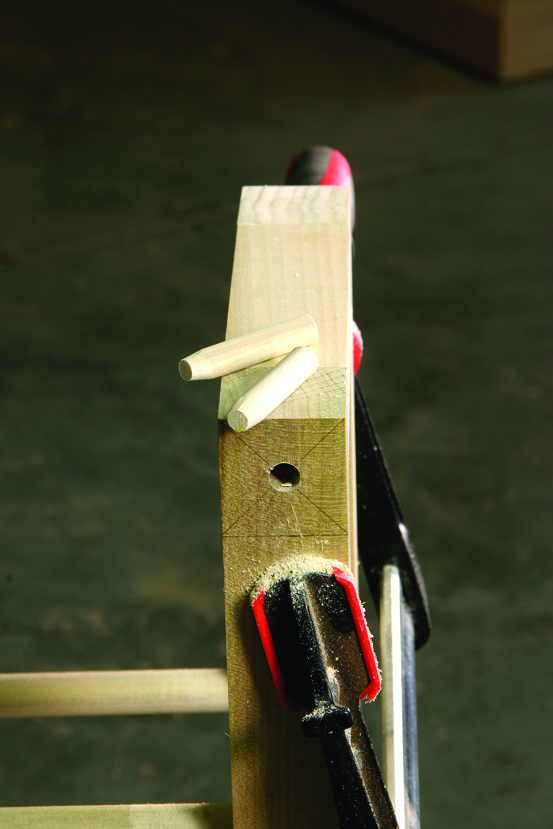
Final alignment. The last step is to clamp the rails in place, drill, add glue then seat the pegs. You’ll need to brace the rack against a solid surface as you seat the pegs; otherwise, the rack will move with each tap – and the pegs won’t.
It’s time to add the crosspieces. Lay one assembled side flat on the ground, holes facing up, and dry-fit your dowels. Remember – some of your crosspieces may be a bit larger than your holes, so you may need to sand them to fit. When all the dowels fit, add glue to the holes, and seat the dowels with a hammer.
Now grab the other side assembly, smear glue around the holes and line up the crosspieces in their corresponding holes. Once you have the side aligned, hammer the side down until the crosspieces are seated; let the glue dry. (If you have long enough clamps, use them to pull everything tight together.)
Add the rails, using the through-holes in the uprights as guides. Once you have the rails in place to square everything up, clamp them tightly and drill through the uprights 1″ into the holes. Brace your rack against something solid so you can swing your hammer with enough force to seat the pegs and not just scoot the rack across the floor with each whack.
Sand all surfaces (and any proud pegs flush) before finishing. I used two coats of amber shellac, sanding with #360 grit between coats. Shellac can be tricky to work with though; it dries very quickly so it’s hard to keep a wet edge and get a uniform coat. If I build another shoe rack, I’ll likely succumb to the siren’s call of spray paint or spray lacquer.
Pegged Shoe Rack Cut List
No. item dimensions (inches) material
T W L
❏ 4 Uprights 1 1⁄2 x 1 1⁄2 x 36 Poplar
❏ 2 Feet 1 1⁄2 x 1 1⁄2 x 12 Poplar
❏ 2 Rails 1 1⁄2 x 1 1⁄2 x 5 Poplar
❏ 6 Crossbars 5⁄8 dia. 38 Dowel
❏ 12 Pegs 3⁄8 dia. 2 Dowel
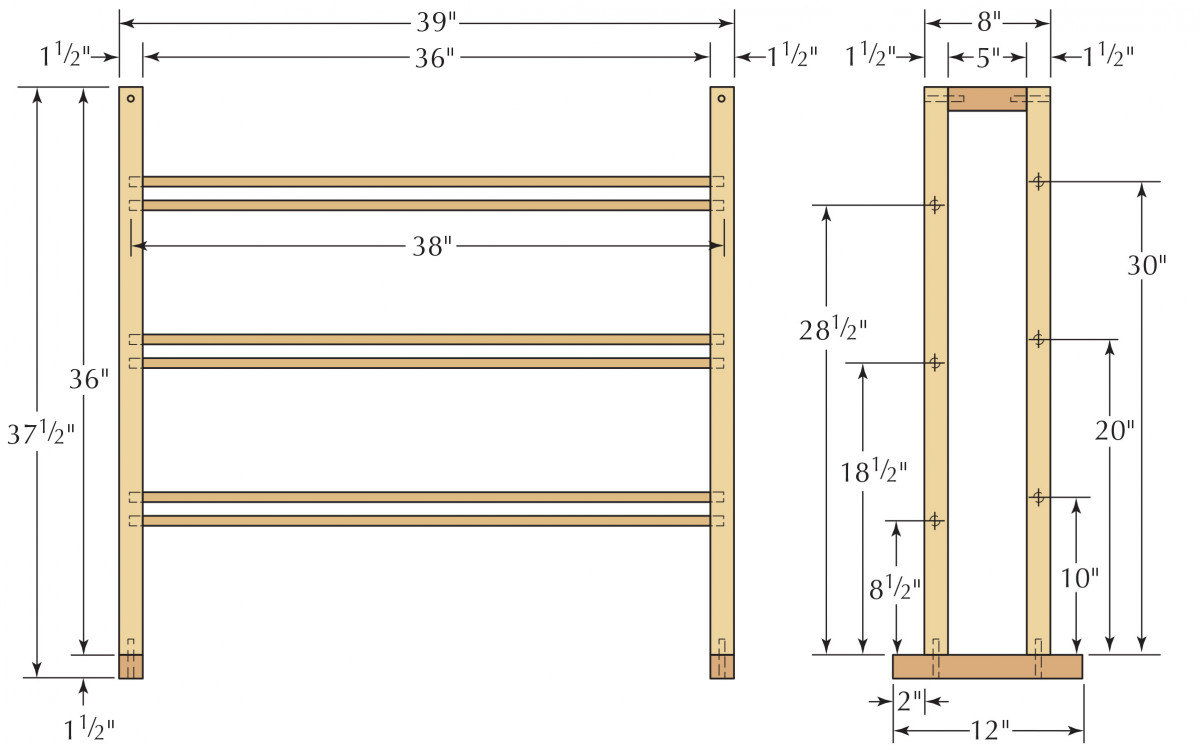
Elevation & profile
Here are some supplies and tools we find essential in our everyday work around the shop. We may receive a commission from sales referred by our links; however, we have carefully selected these products for their usefulness and quality.
Megan,
I am an intermediate woodworker, and this looks like a fine project to cut down to fit our bedroom closet. The house is an old (1935 Model Sear’s Mail-order) house built by a carpenter/plumber from The Bud Company in Phila, PA from the plans of a friend at work during WW II. We have made very few changes during our stay in the last 33 years, but this will help me organize our shoe collection.
Thank you,
Jim Childress
1330 Bernard Ave.
Willow Grove, PA.