We may receive a commission when you use our affiliate links. However, this does not impact our recommendations.
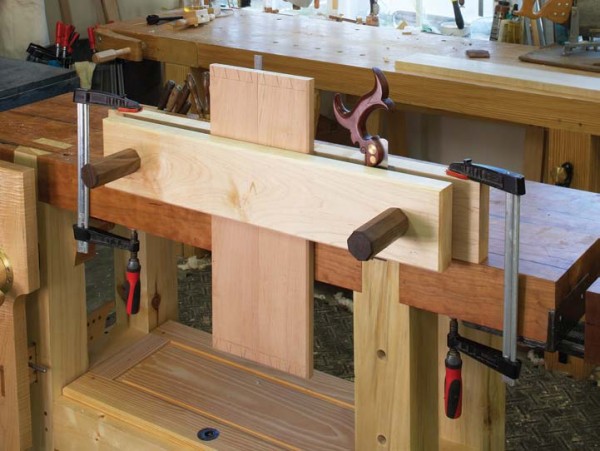
Back to the future. This vise might not have originally been intended for cutting dovetails, but boy is it great for it. It raises your work, then stows away when you don’t need it.
17th-century design saves your 21st-century back.
by Christopher Schwarz
pages 64, 66
If you cut dovetails by hand, then I’m sure you’re aware of the other part of your anatomy that is involved: your back.
Bending over rows of tails and pins all day is murder when you try to stand up straight. Several people have come up with solutions, including a cute mini-bench that you park on your full-size bench to raise your work. Other woodworkers have built benches with higher benchtops that are designed just for hand-joinery.
Of course, like most things in woodworking, someone had already come up with the solution several centuries ago.
‘Mechanick Exercises’
Joseph Moxon wrote the first English-language book on woodworking titled “The Mechanick Exercises” in1678. In it he showed many of the tools used by the contemporary joiner, from the workbench down to the dividers.
In one part of his book he discusses the “double-screw” vise. It looks like a twin-screw vise with two jaws that has been affixed to the front of a workbench.
But the text discusses how the vise can also be clamped down to the top of the workbench.
When that piece of information sunk in, I got excited and built a prototype. After a few revisions, here is what I came up with.
This vise solves a lot of problems that we joiners have. It allows you to hold stock of almost any size (mine holds up to 24-1⁄8″-wide material) with an incredible grip. More so, it raises your work above your benchtop surface. The vise as shown is 6″ high, so the top edge of the vise is 39″ from the floor.
The board I’ve clamped in the vise is 44″ off the floor and is as stable as something clamped between two boulders. What does that mean?
No more stooping to saw dovetails, tenons or other joinery.
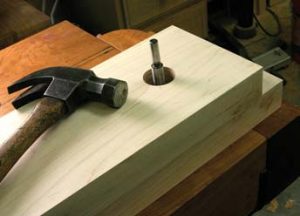
Tap then tap. Place the front jaw on the rear jaw. Drop your Forstner in the hole. Tap it with a hammer. Then drill the hole in the rear jaw and tap that.
And because the vise is portable, that means I can:
1. Put the vise wherever I want on the bench – the end, the back edge, wherever.
2. Remove it when I don’t need it and hang it on the wall – most woodworkers don’t need a twin-screw vise every day.
3. Leave it unclamped on the benchtop, and use it like a giant handscrew clamp (Peter Follansbee hipped me to this function).
The vise is quite easy to build – I used some scraps. The only other key piece of shop equipment is an 1-1⁄2″ wooden thread box and tap, which is available at many suppliers for less than $50.
Tap the Jaws
The first step is to cut the 1-1⁄2″-diameter clearance holes in the front jaw. Position the holes so you’ll have 24-1⁄8″ between them. Then center the front jaw on the rear jaw and clamp them together. (Note: The front jaw is wider than the rear jaw so that it is easier to line up the rear jaw with the front edge of your benchtop.)
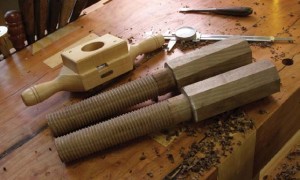
Two screws from one stick. The two vise screws are made from one octagonal piece. Turn down the middle. Cut the piece in half. Thread the round sections.
Drop a 1-1⁄2″ Forstner bit into each hole and tap the end with a hammer – this transfers the centerpoint of the hole to the rear jaw.
Unclamp the jaws and drill 1-3⁄8″ holes though the rear jaw. Then use your tap to tap the holes in the rear jaw (a little linseed oil or a non-drying vegetable oil makes a good lubricant).
Turn & Thread the Screws
The vise’s screws are made from 2″ x 2″ walnut. I planed a 25″-long section to an octagon then chucked that in the lathe. I turned the middle 14″ down to just a shade less than 1-1⁄2″. Then I crosscut the piece, ending up with two 12-1⁄2″-long handles.
Clamp a vise screw with the round section facing up and use your threadbox to thread the round section. Test the results in the rear jaw. If the screw squeaks or doesn’t turn freely, adjust the cutter in the threadbox so it cuts slightly deeper.
Add the Rear Brace
The vise will be more stable if you glue a rear brace on the backside of the rear jaw, which will increase the surface area that contacts your bench. Glue and clamp the rear vise in place.
Add some details if you like. I chamfered the front edges of my front jaw and the ends of the vise screws. I applied a couple coats of an oil/varnish blend finish. I also glued on a layer of suede to the inside face of the front jaw, which improves the vise’s grip even more.
I’ve been testing the vise for more than three months (and I made versions for co-workers and friends). If you cut dovetails, I think this vise is well worth making. Your back will thank me. PWM
For the cutlist, and plan and profile illustrations, download the PDF below:
MoxonBenchVise
The article above is from the December 2010 issue of Popular Woodworking Magazine.
Here are some supplies and tools we find essential in our everyday work around the shop. We may receive a commission from sales referred by our links; however, we have carefully selected these products for their usefulness and quality.